Batteriemanagement
über
Was ist bei Lithium-Akkus so besonders, dass sie anders als die anderen gängigen Akku-Technologien zwingend ein elektronisches Akkumanagement benötigen? Um diese Frage und den Umgang damit geht es im nachfolgenden Text.
Nicht-Lithium-Technik
Blei
Wie war das weiland mit Blei-Akkus doch simpel: Man drückte so viel Strom wie zulässig oder verfügbar in den Akku und hörte damit auf, wenn die Ladeschlussspannung (ab jetzt: LSS) erreicht wurde. Und Akkus aus mehr (in Serie geschalteten) Zellen? Auch kein Problem. Einfach die LSS mit der Zellenzahl multiplizieren und die Sache war geritzt. Das gilt noch heute.
Warum klappt das? Einfach deswegen, weil Blei-Säure-Akkus beim Überladen nicht gleich kaputt gehen (sondern höchstens etwas ausgasen). Wenn eine der Zellen eines Akkus daher etwas weniger Kapazität als der Rest aufweisen sollte, kann man die restlichen Zellen eben trotzdem auf die passende LSS aufladen. Diese Robustheit sorgt dafür, dass fast alle Autos auch heute noch eine 12-V-Bord-Batterie in eigentlich anachronistischer Blei-Technologie besitzen, obwohl andere Akkutypen ordentlich Gewicht sparen würden. Ein mit Blei-Akkus bestückter Laptop würde eindeutig zum Schlepptop. Trotzdem: Diese Akkus sind so robust, dass man eine Standard-44-Ah-Autobatterie für einen Kleinwagen locker jahrelang mit einer 55-A-Lichtmaschine mit Primitivregler quälen kann, was schon sehr eindrucksvoll ist.
Bekanntlich beträgt die typische Zellenspannung 2 V. Die LSS liegt bei etwa 2,35…2,4 V/Zelle, was sich für die sechszellige Autobatterie auf 14,1…14,4 V summiert. Eine Blei-Akkuzelle sollte nicht unter 1,8 V entladen werden. Ergo nimmt eine Autobatterie Schaden, wenn sie unter 10,8 V gerät, so wie das durch die Selbstentladung von etwa 5%/Monat z.B. bei Motorrädern passieren kann, wenn man sie im Winter nicht zwischendurch einmal auflädt.
Nickel-Cadmium
Sogenannte NiCd-Akkus in Rundzellen wurden vor allem als Ersatz für Zink-Kohle-Batterien in Geräten der Unterhaltungselektronik populär. Mittlerweile ist dieser Akkutyp aufgrund der Umweltschädlichkeit des enthaltenen Cadmiums in der EU schon über 10 Jahre verboten. NiCd-Akkus sind mittlerweile aus dem Alltag verschwunden, weshalb sich viele Worte hier nicht lohnen.
Kurz zu den Eigenschaften dieser Akku-Technologie: NiCd-Akkus vertragen recht hohe Ströme und viele Ladezyklen, weshalb sie früher gerne für Modell-Autos etc. eingesetzt wurden. Auch hier gibt es eine Nominalspannung, nämlich 1,2 V pro Zelle. Geladen wird ähnlich wie beim Blei-Akku bis zur LSS von 1,5…1,57 V/Zelle (je nach Strom). Tiefentladung unter 0,85 V/Zelle schadet dem Akku, auch wenn dieser noch wesentlich robuster als ein NiMH- oder Lithium-Akku ist. Die Selbstentladung reicht bis zu heftigen 20%/Monat. Eine Serienschaltung beim Laden ist kein Problem – ergo ist kaum Management erforderlich.
Nickel-Metallhydrid
Kleine NiMH-Rundzellen wie z.B. der AA-Typ von Bild 1 haben als ungiftige Alternative das Erbe der NiCd-Akkus angetreten.
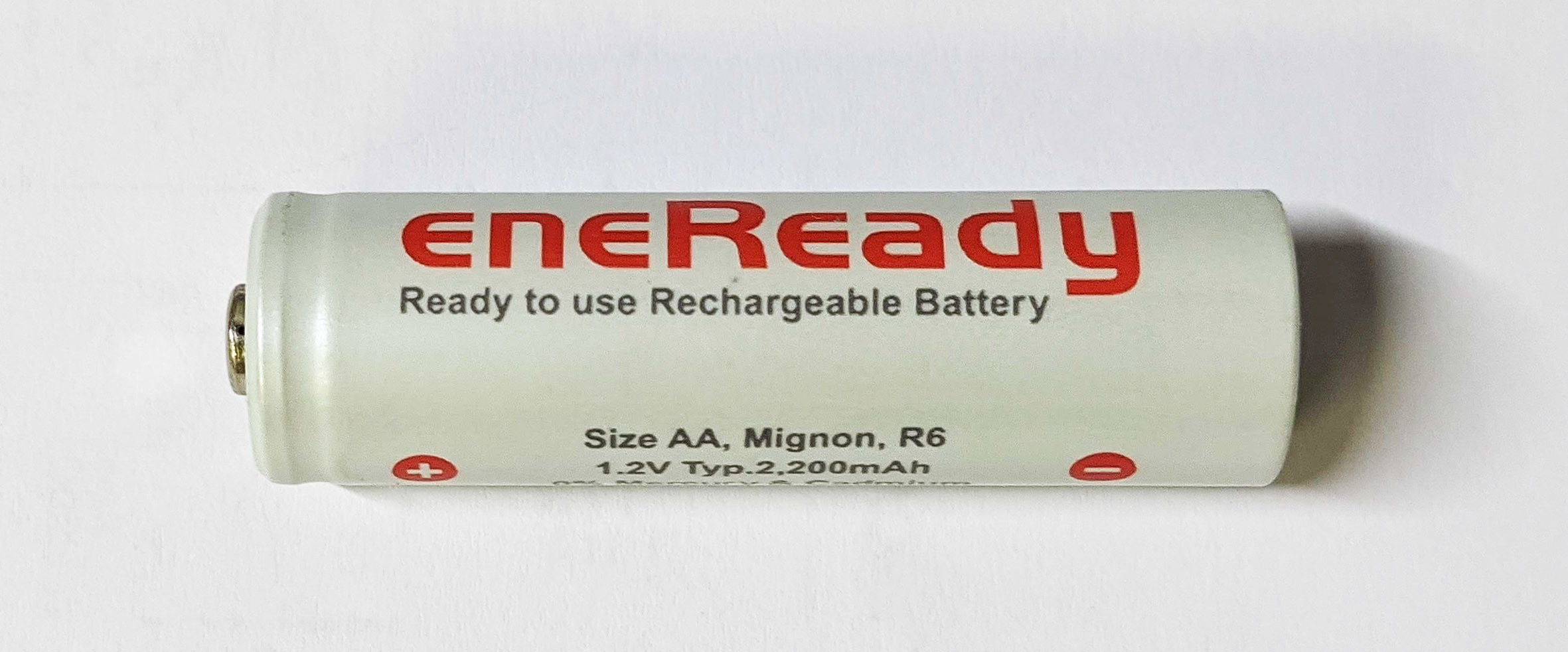
Aber es gibt sie nicht nur in klein: Jahrelang waren sie z.B. in akkubetriebenen Werkzeugen aufgrund des günstigen Preises und des einfachen Handlings Standard. Es gibt sie sogar nicht so selten noch als größeres Modell: Der „Prototyp“ aller Hybrid-Autos, der Toyota Prius, war bei den Modellen II und III mit einem fast einen Zentner schweren NiMH-Akku mit rund 200 V und etwa 6,5 Ah bestückt. Dieser erreicht in solchen Autos enorme Lebensdauern und Zyklenzahlen, die auf ein Management des Lade- und Entladeverhaltens und der Ausnutzung lediglich einer Teilkapazität beruhen. Bild 2 zeigt die geöffnete Batterie meines ehemaligen Prius II.
