PCB mit CNC (Teil 2): Gravieren und Bohren der Pads und Vias
über
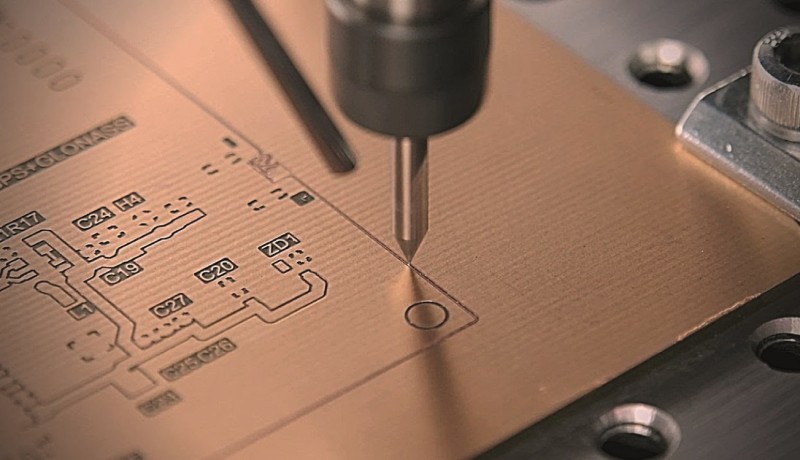
Im ersten Teil der Serie ging es um die Erstellung von CAM-Dateien für Leiterplatten (PCBs) mit einer CNC-Fräsmaschine (Computer Numerical Control). In diesem zweiten Teil werden wir sehen, wie wir die Platte unserer CNC2018 modifizieren und dann die Dateien verwenden, um unsere Platine vorzubereiten. Wir beginnen mit der Gravur und dem Bohren der Pads und Vias.
Modifikation der CNC2018-Platte
- Aluminiumplatte mit gleichmäßigen Nuten für M5-Muttern (Abbildung 1), um eine Fläche von maximal 24 × 18 cm abzudecken. Für unseren Bedarf ist eine Fläche von 20 × 16 cm mehr als ausreichend, die wir mit zwei nebeneinander liegenden 20 × 8 cm großen Platten erhalten haben. Sie können sie einzeln oder in Form einer einzigen 40 × 8 cm großen Platte kaufen, die Sie dann in zwei gleiche Teile schneiden müssen. Im letzteren Fall sind die Kosten geringer, aber Sie benötigen die entsprechende Schneideausrüstung.
- 4 × M5-Muttern pro Profil (8 weitere werden für die Stützen benötigt) mit den entsprechenden Schrauben und Unterlegscheiben.
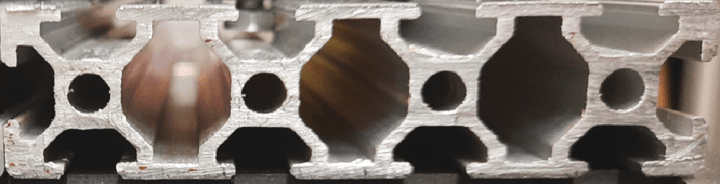
Die folgenden einfachen Arbeitsschritte sind zu befolgen:
- Legen Sie die beiden Platten paarweise und mittig auf die Oberseite der Originalplatte und befestigen Sie sie vorübergehend mit sehr starkem Klebeband. Es ist wichtig, dass die beiden Platten perfekt ausgerichtet sind und einander berühren. Die offenen Kanten sollten entlang der X-Achse der Platte ausgerichtet sein, sodass die geschlossene Kante nach vorne zeigt.
- Drehen Sie die CNC auf den Kopf und schrauben Sie die 4 Muttern so in die Nuten, dass sie durch die Schlitze in der PVC-Platte sichtbar und symmetrisch sind.
- Markieren Sie die Punkte mit einem Marker, sowohl auf den Platten als auch auf der Unterseite der PVC-Platte.
- Entfernen Sie die Platten und fixieren Sie die Muttern mit Heißkleber (Abbildung 2).
- Fixieren Sie die Platten mit 4 Schrauben und Unterlegscheiben (Abbildung 3).
