Ein kleiner Schritt für eine Ameise
06. Mai 2015
über
über
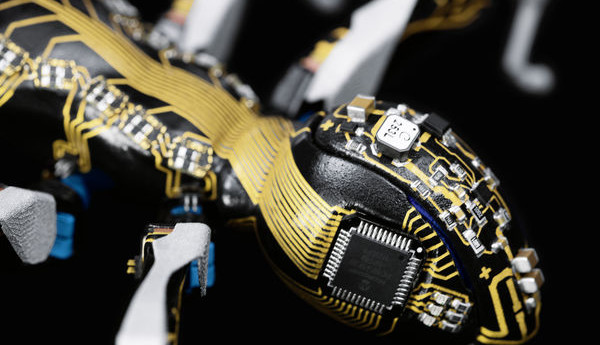
Die Festo AG & Co. KG aus Esslingen hat schon in den vergangenen Jahren mit technischen Konstruktionen überzeugt, die sich an Vorbildern aus der Natur orientierten. Auf der diesjährigen Hannover Messe ist die Wahl auf kollaborative Ameisen gefallen - BionicANTs arbeiten gemeinsam an Aufgaben, die ein einzelnes Exemplar nicht bewältigen könnte. Den kompakten Aufbau und ihr prägnantes Äußeres verdanken die BionicANTs einer LPKF-Technologie: Durch das LDS-Verfahren tragen sie elektronische Bauteile und die zugehörigen Leiterzüge auf dem Körper.
Die Körper und Beine der BionicANTs von Festo wurden im 3D-Druck hergestellt. Durch den LPKF ProtoPaint LDS-Lack lassen sich elektronische Komponenten und Leiterbahnen direkt auf der Außenhaut unterbringen (© Festo AG & Co. KG).Wenn es klein und kompakt werden soll, bieten sich MIDs (Mechatronic Integrated Devices) an: Sie vereinen mechanische und elektronische Funktionen. In der MID-Technologie dominiert die Laser-Direktstrukturierung (LDS): Ein Laserstrahl schreibt die gewünschten Strukturen auf einen Kunststoffkörper, der im Spritzguss aus einem additivierten Kunststoff hergestellt wird. In einem stromlosen Metallisierungsbad bauen sich anschließend Leiterbahnen auf, so entstehen 3DSchaltungsträger.
Dreidimensionale Schaltungsträger verringern den Platzbedarf und das Gewicht einer Baugruppe. Sie dienen als Bauteilträger, Antennen und als Verbindungselement. Dank Lasertechnologie lassen sich Änderungen am Leitungslayout ohne weitere Werkzeuge nur durch Anpassung der Strukturierungslayouts vornehmen. LDS-Schaltungsträger sind bislang in großem Umfang als Antennen in Smartphones und Tablet-Computern zu finden, aber auch in der Automobilindustrie, der Medizintechnik und der Consumer-Elektronik.
Festo setzte bei den BionicANTs ein besonderes Verfahren ein. Körper und Beine wurden im 3D-Druck erstellt und mit LPKF ProtoPaint LDS Lack beschichtet. Dieser enthält die LDS-Additive - danach kann das Bauteil wie ein LDS-Kunststoff weiterverarbeitet werden. Prozessentwicklung und Produktion lagen bei der LaserMicronics GmbH, die sich als Technologiescout und Fertigungsdienstleister auf das LDS-Verfahren spezialisiert hat.
Auf dem nur 13,5 cm langen Produkt konnten dank der 3D-MIDTechnologie alle mechanischen und elektronischen Funktionen untergebracht werden. Der bionische Technologieträger zeigt, wie autonome Einzelkomponenten als vernetztes Gesamtsystem verschiedene Regeln einhalten können und gemeinsam eine komplexe Aufgabe lösen - hier spielen High-Tech bei der Konstruktion und bei der Herstellung Hand in Hand.
Die Körper und Beine der BionicANTs von Festo wurden im 3D-Druck hergestellt. Durch den LPKF ProtoPaint LDS-Lack lassen sich elektronische Komponenten und Leiterbahnen direkt auf der Außenhaut unterbringen (© Festo AG & Co. KG).Wenn es klein und kompakt werden soll, bieten sich MIDs (Mechatronic Integrated Devices) an: Sie vereinen mechanische und elektronische Funktionen. In der MID-Technologie dominiert die Laser-Direktstrukturierung (LDS): Ein Laserstrahl schreibt die gewünschten Strukturen auf einen Kunststoffkörper, der im Spritzguss aus einem additivierten Kunststoff hergestellt wird. In einem stromlosen Metallisierungsbad bauen sich anschließend Leiterbahnen auf, so entstehen 3DSchaltungsträger.
Dreidimensionale Schaltungsträger verringern den Platzbedarf und das Gewicht einer Baugruppe. Sie dienen als Bauteilträger, Antennen und als Verbindungselement. Dank Lasertechnologie lassen sich Änderungen am Leitungslayout ohne weitere Werkzeuge nur durch Anpassung der Strukturierungslayouts vornehmen. LDS-Schaltungsträger sind bislang in großem Umfang als Antennen in Smartphones und Tablet-Computern zu finden, aber auch in der Automobilindustrie, der Medizintechnik und der Consumer-Elektronik.
Festo setzte bei den BionicANTs ein besonderes Verfahren ein. Körper und Beine wurden im 3D-Druck erstellt und mit LPKF ProtoPaint LDS Lack beschichtet. Dieser enthält die LDS-Additive - danach kann das Bauteil wie ein LDS-Kunststoff weiterverarbeitet werden. Prozessentwicklung und Produktion lagen bei der LaserMicronics GmbH, die sich als Technologiescout und Fertigungsdienstleister auf das LDS-Verfahren spezialisiert hat.
Auf dem nur 13,5 cm langen Produkt konnten dank der 3D-MIDTechnologie alle mechanischen und elektronischen Funktionen untergebracht werden. Der bionische Technologieträger zeigt, wie autonome Einzelkomponenten als vernetztes Gesamtsystem verschiedene Regeln einhalten können und gemeinsam eine komplexe Aufgabe lösen - hier spielen High-Tech bei der Konstruktion und bei der Herstellung Hand in Hand.
Mehr anzeigen
Weniger anzeigen
Diskussion (0 Kommentare)