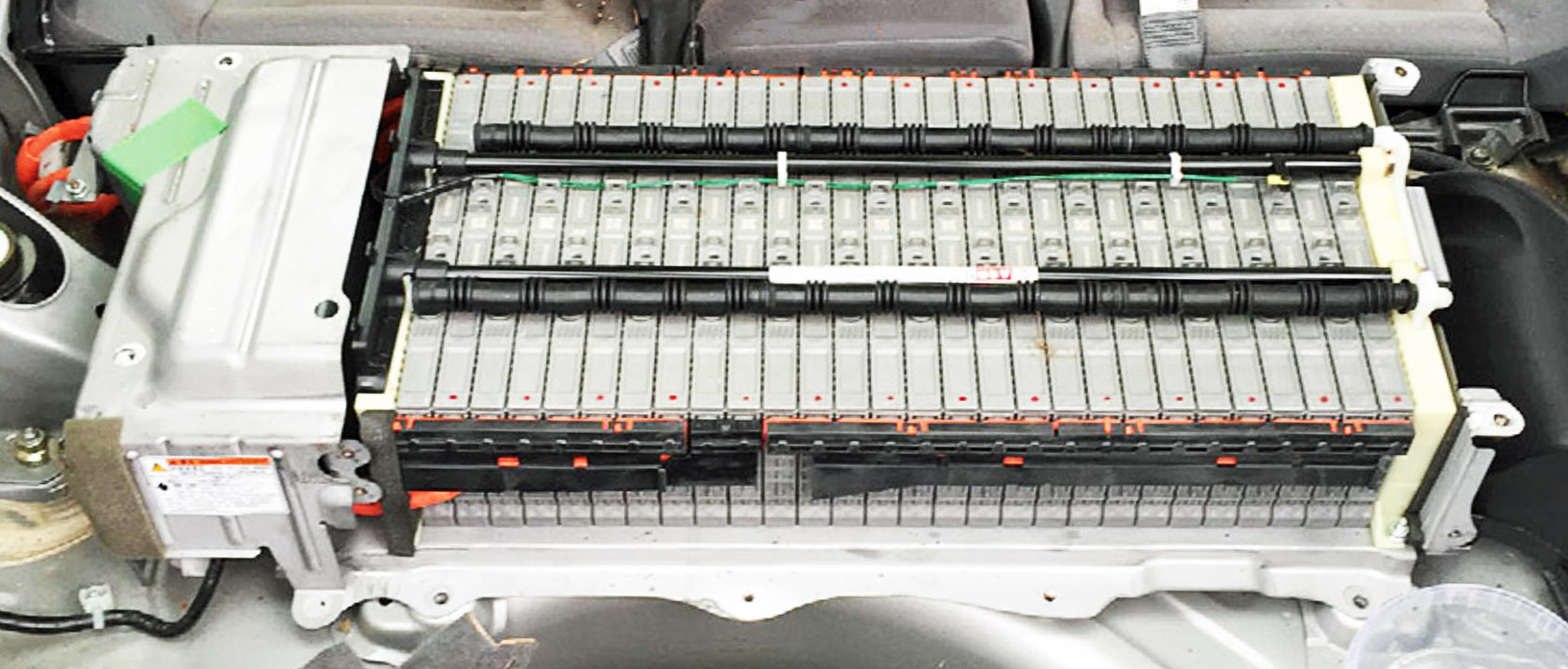
Bei Plug-in-Hybriden und neueren Hybrid-Modellen ist Toyota und auch alle anderen Hersteller aufgrund der Gewichtsersparnis dann doch auf Lithium umgestiegen, nachdem die mit dieser Technologie verbundenen Probleme anscheinend gut genug gelöst werden konnten.
Die Selbstentladung von NiMH-Akkus ist (normalerweise) ähnlich hoch wie bei NiCd-Typen. Allerdings gibt es Varianten wie der Akku in Bild 1, die auf Kosten der Leistungsdichte eine sehr viel geringere Selbstentladung von etwa 1,5%/Monat aufweisen. Für seltener genutzte Gadgets sind diese Akkus immer vorzuziehen, da tiefentladene NiMH-Akkus unbrauchbar werden.
Lithium
Akkus auf Lithium-Basis verdrängen zunehmend alle anderen Akkutypen in den meisten Anwendungsgebieten, da sie bekanntlich das bessere Leistungs- und Volumengewicht und eine extrem niedrige Selbstentladung von etwa 5%/Jahr aufweisen. Doch kein Licht ohne Schatten: Die sogenannten LiIon-Akkus (Lithium-Ionen) sind sehr empfindlich gegen Überladung und Tiefentladung. Sie verlieren dabei nicht nur Kapazität, manche Typen können durchaus platzen oder gar in Flammen aufgehen. Nur um es erwähnt zu haben: Bei geringen Temperaturen sinkt die verfügbare Kapazität. Auch wenn Letzteres reversibel ist, so ist das doch ein Problem für damit betriebene Elektro-Autos. Hohe Temperaturen bekommen LiIon-Akkus ebenfalls nicht.
Aufgrund der Empfindlichkeit gegen Überladung ist bei einer Serienschaltung für höhere Spannungen Vorsicht geboten. Es braucht hier auf jeden Fall zusätzliche Elektronik in Form eines sogenannten Balancers, der beim Laden verhindert, dass einzelne Zellen mit zufällig etwas geringerer Kapazität schon überladen werden, wo die anderen Zellen noch nicht ganz voll sind. Und es gibt noch mehr Faktoren zu berücksichtigen. Auf jeden Fall dürfte klar sein, dass LiIon-Akkus immer zwingend ein Batteriemanagementsystem (das Akronym BMS passt auch im Englischen) mit zum Teil komplexen Eigenschaften benötigen.
Was die Sache noch komplizierter macht ist, dass es nicht nur einen Typ von Lithium-Akkus gibt. Je nach verwendeter Technologie und interner Chemie variieren die möglichen Zyklenzahlen, die TZS (typische Zellenspannung), die LSS, die ELSS (Entlade-Schluss-Spannung), der maximale Entladestrom und weitere Kenngrößen. Die BMS müssen auf diese Parameter und natürlich die im konkreten Fall zu beherrschenden Ströme und Temperaturbedingungen abgestimmt sein.
Wenn man von Elektroautos absieht, für die besondere Bedingungen gelten und bei denen auch enormer Aufwand zum Schutz der teuren Akkus betrieben wird, ist die Sache bei kleineren Batteriesystemen etwa für tragbare Geräte wie Laptops oder Bluetooth-Lautsprecher, Werkzeuge wie Akkuschrauber oder Haushaltsgeräte wie Akkusauger doch zum Glück etwas einfacher, da Kühlung und Heizung entfallen. Am einfachsten ist die Sache übrigens bei Smartphones, denn die enthalten keine in Serie geschalteten Akkuzellen, weshalb kein Balancer nötig ist. Die integrierte Ladeelektronik muss lediglich die LSS und die ELSS sowie den maximalen Ladestrom berücksichtigen.
Bei den kleineren LiIon-Akkus dominieren zwei Kategorien: Auf der einen Seite Typen, deren Elektroden mit den Werkstoffen Cobalt, Cobalt-Dioxid, Mangan und/oder Nickel und Aluminium gebaut sind. Der Löwenanteil entfällt hier auf die bewährte LiCoO2-Technik. Glücklicherweise beträgt bei all diesen Typen die TZS etwa 3,6…3,7 V, die LSS 4,2 V und die ELSS 2,5 V (Ausnahme: bei LiNixCoyAlzO2 ist die ELSS 3,0 V). Auch wenn sich die erlaubten Ströme und die Lebensdauer unterscheiden, lassen sich all diese Typen im Prinzip mit den gleichen Verfahren = den gleichen ICs managen.