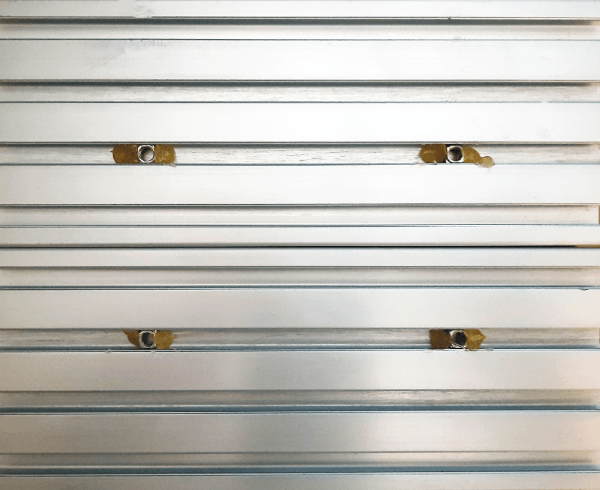
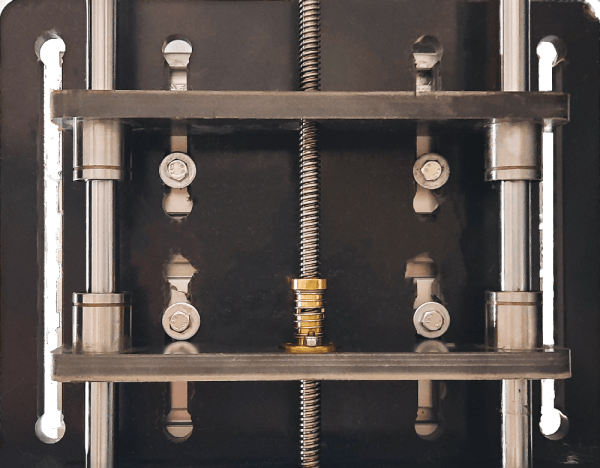
Haben Sie unsere Anweisungen befolgt, sieht das Ergebnis wie in Abbildung 4 aus. Die Änderung führt zu einem Höhenverlust von etwa 2 cm, aber der Z-Achsenweg dieser CNC ist für die Platinenbearbeitung ausreichend.
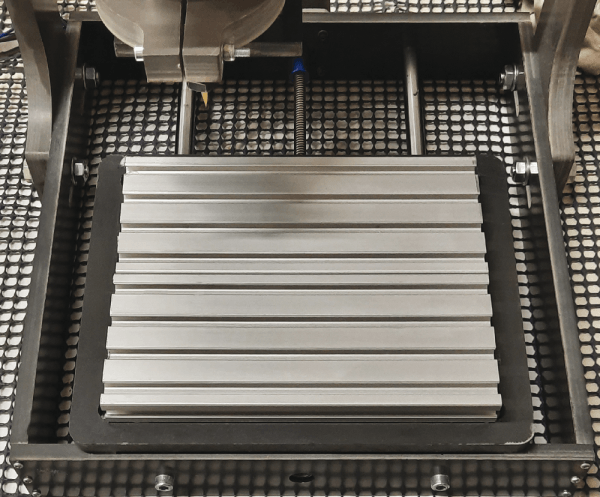
Um die Arbeit zu vervollständigen und das Beste aus unserer neuen Platte zu machen, benötigen wir nun Halterungen für Platinen, die wir per 3D-Druck hergestellt haben. Sie finden die STL-Dateien hier. Die Halterungen sind so konzipiert, dass sie die Nuten des Aluminiumprofils optimal ausnutzen, sich an praktisch jede Platinengröße anpassen und den Abstand zum Bett vergrößern, um das Bohren zu erleichtern. Das "L"-System mit Schrauben und Muttern (eingebettet in die Halterung) ermöglicht eine perfekte Fixierung der Platine, was für die Gravur wichtig ist (Abbildung 5). Die Halterungen wurden für M6-Schrauben/Bolzen konzipiert, lassen sich aber auch mit M5-Schrauben verwenden.
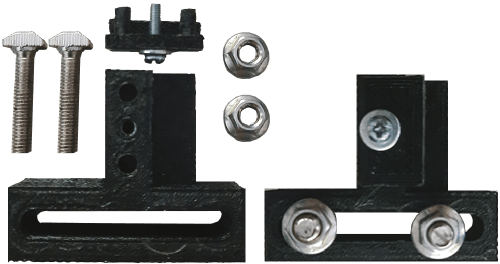
Wir müssen zwei normale und zwei gespiegelte Halterungen sowie die vier "L"-Bauteile für die Befestigung der Leiterplatte drucken. Wie auf dem Foto deutlich zu sehen ist, benötigt jede der 4 Halterungen zwei M5-Profilschrauben mit einer Länge von etwa 25 mm, zwei Muttern mit integrierter Unterlegscheibe (ein separates Paar ist auch in Ordnung) und eine kleine M3-Schraube mit Unterlegscheibe sowie Mutter (die in die spezielle Nut der Halterung eingesetzt werden muss). In Abbildung 6 zeigen wir das Endergebnis, bei dem die Leiterplatte für die nächsten Schritte bereit ist. Mit dieser Art von Halterung kann die Mindestgröße einer verkupferten Leiterplatte 5 × 3,5 cm betragen.
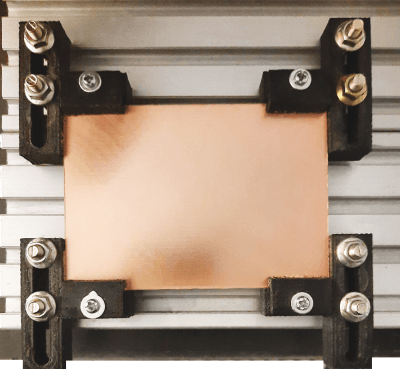
Das Kupfer-beschichtete Board für die Leiterplatine
Je nach den Abmessungen der Leiterplatine, die sich aus dem Entwurf ergeben, sollten Sie eine einseitig verkupferte Platine vorbereiten. In unserem Fall muss sie etwas größer sein als das Design, etwa 1 cm auf jeder Seite, um zu vermeiden, dass der Fräser gegen die Halterungen stößt und beschädigt wird. Die Platine sollte mit der zu gravierenden Seite nach oben an den Halterungen befestigt werden. Bitte beachten Sie: Manchmal haben verkupferte Leiterplatinen aufgrund des werkseitigen Schneidens verdickte Kanten, wenn sie qualitativ minderwertig sind. Das kann beim Gravieren zu Problemen führen, da es eine feste Verbindung mit den Trägern verhindert. Daher müssen Sie alle Kanten feilen, bis diese unerwünschten Teile auf beiden Seiten entfernt sind.