Abweichend hiervon ist der Akku aus Lithium-Eisenphosphat (LiFePO4), bei dem gilt: TZS = 3,2 V, LSS = 3,65 V und ELSS = 2,5 V. Dieser Akkutyp bietet hohe Zyklenzahlen und eine etwas geringere Leistungsdichte. Man braucht hierfür also zumindest für diese Spannungen gedachte Balancer. Die Halbleiter-Industrie bietet selbstverständlich Lösungen für beide Kategorien und für verschiedene in Serie geschaltete Zellenzahlen und Ströme an – manche ICs sind sogar programmierbar, für bestimmte Parameter umschaltbar oder haben ein Interface für Mikrocontroller.
LiIon-Akkus gibt es in verschiedenen Bauformen: Die LiPo-Typen (Lithium-Polymer) sind aufgrund der möglichen Formen und ihrer Flachheit vor allem in Mobilgeräte und Laptops eingebaut. Der Begriff Polymer bezieht sich vor allem darauf, dass die LiPos statt in ein festes Gehäuse einfach in eine Kunststofffolie eingeschweißt sind – Knicke sind da unerwünscht. Dann existieren diverse Rundzellen, darunter besonders verbreitet der Typ 18650 (ø = 18 mm, Länge = 65 mm), der erstaunlicherweise zu Tausenden als Paket in Teslas Elektroautos verbaut wird – die Lücken zwischen den runden Zellen werden zum Temperaturmanagement genutzt. Bild 3 zeigt eine 18650-Zelle aus chinesischer Fertigung mit Fantasieangaben: Wie man sieht, ist nicht nur Papier, sondern auch Kunststoff und HTML sehr geduldig, denn 7.800 mAh passen noch lange nicht in das 18650-Format.
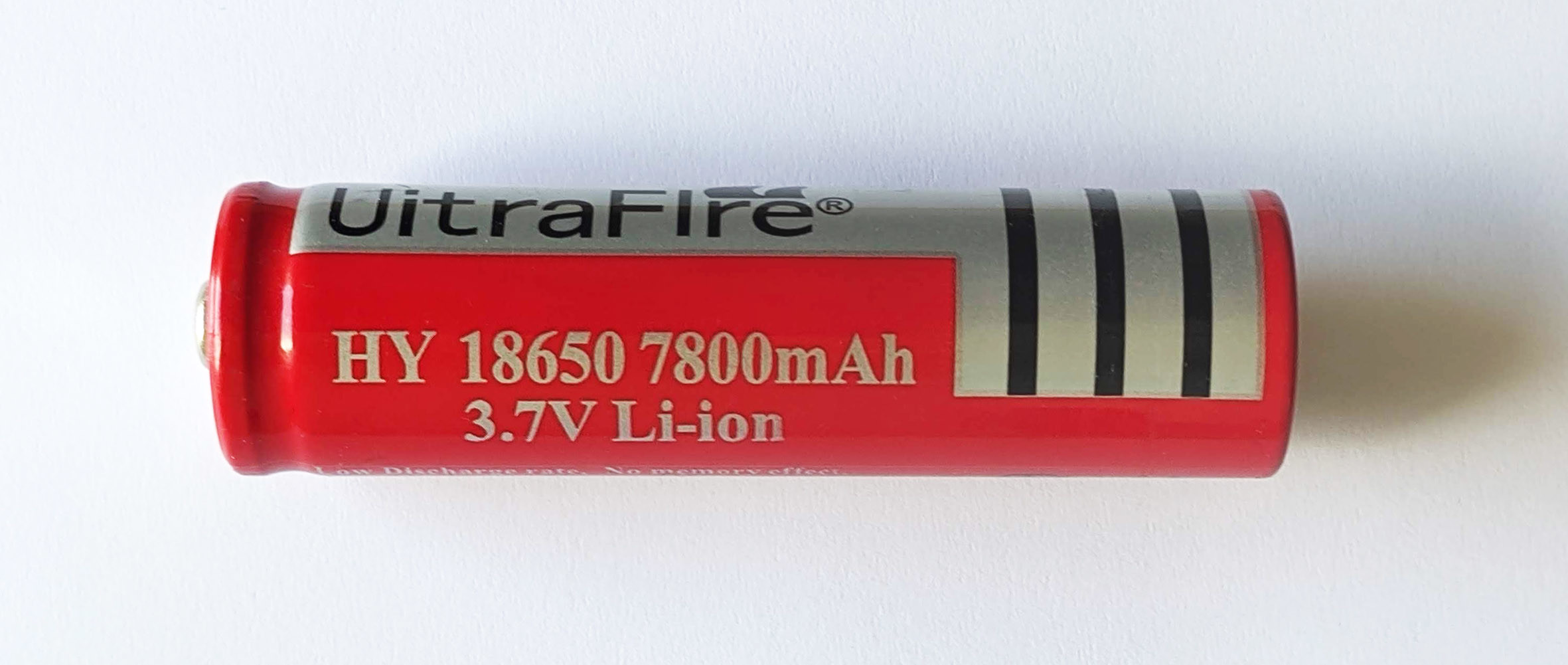
Die besten aktuellen Zellen kommen real etwa auf die Hälfte. Schließlich gibt es noch die sogenannten prismatischen Zellen, deren Bezeichnung lediglich darauf hinweist, dass ihr Gehäuse nicht rund, sondern quaderförmig ist. Solche Zellen sind z.B. im Mini-Auto „Hotzenblitz“ aus deutscher Produktion verbaut. In Bild 4 sieht man schön, dass jede Zelle mit extra Elektronik versehen ist, welche ihren Zustand überwacht.
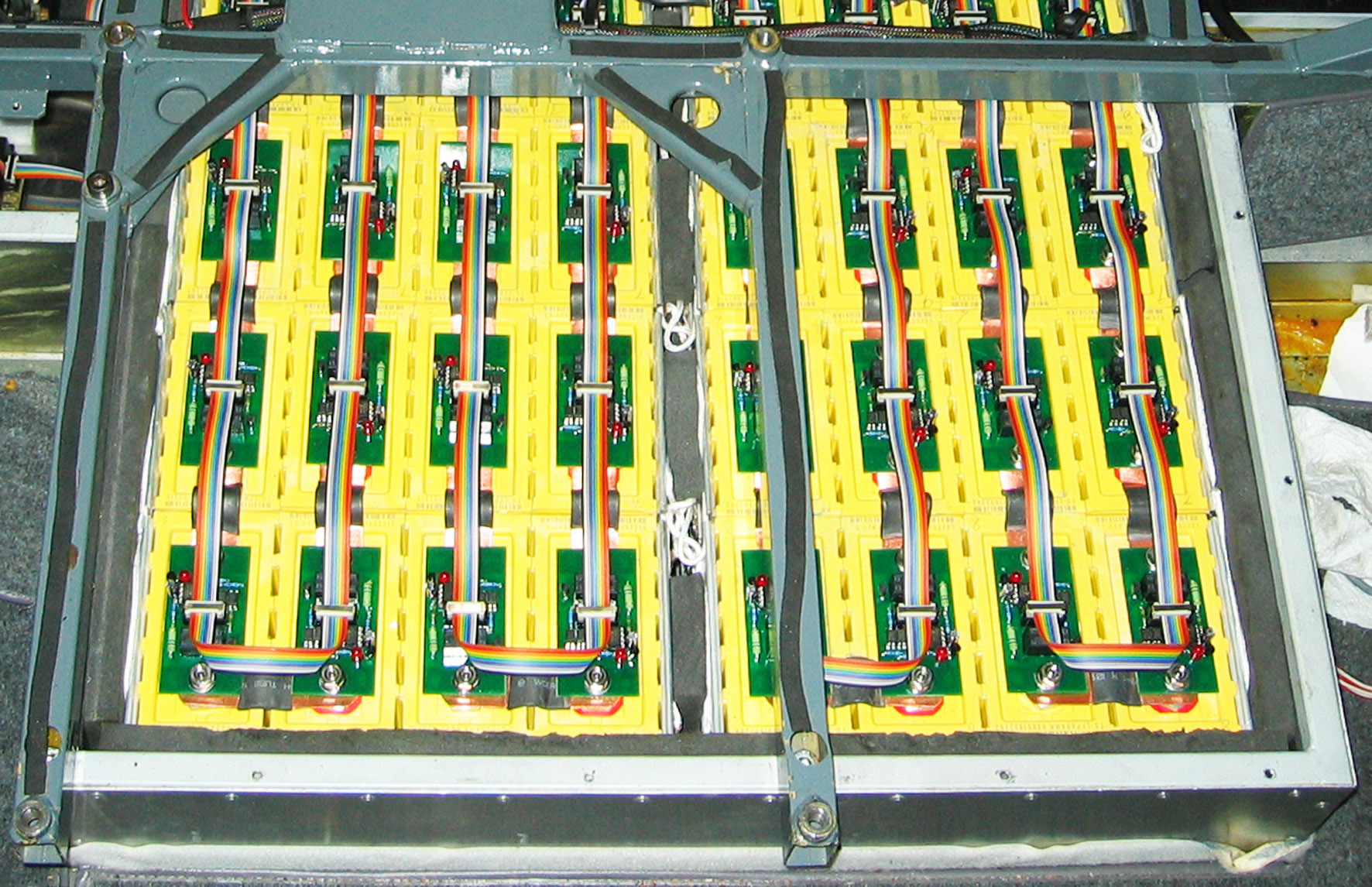
Balancer
Der Begriff „Batteriemanagment“ ist ja eigentlich recht schwammig. Er umfasst alles, was sich irgendwie mit der Überwachung und Steuerung des Ladens, des Entladens und des Betriebszustands von Akkus befasst. Während sich dies bei Blei-, NiCd-, und NiMH-Akkus lediglich auf die Einhaltung von LSS, ELSS und gelegentlich der Begrenzung von Strömen bezieht, ist die Sache aufgrund der Probleme mit der Serienschaltung von Zellen bei Lithium-Akkus komplexer. Hier braucht das BMS bei mehr als einer Zelle zwingend einen Balancer!
Der zentrale Grund hierfür ist, dass Lithium-Akkus Überladung gar nicht mögen. Und weil die Kapazität der Zellen auch bei Massenfertigung in einer Charge leicht variiert und Unterschiede auch durch Alterung auftreten können, gibt es bei einer Serienschaltung immer eine Zelle, die beim Laden zuerst voll ist. An dieser Stelle ist aber die LSS für den Gesamt-Akku noch nicht erreicht, und wenn dann weiter geladen würde, würde die schwache Zelle zumindest geschädigt – sie wäre dann beim nächsten Laden noch früher „fertig“ und ein circulus vitiosus wäre im Gang, der nach ein Paar Zyklen zumindest zum Ausfall der schwachen Zelle und damit des Akkus – wenn nicht zu Schlimmerem – führt. Ein Balancer verhindert das.
In der einfachsten Version bei einem Zwei-Zellen-Akku wie in Bild 5 überwacht der Balancer die Spannungen der beiden Zellen.
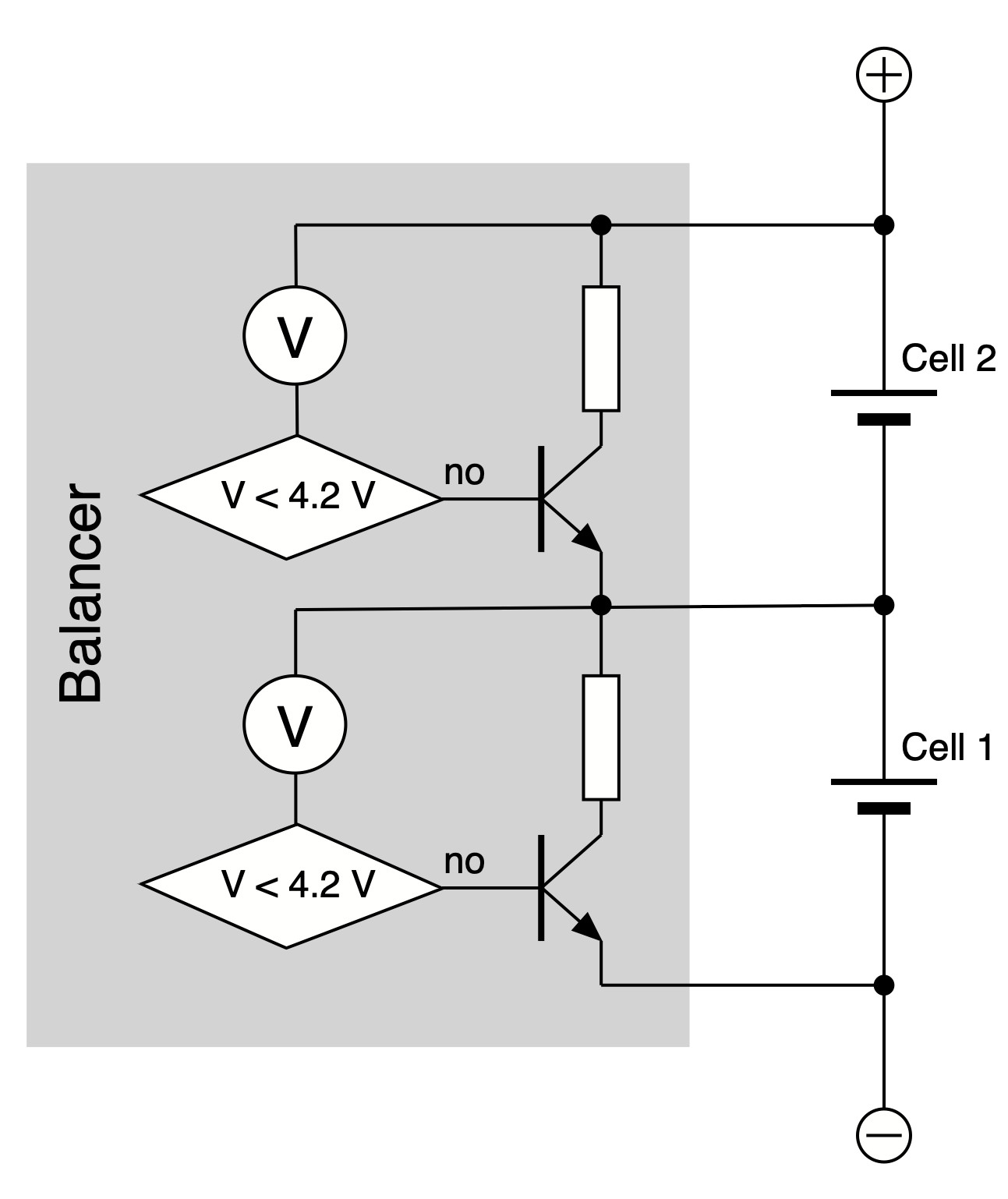
Erreicht eine der beiden Zellen die LSS, dann wird eine angemessen kleine Last parallel zur Zelle gelegt, damit der weitere Ladestrom quasi an dieser Zelle vorbei fließt und so immer noch die andere, bessere Zelle vollgeladen werden kann. Bei mehr Zellen skaliert man den Balancer entsprechend. Bild 6 zeigt eine kleine BMS-Platine für vier (kleine) Zellen, wie sie in eBay für unterschiedliche Zellenzahlen massenhaft für Preise zwischen 1 € und 10 € angeboten werden.