Wir erinnern Sie an die beiden kostenlosen Programme, die Sie herunterladen können: FlatCAM und Candle . Es ist jedoch immer ratsam, die neuesten Versionen zu verwenden (allerdings nicht die Beta-Versionen). Die Verwendung von FlatCAM und die Erstellung der zugehörigen Dateien haben wir bereits in der vorherigen Ausgabe beschrieben. Jetzt werden wir uns stattdessen mit Candle beschäftigen.
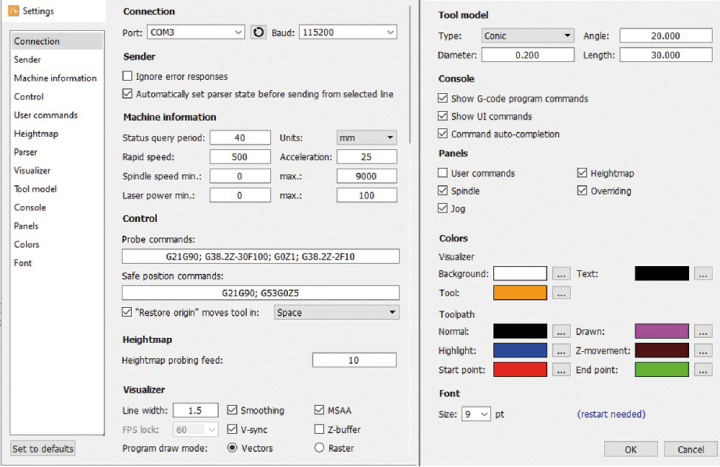
Es ist keine Installationen notwendig. Der entpackte Ordner kann an einem beliebigen Ort abgelegt werden. Öffnen Sie ihn einfach und führen Sie die Datei Candle.exe aus. Zunächst müssen Sie das Programm richtig einrichten. Ist der Controller an den USB-Anschluss des PCs angeschlossen, wählen Sie im Menü Service-Einstellungen den entsprechenden COM-Anschluss aus und konfigurieren im Anschluss die gewünschten Felder, wie in Abbildung 7 gezeigt. Bestätigen Sie abschließend alles mit OK.
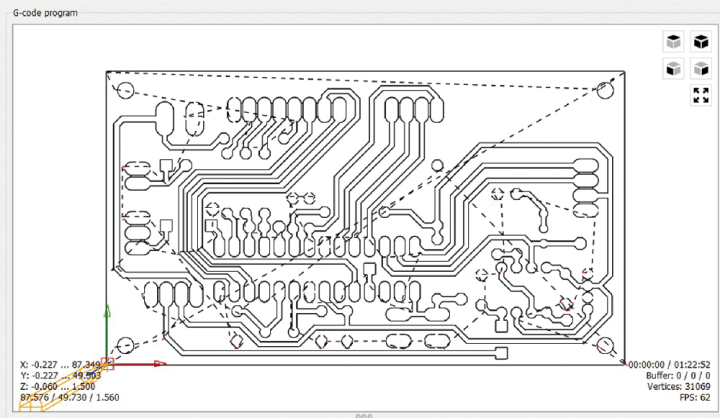
Ist der ausgewählte Port der richtige, wird im rechten Teil der Maske im Feld Status der Wert Idle angezeigt. Lesen Sie stattdessen Opened, müssen Sie zurück zu den Einstellungen und den Port ändern, indem Sie ihn unter den verfügbaren auswählen. Öffnen Sie die CAM-Datei Name_PCB.nc ("Name" ist der Name, den Sie der Datei gegeben haben, die Sie mit FlatCAM erstellt haben). Im mittleren Bereich der Maske sehen Sie die Leiterbahnen und Pads auf der Leiterplatte sowie einige gepunktete Linien, die den Weg darstellen, den der Gravierstichel während der Gravur nehmen wird (Abbildung 8). Werfen wir einen Blick auf die Felder und Schaltflächen, die sich auf der rechten Seite der Maske befinden und die wir in Abbildung 9 nummeriert haben.
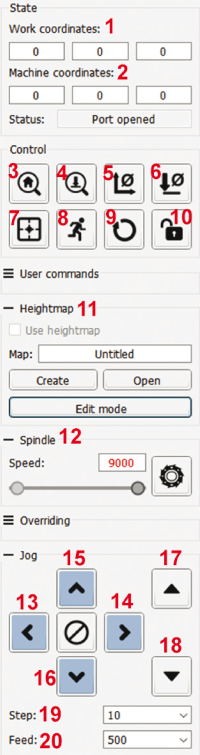
2. Machine Coordinates: die drei X-Y-Z Felder enthalten die absoluten Koordinaten der Maschine. Beginnt ein Auftrag mit den Ursprüngen bei 0,0,0, stimmen die drei Felder mit den Arbeitskoordinaten überein.