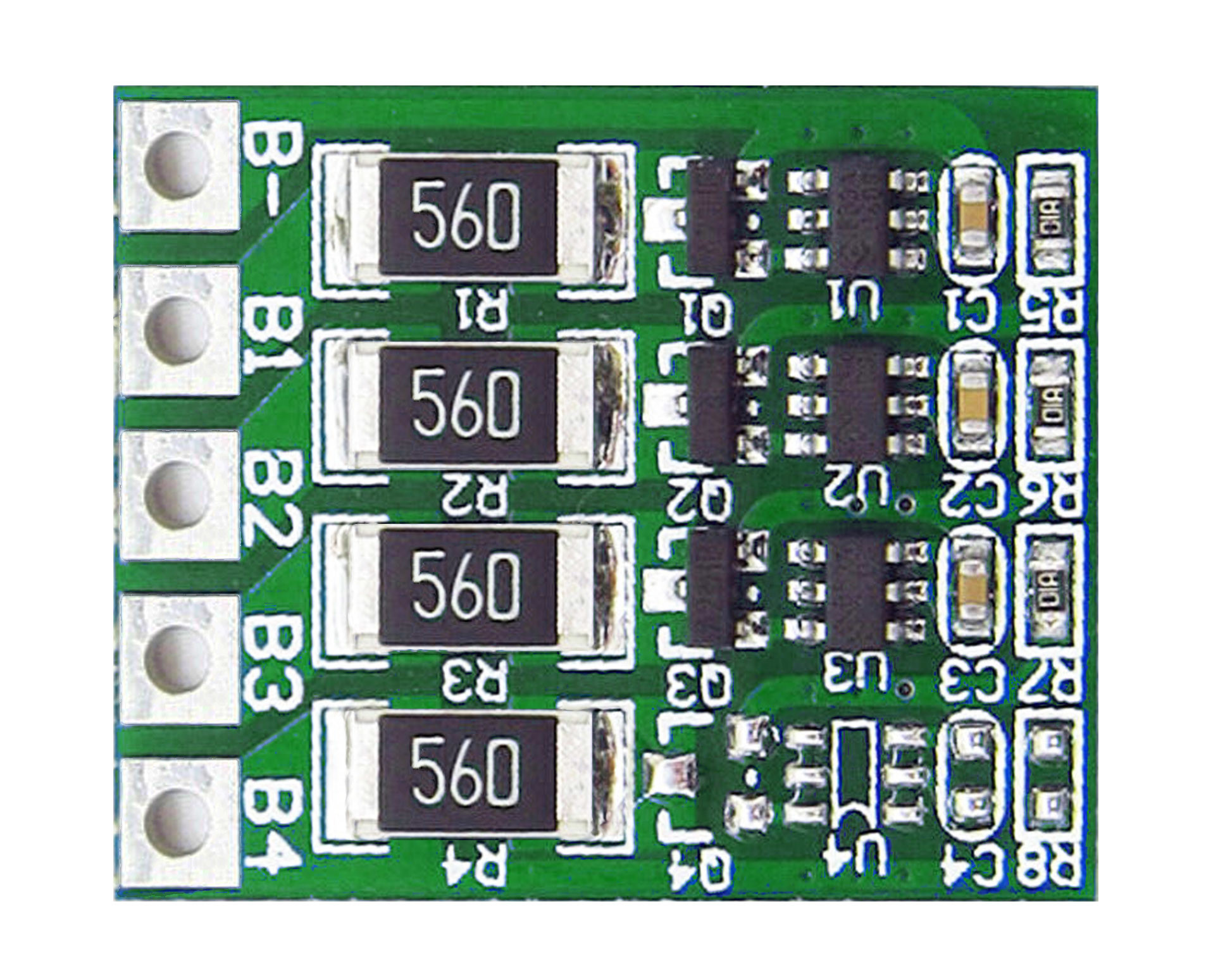
In Bild 7 kann man sehen, welchen Aufwand ich für den Balancer des 48-V-LiFePo-Akkus meines Segway-Clones getrieben habe: Jede Zelle wird von einem eigenen Mikrocontroller überwacht.
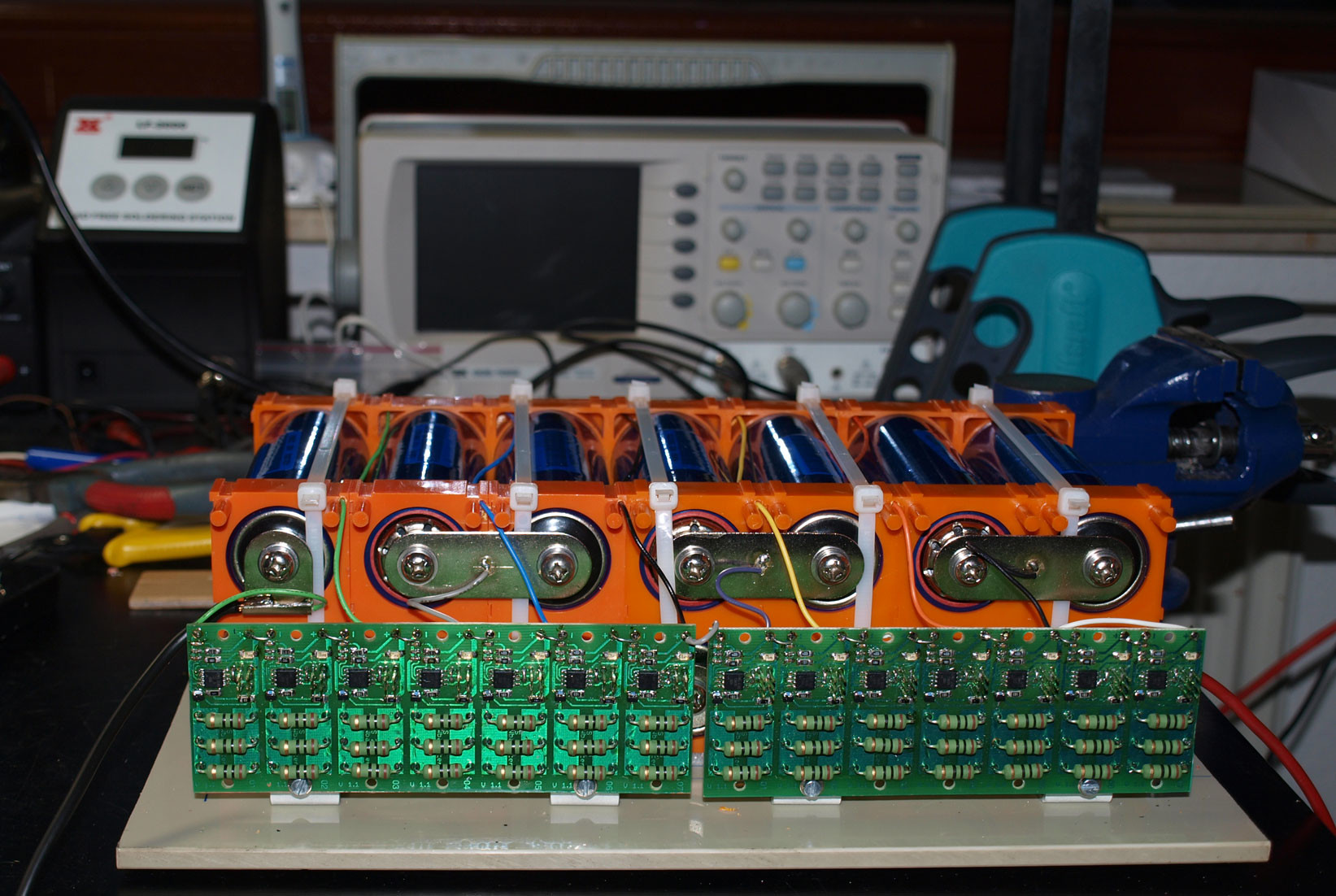
Man könnte nun einwenden: „Eine kleine Last?“ und hätte damit nur prinzipiell, aber nicht praktisch recht. Rein formal sollte die im Notfall parallel geschaltete Last zwar den vollen Ladestrom an der zu schützenden Zelle vorbeischleusen können, aber der ist praktisch deutlich kleiner als der maximal vorkommende Ladestrom. Hintergrund ist, dass LiIon-Akkus zwar am Anfang bis zu einem Ladezustand von 50…80% mit dem nominalen Strom geladen werden, ab dann aber nur noch mit einem kleinen, in der Regel stetig sinkenden Strom. Bei LiCoO2-Zellen ist der Strom jenseits von 3,95 V beim Laden ziemlich niedrig. Da die Unterschiede gesunder Zellen nicht sooo groß sind, reicht es, wenn man diesen deutlich geringeren Strom abführt. In der Praxis reichen dafür Zusatzlasten für etwa 1…5% des Maximalstroms fast immer aus. Reicht es mal nicht, ist eine Zelle „echt schlecht“ und ein höherer Ballast würde auf die Dauer auch nichts bringen.
Je nach den vorkommenden Strömen wird durch einen Balancer Energie vernichtet, die vielleicht besser doch genutzt statt verheizt werden kann. Für solche Zwecke gibt es Spezial-Balancer, welche die überschüssige Energie an der zu schützenden Zelle nicht einfach in Wärme umwandeln, sondern via Step-up-Schaltregler (pro Zelle!) direkt wieder dem Gesamtsystem zuführen. Eine solcher Aufwand wird aber verständlicherweise selten getrieben.
Noch ein anderes Kriterium ist wichtig: Balancer basieren auf elektronischen Bauelementen und integrierte Schaltungen lassen sich nicht ganz so einfach und vor allen Dingen nicht preiswert für hohe Spannungen bauen. Von daher stößt die mögliche Skalierung an praktische Grenzen. Moderne BMS-ICs gibt es typischerweise für 2…12 Zellen. Bei 12 Zellen hat man schon eine Betriebsspannung von gut 50 V. Will man mehr Zellen in einem Akku, skaliert man einfach die BMS-Elektronik. Bei den 800-V-Systemen moderner Elektro-Autos kommt man dann schon auf gut 20 Module mit 12s-BMS-ICs in Serie (das „s“ bei 12s steht für „Zelle“). Die einzelnen Subsysteme sind dann per (potentialgetrenntem) Bus miteinander und meistens mit einer zentralen Steuerung verbunden.
ICs
Wie schon erwähnt, bietet die Industrie eine Vielzahl spezieller ICs für alle denkbaren Anwendungsfälle – zu viele, um zu versuchen, hier eine brauchbare Übersicht zu geben. Stattdessen werden ein konkretes IC und seine Schaltung exemplarisch beschrieben. Doch vorab gibt es noch etwas nachzutragen.
Neben dem Balancing hat ein BMS bei den meisten Anwendungen mit Lithium-Akkus auch noch die Aufgabe, den Akku vor Unterspannung und Überstrom zu schützen. Manchmal ist auch die Ladeschaltung mit in das System einbezogen. Bei diesen komplexen Aufgaben macht der Einsatz eines Mikrocontrollers durchaus Sinn. Moderne BMS haben deshalb manchmal einen kleinen SoC integriert oder ein entsprechendes Interface. Man findet BMS-ICs deshalb nicht nur bei den üblichen Verdächtigen für analoge ICs oder Schaltregler, sondern auch bei Firmen wie etwa Microchip, Maxim (siehe Bild 8) oder Renesas.
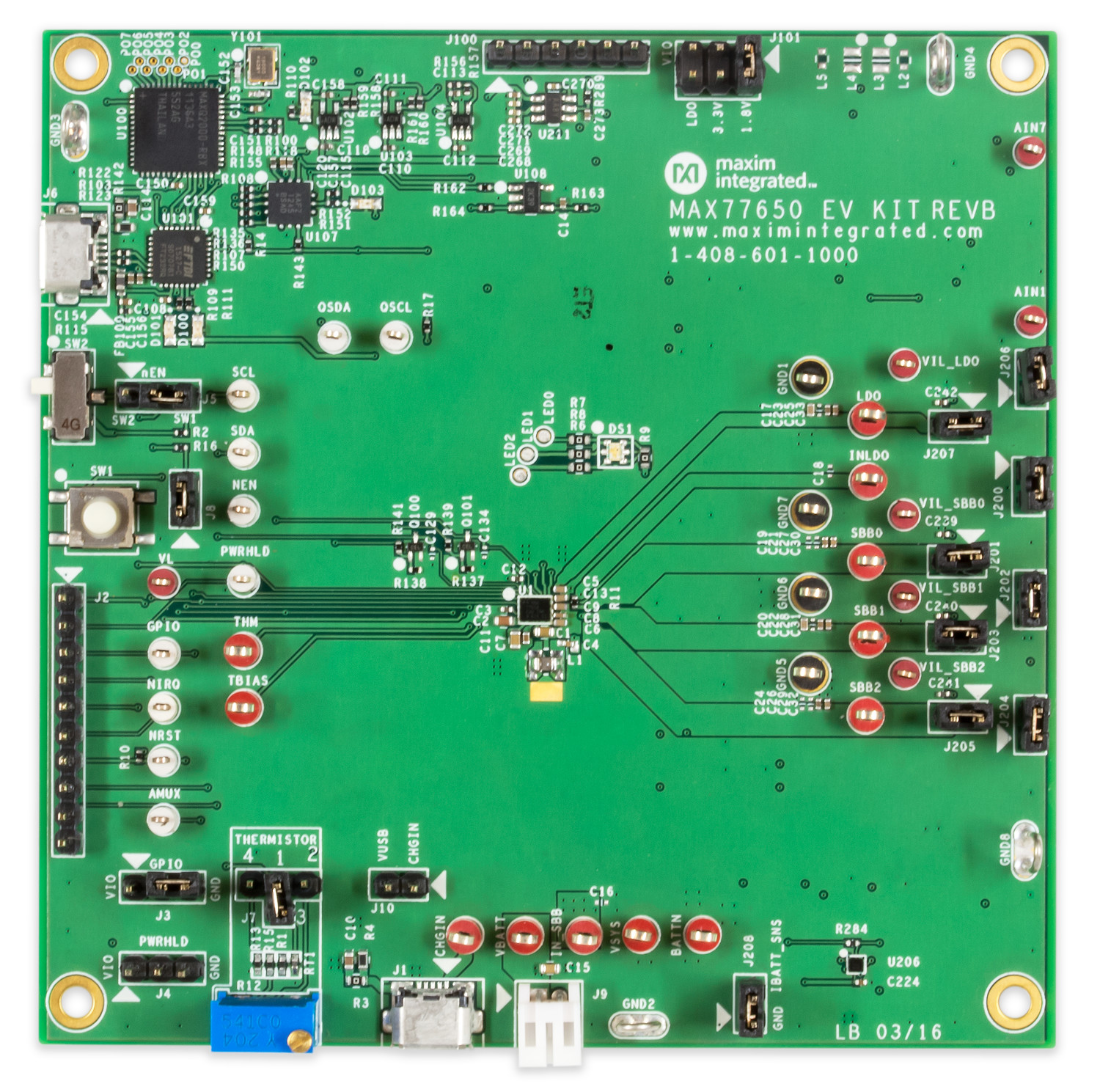
Und von letzterem vor allem für seine Mikrocontroller bekannten Hersteller stammt das Beispiel-IC.