3. Home: startet die Prozedur der Referenzfahrt mit dem Befehl $H. Er sollte nur verwendet werden und funktioniert nur dann korrekt, wenn die CNC mit Endschaltern ausgestattet ist.
4. Z-probe: wird verwendet, um den Z-Nullpunkt zu finden, d.h. den Kontaktpunkt zwischen der Spitze des Fräsers und der Oberfläche der Kupferschicht. Es sollte mit korrekt angeschlossener Sonde verwendet werden, da die Sondenspitze sonst irreparabel abbricht.
5. Zero XY: wird verwendet, um die Arbeitskoordinaten X und Y in dem Moment zu nullen, in dem der Fräser auf den Ausgangspunkt der Bearbeitung gesetzt wird.
6. Zero Z: dient dazu, die Z-Arbeitskoordinate zurückzusetzen, wenn der Messtaster die Oberfläche der Kupfer-beschichteten Leiterplatine am Ursprungspunkt der Arbeit berührt.
7. Restore Origin: stellt die Arbeitskoordinaten mit den Maschinenkoordinaten wieder her, indem Sie den Befehl G92 verwenden.
Wenn Sie in den Candle-Einstellungen das Feld Ursprung wiederherstellen aktivieren (empfohlene Option!), indem Sie auf die Schaltfläche klicken, wird die CNC gestartet und der eingestellte Wert wird übernommen:
Plane: bewegt sich die Maschine zum XY-Nullpunkt und bewegt sich nur horizontal.
Space: bewegt sich die Spindel zum XYZ-Nullpunkt und bewegt sich dabei horizontal und vertikal.
8. Safe position: bringt die Maschine in eine sichere Position entlang der Z-Achse, die das Werkzeug von der Kupferplatte fernhält. Die Position wird durch den Wert bestimmt, der im Feld Safe Position Commands eingestellt ist. In unserem Fall bedeutet der Endwert Z5, dass die Spindel 5 mm von der Leiterplatine entfernt ist. Dieser Punkt wird unabhängig von der Ausgangsposition der Spindel erreicht. Sie wird also angehoben oder abgesenkt, um genau 5 mm von der Oberfläche der Kupferplatte entfernt zu stoppen.
9. Reset: setzt die CNC mit dem Befehl Strg+X zurück.
10. Unlock: hebt mit dem Befehl $X die Sperre der CNC aus dem Alarmzustand auf.
11. Heightmap: Abschnitt für die Kartierung der Kupferoberfläche reserviert.
12. Spindle: Abschnitt zur Steuerung des Spindel-Motors. Er zeigt den eingestellten Wert mit dem Schieberegler unten an, wobei der Bereich von 0 bis zum in den Einstellungen eingegebenen Maximalwert reicht. Der Maximalwert sollte mit dem in FlatCAM eingegebenen Wert übereinstimmen. Die Schaltfläche neben dem Schieberegler dient zum Starten und Stoppen des Spindel-Motors.
13. X-: bewegt die Spindel nach links.
14. X+: bewegt die Spindel nach rechts.
15. Y+: bewegt die Platte an die Vorderseite der CNC.
16. Y-: bewegt die Platte an die Rückseite der CNC.
17. Z+: bewegt die Spindel nach oben.
18. Z-: bewegt die Spindel nach unten.
19. Step: Achsenverschiebung in mm.
20. Feed: Geschwindigkeit der Achsenverschiebung in mm/min.
Der XY-Nullpunkt ist der Punkt, an dem Sie mit der Gravur des PCB-Designs beginnen möchten. Um den Nullpunkt zu wählen, müssen Sie die Leiterplatine virtuell auf der verkupferten Oberfläche positionieren. Hier ein Beispiel: Ist diese Fläche 10 × 7 cm groß und das PCB-Design 8 × 5 cm groß, ist es eine gute Idee, die Leiterplatine zu zentrieren und dabei etwa 1 cm Abstand von jeder Kante der Platte zu lassen. Zu Ihrer Unterstützung können Sie ein Stück Papier mit den genauen Abmessungen der Leiterplatine ausschneiden und es vorübergehend auf die Platte legen, wobei Sie es so gut wie möglich zentrieren. Dann können Sie einen Punkt in der Nähe der Ecke markieren, der der Nullpunkt des Arbeitsbereichs sein wird. Achten Sie jedoch darauf, nicht genau auf der Ecke zu markieren, da die Tinte den elektrischen Kontakt zwischen dem Werkzeug und dem Kupfer der Leiterplatte behindern könnte, wodurch die Funktion des Z-Tasters behindert würde (Abbildung 10).