Bild 9 zeigt das interne Blockschaltbild des BMS-ICs ISL94212.
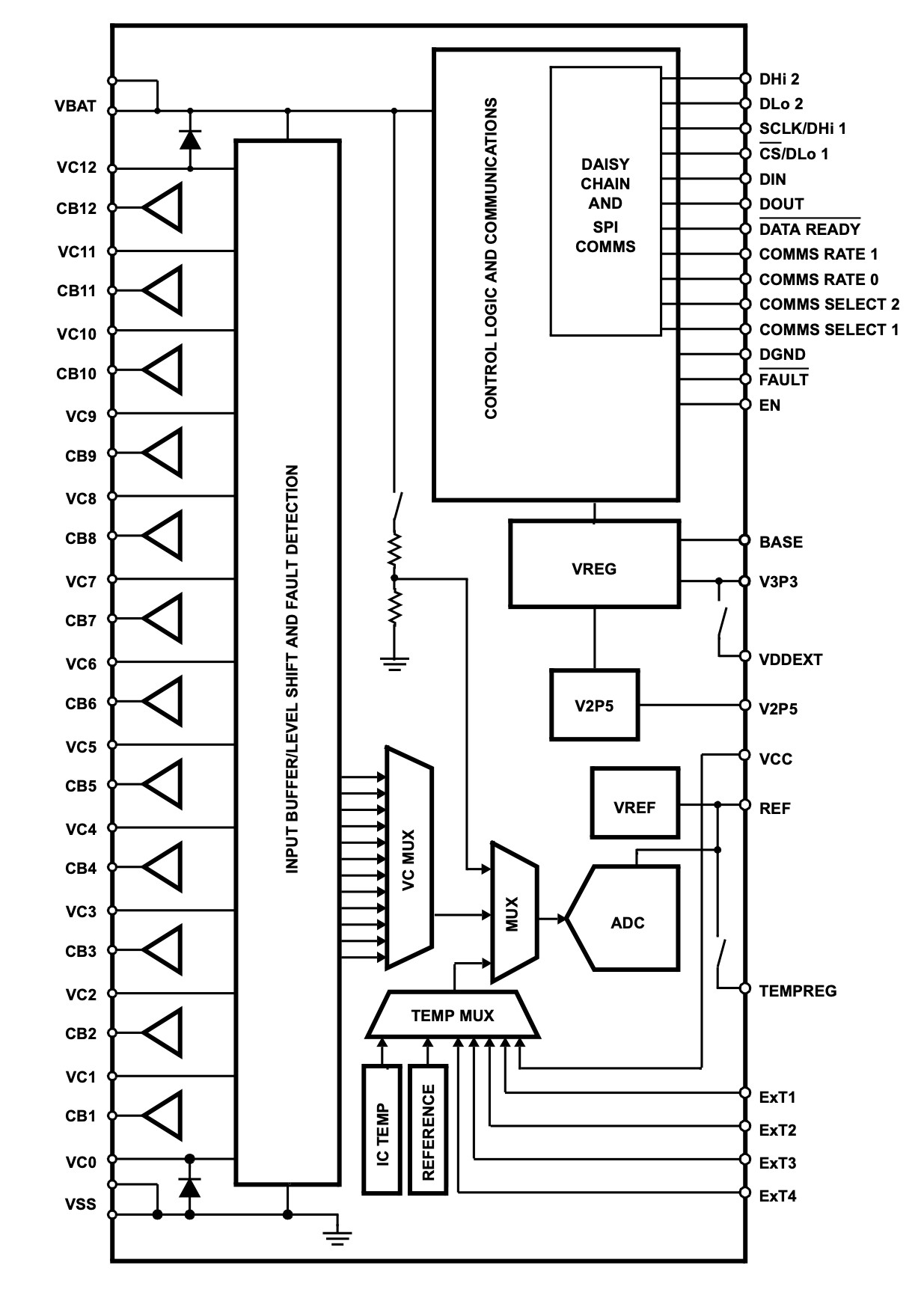
Auf der linken Seite sieht man neben den Anschlüssen für Masse (unten) und positiver Betriebs- bzw. Akkuspannung (oben) die vielen Anschlüsse für insgesamt zwölf Lithium-Zellen. Die Spannungen gelangen vom „Input Buffer / Level Shifter“ über einen Umschalter (VC MUX) und einen weiteren Selektor (MUX) auf einen A/D-Konverter. Daneben gibt es Referenzspannungen, Einheiten zur Messung von Temperatur usw., Überwachung der ELSS und natürlich das Wichtigste: der voll digitale Block „Control Logic and Communications”).
Bild 10 zeigt die prinzipielle Anwendungsschaltung.
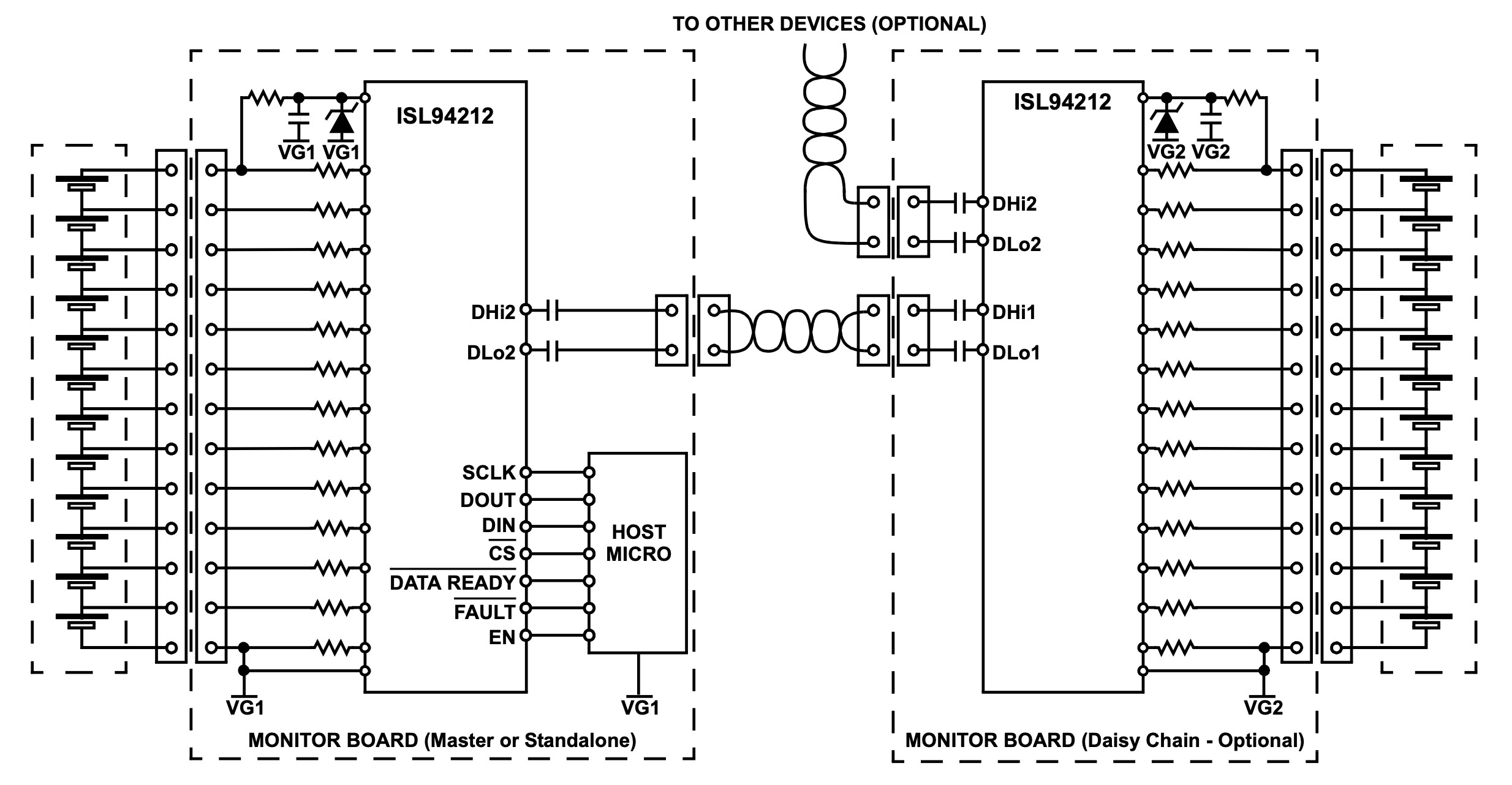
Hier sieht man die IC-Beschaltung genauer. Links sind die Zellen angeschlossen und rechts vom linken IC ISL94212 steuert ein Mikrocontroller das ganze BMS via digitaler Schnittstelle. Will man mehr als 12 Zellen überwachen, werden weitere Module mit je einem ISL94212 erforderlich. Die einzelnen Module werden seriell gekoppelt: Daher gibt es die beiden Pins DHi und DLo zweimal pro IC (mit dem Index 1 und 2). Aufgrund der hohen Spannungen solcher Modulketten werden die seriellen Schnittstellen nicht direkt, sondern über Kondensatoren mit kleinen Kapazitäten gekoppelt.