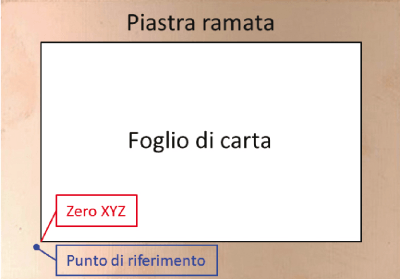
Mit den X/Y-Schaltflächen müssen Sie die Spindel mehr oder weniger an der Markierung positionieren, die Sie mit dem Marker gemacht haben. Dann müssen Sie auf die Schaltfläche Null XY klicken, um einen temporären XY-Nullpunkt zu setzen. Das muss an dieser Stelle nicht extrem präzise sein.
Die "Probe Z"-Sonde
Bevor wir den Fräser einsetzen, machen wir einen Test mit der Probe-Z-Sonde, die sich recht einfach einrichten lässt. Sie benötigen ein bipolares Standardkabel. Schließen Sie an einem Ende einen 2-poligen Stecker an und befestigen Sie am anderen Ende zwei Krokodilklemmen (Abbildung 11). Der Pfostenstecker muss in das entsprechende Stiftpaar am Anschluss des externen Controllers eingesteckt werden. Im Falle Ihres CNC-Controllers ist der Stift mit PB beschriftet. In anderen Fällen finden Sie ihn vielleicht als A5 markiert. Der erste Test sollte ohne Fräser durchgeführt werden, da dieser im Falle einer Fehlfunktion beim Kontakt mit der verkupferten Platine abbrechen könnte.
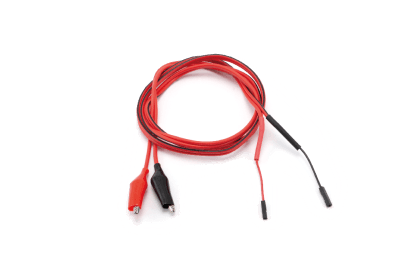
Sie müssen die Spindel mit der Schaltfläche Z+ auf den höchstmöglichen Punkt bringen. Stellen Sie dann einen Wert von Step = 20 ein (geben Sie diesen Wert manuell ein) und klicken Sie dann auf die Taste Z-. Sobald die Spindel beginnt, sich nach unten zu bewegen, schließen Sie die beiden Krokodilklemmen der Sonde kurz. Schließt die Spindel ihre 20-mm-Bewegung ab, ohne auf den Kurzschluss zwischen den beiden Klemmen zu reagieren, bedeutet das, dass etwas nicht stimmt und Sie das Problem beheben müssen.
Bewegt sich die Spindel hingegen schnell nach unten und hält an einem bestimmten Punkt von selbst an, deutet das darauf hin, dass der Controller den Kontakt zwischen den beiden Clips erkennt. Dieses Verhalten könnte auf eine Fehlfunktion der Sonde hindeuten, aber das wird bei dem eigentlichen Test nach unseren Anweisungen nicht der Fall sein.
Ist alles in Ordnung, können Sie den 0,2 mm Fräser in das Spindelfutter einsetzen. Heben Sie das Werkzeug über die Oberfläche der Platte und starten Sie den Motor, indem Sie auf die entsprechende Taste klicken und die Spitze beobachten. Ist das Werkzeug nicht richtig eingesetzt und gesichert, haben Sie das Gefühl, eine doppelte Spitze zu sehen. Beheben Sie dieses Problem nicht, wird das Resultat der Gravur gelinde gesagt verwirrend sein!
Stellen Sie den Schritt auf 1, sodass Sie Bewegungen von nur einem Millimeter haben. Senken Sie die Spindel so ab, dass die Spitze des Fräsers etwa ein paar Millimeter von der Kupferplatte entfernt ist, und zwar genau auf dem Punkt, der als XY-Nullpunkt gewählt wurde, der nicht mit dem Markierungszeichen übereinstimmen muss. Jetzt müssen wir die Zange der Sonde richtig anschließen: eine sollte direkt am Fräser und die andere an der Kupferplatte eingehakt werden, und zwar an einem Punkt außerhalb des zu gravierenden Arbeitsbereichs (das übliche Stück Papier ist hier hilfreich). Das ist wichtig, denn sonst könnte der Fräser beim Abtasten gegen die Pinzette stoßen und sie beschädigen.
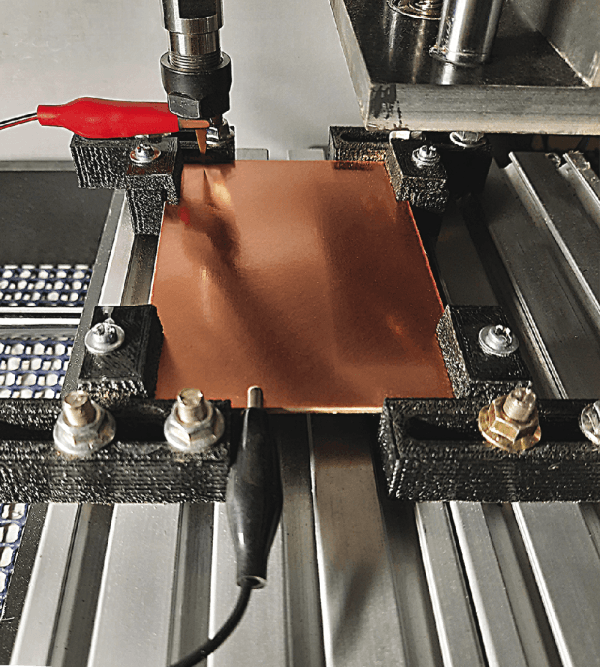
In Abbildung 12 haben wir ein Bild der CNC während der Z-Null-Suchphase aufgenommen, um zu zeigen, wie die beiden Clips verbunden werden sollten.