Das IC bietet natürlich nicht nur eine Überwachung vieler Zellen, sondern auch das notwendige Balancing. Bild 11 enthält die prinzipielle Anschaltung von je einem Lastwiderstand (ganz links) über einen kleinen Power-MOSFET, der über den zugehörigen IC-Ausgang CBX gesteuert wird.
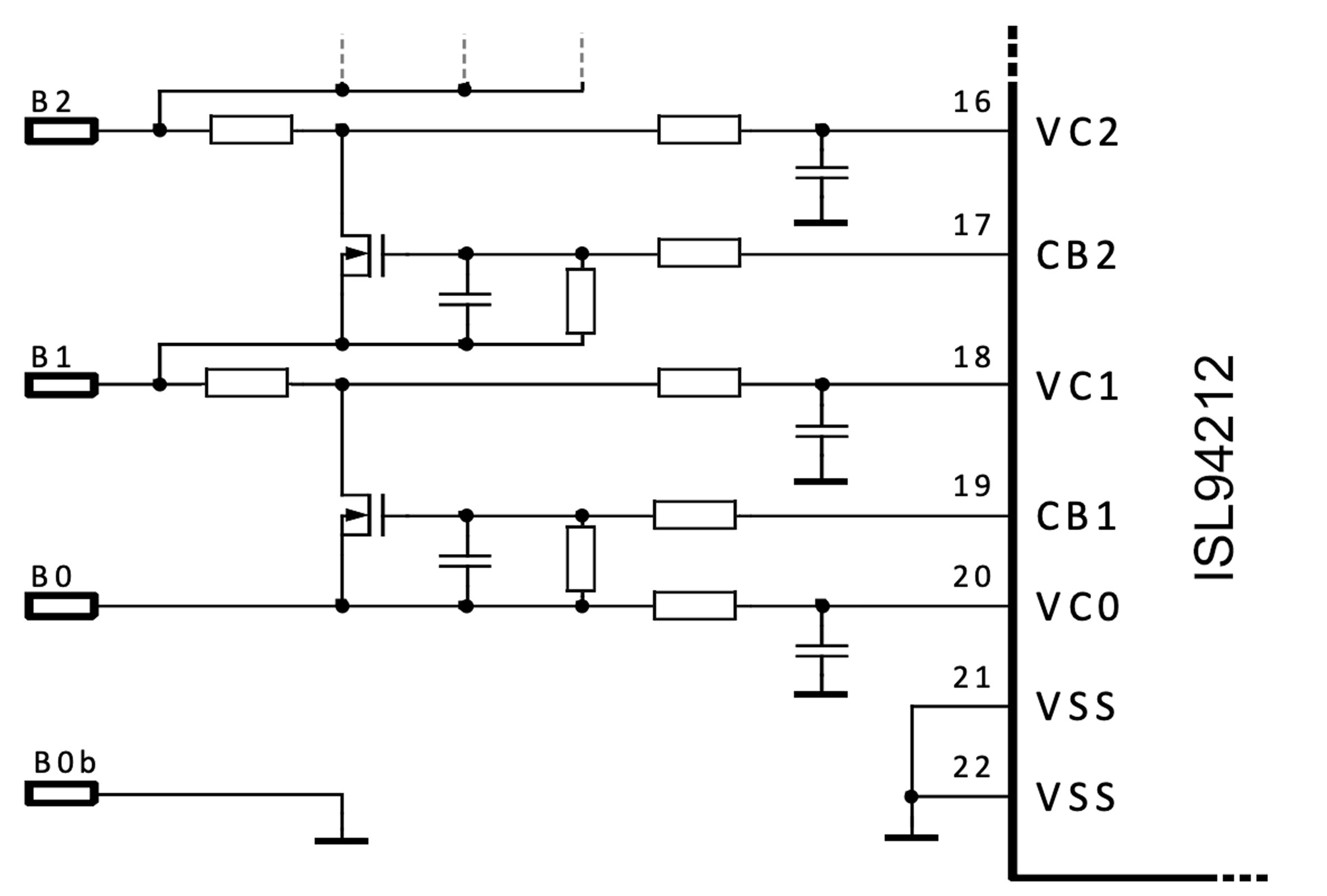
Auf diese Weise lässt sich das Balancing auch für recht hohe Ströme realisieren. Die Details der vielen IC-Funktionen entnehme man dem Datenblatt.
Praxis
Wenn Sie es mit einem Lithium-Akku zu tun haben, dann haben Sie im Prinzip die Wahl zwischen drei Strategien: Für einfache Anwendungen kaufen Sie schlicht so eine kleine, preiswerte und fertig bestückte Platine aus chinesischer Produktion wie die von Bild 5. Bei einem größeren und/oder teureren Akku können Sie auch von Markenherstellern aus einem unüberschaubar großen Fundus an fertigen BMS-Lösungen auswählen. Last not least bietet es sich an, für das in Frage kommende Akkupaket eine Lösung maßzuschneidern. Auswahl an ICs gibt es genug. In einigen Fällen kann und muss man dafür dann aber auch eigenen Code für die Überwachung und Steuerung des Akkus schreiben, wenn man es wirklich genau machen will. In all diesen Fällen ist Google ein guter Freund.
----------------------------------------------------------------------------------------------------------------------
Wollen Sie weitere Elektor-Artikel lesen? Jetzt Elektor-Mitglied werden und nichts verpassen!
----------------------------------------------------------------------------------------------------------------------
Diskussion (11 Kommentare)