Die letzte Aktion ist das Einfügen (unter der Hauptmaske):
- Geben Sie im Probe-Zt-Feld den Wert 1.00 ein.
- Geben Sie im Probe-Zb-Feld den Wert -2.00.
An diesem Punkt können Sie mit dem Einstellen des Z-Nullpunkts beginnen. Dieser Vorgang ist von entscheidender Bedeutung. Eine standardmäßig beschichtete Platine hat normalerweise eine Kupferdicke von etwa 0,035 Millimetern (35 Mikron). Bei CAM haben wir eine Tiefe von 0,06 mm eingestellt. Beginnen Sie also nicht genau mit dem Kontakt zwischen Fräser und Oberfläche, erhalten Sie schnell schlechte Ergebnisse.
Klicken Sie auf die Schaltfläche Z-probe, wird der Bohrer langsam abgesenkt. Aufgrund seiner sehr langsamen Geschwindigkeit scheint er sich nicht zu bewegen, aber Sie können den Fortschritt bestätigen, indem Sie die Abnahme der Z-Koordinatenwerte im Feld Arbeitskoordinaten beobachten. In dem Moment, in dem die Spitze des Fräsers die verkupferte Oberfläche berührt, wird der Stichel um 1 mm angehoben und dann wieder abgesenkt, wobei er beim Kontakt mit der Leiterplatte stoppt.
Tritt während des Abstiegs ein Alarm auf, bedeutet das, dass die Spitze des Werkzeugs mehr als 2 mm von der Leiterplatte entfernt ist. Klicken Sie in diesem Fall auf die Schaltfläche Unlock, dann auf die Schaltfläche Zero Z und noch einmal auf die Schaltfläche Z-probe. Bleibt der Fräser ohne Fehler in Kontakt mit der Kupferplatte stehen, war der Vorgang erfolgreich, sodass Sie auf die Schaltfläche Zero-Z und dann auf Zero-XY klicken können. Haben Sie diese Anweisungen sorgfältig befolgt, sollte nun in den drei Feldern der Works-Koordinaten der Wert 0 erscheinen.
The next step is to match the Works coordinates with the absolute coordinates of the machine. This will come in handy later, especially in case you have to stop working. We need to perform the following operations in sequence:
- Close Candle.
- Turn off the power supply of the CNC controller, no need to disconnect the USB.
- After a few seconds, reopen Candle and then turn the power supply back on.
- Click on Restore origin.
- Click on Zero Z and Zero XY.
- Click on Restore origin again.
Now, hovering the mouse arrow over this button will bring up a small box showing the values 0, 0, 0. If this doesn’t happen, repeat the entire software sequence (not the Z zero sequence).
Mapping der Kupferschicht
Jetzt können Sie die CAM-Datei der Leiterplatte öffnen. Die Zeichnung wird im Hauptfenster von Candle angezeigt. Das Mapping ist ein entscheidender Schritt, um eine perfekte Gravur der Kupferschicht der Leiterplatte zu erreichen. Normalerweise können Verformungen der Leiterplatte dazu führen, dass die Oberfläche nicht perfekt eben ist. Daher kann es vorkommen, dass in Bereichen, die unter dem Z-Nullpunkt liegen, keine Gravur erfolgt, während in höheren Bereichen sehr tiefe Rillen entstehen können.
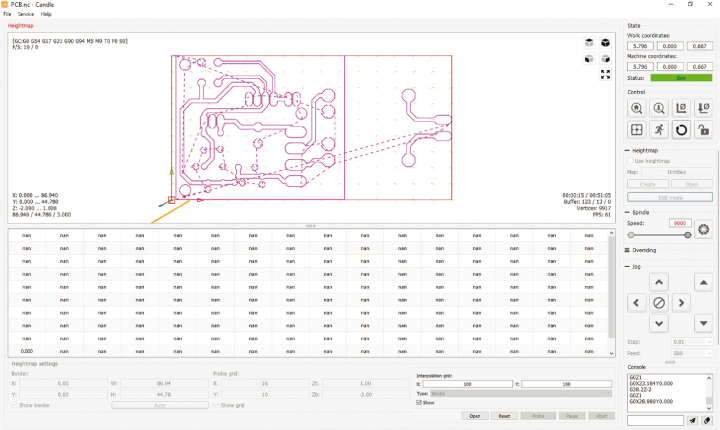
Indem Sie eine Karte der Kupfer-beschichteten Platine erstellen, gleicht die Software diese Unregelmäßigkeiten während des Graviervorgangs aus. Klicken Sie im Bereich Heightmap auf die Schaltfläche Create. Unterhalb des PCB-Bereichs öffnet sich der Mapping-Bereich (Abbildung 13):
- Aktivieren Sie die drei Kontrollkästchen mit der Bezeichnung Show…
- Klicken Sie auf Auto, sodass der rote Rahmen mit den Kanten der Leiterplatinenzeichnung übereinstimmt. Auf diese Weise werden die tatsächlichen Abmessungen darunter angezeigt.
- Geben Sie in das Feld Probe grid X einen ganzzahligen Wert ein, der ungefähr der doppelten Breite des PCB-Designs (in Zentimetern) entspricht. Ist die Leiterplatine z.B. 8 cm breit, können Sie einen Wert von 16 verwenden. Dieser Wert legt das Mapping für die X-Achse mit Messwerten etwa alle 0,5 cm fest.
- Geben Sie in das Feld Probe grid Y einen ganzzahligen Wert ein, der ungefähr der doppelten Tiefe des PCB-Designs (in Zentimetern) entspricht. Ist die Leiterplatte z.B. 5 cm tief, können Sie einen Wert von 10 verwenden. Dieser Wert legt die Zuordnung für die Y-Achse mit Messwerten etwa alle 0,5 cm fest.
- Prüfen Sie, ob das Feld Probe grid Zt auf 1.00 eingestellt ist.
- Prüfen Sie, ob das Feld Probe grid Zb auf -2.00 eingestellt ist.
- Geben Sie einen ganzzahligen Wert zwischen 50 und 200 in die Felder Interpolation grid X und Y ein. Dieser Wert legt die Interpolation zwischen benachbarten Kartierungspunkten fest. Wir haben 100 verwendet, aber 50 ist wahrscheinlich mehr als ausreichend.
Probe
Z-Probe
Restore origin
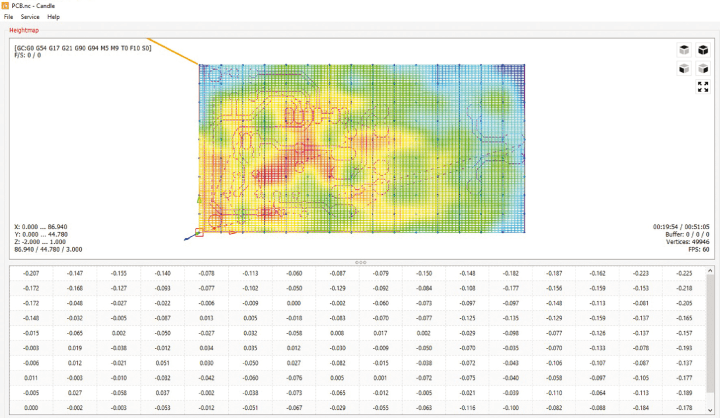
Natürlich müssen Sie diese Entsprechungen nicht überprüfen. Sie sollten auch die Auswirkungen der Interpolation berücksichtigen. Aber das geschieht alles automatisch. Klicken Sie auf Create, dann auf Yes bei der eventuellen Bestätigungsaufforderung und nennen Sie die Datei z.B. Name.map, wobei Sie denselben Pfad wie die CAM-Dateien wählen.
Klicken Sie auf Edit mode, um die Heightmap-Maske zu entfernen und die Leiterplatine wird wieder angezeigt. Aktivieren Sie das Feld Use Heightmap, klicken Sie auf Open und öffnen Sie die soeben erstellte .map-Datei. Die Software wird alle XYZ-Koordinaten auf der Grundlage der Karte neu berechnen.
Der letzte Vorgang, der durchgeführt werden muss, ist die Wiederholung des Z-Nullpunkts, wiederum mit Hilfe der Probe Z. Dieser Vorgang sollte nicht vernachlässigt werden, da es häufig vorkommt, dass der Z-Nullpunkt am Ende des Mappings leicht verändert ist, was sich negativ auf die Gravur auswirken würde. Unmittelbar danach sollten Sie Probe Z von der Steuerung trennen, die Zange aushängen und das Kabel beiseitelegen.
PCB-Ätzen
Bevor Sie mit diesem Vorgang beginnen, empfehlen wir Ihnen, ein emulgierbares Schmier- und Kühlöl für mechanische Werkzeuge bereitzuhalten. In der Regel wird es als 1%ige Mischung in normalem Leitungswasser zubereitet und kann zur einfachen Dosierung in einen Sprühbehälter gegeben werden. Sie müssen auf den Z-Null-Bereich einen ersten Sprühstoß geben.
An diesem Punkt heben Sie den Stichel am besten 5 bis 10 mm über die Platte und klicken auf die Schaltfläche SEND. Der Spindelmotor wird gestartet und der Fräser erreicht den Punkt, an dem die Gravur beginnen soll. Sie sollten die Gravur verfolgen, während Sie das Öl-Wasser-Gemisch auf das Kupfer auftragen, da dies die Leistung des Stichels verbessert, Überhitzung und Schäden verhindert sowie die Qualität der Kupfergravur verbessert. (Abbildung 15).
Allerdings muss man einen Sicherheitsabstand zum Stichel einhalten, denn ein Kontakt wäre extrem gefährlich!
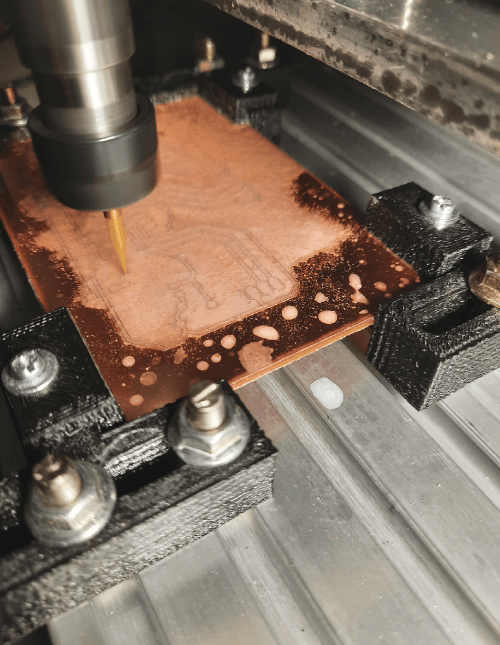
Candle stellt den Ätzvorgang grafisch dar. Der Stichel wird durch einen Zeiger dargestellt, der anzeigt, wo er sich befindet. Außerdem ändern die Leiterbahnen ihre Farbe, wenn sie geätzt werden. Es ist erwähnenswert, dass die CNC-Maschine bei größeren Leiterbahnen und Pads normalerweise einen doppelten Durchgang macht, wobei der zweite Durchgang etwas tiefer ist. Daher kann es sein, dass der erste Durchgang in einigen Bereichen nicht tief genug ist (Abbildung 16). Sollten Probleme auftreten, können Sie auf die Schaltfläche ABORT klicken, um den Vorgang sofort zu beenden.
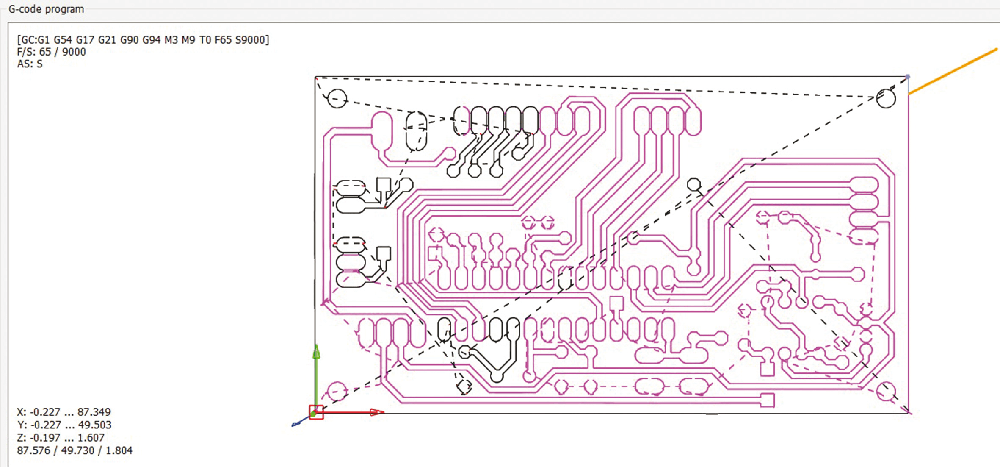
An diesem Punkt können Sie die notwendigen Korrekturen vornehmen und die Gravur mit der Schaltfläche Send von vorne beginnen. Sie dürfen Candle jedoch nicht schließen und wieder öffnen oder das Kabel abziehen, da Sie sonst die Null-XY-Referenzen verlieren könnten. Unter diesen Bedingungen können Sie die Gravur mit der Gewissheit fortsetzen, dass das Werkzeug genau den vorherigen Spuren folgt.
Beachten Sie bitte: Jedes Mal, wenn Sie Abort nutzen, müssen Sie vor dem erneuten Starten des Graviervorgangs die Heightmap-Datei neu laden und den Null-Z-Vorgang wiederholen.
Sobald der Graviervorgang abgeschlossen ist, dürfen Sie Candle nicht beenden oder die USB-Verbindung trennen, um die XY-Referenzen beizubehalten. Die Oberfläche der Platine wird voll von Kupferrückständen sein, die mit emulgierbarem Öl vermischt sind. Sie die Schaltflächen XYZ movement nutzen, um die Platine leicht zu reinigen, ohne sie von der Platte zu lösen. Das ist mit einer Bürste oder einem Tuch möglich. Sie brauchen sich nicht um die neuen Koordinaten zu kümmern, das Bohren beginnt automatisch bei Null XY.
Viele Faktoren tragen zur Qualität der Herstellung einer Leiterplatine bei. Manchmal ist das Ergebnis perfekt, aber häufiger kann die Oberfläche rau erscheinen, was auf eine zu große Gravurtiefe oder einen unzureichenden Zustand des Werkzeugs hinweisen kann. Außerdem muss man den restlichen "Teig" zwischen Öl und gefrästem Material beachten, sodass die Leiterplatine wie in Abbildung 17 aussehen kann.
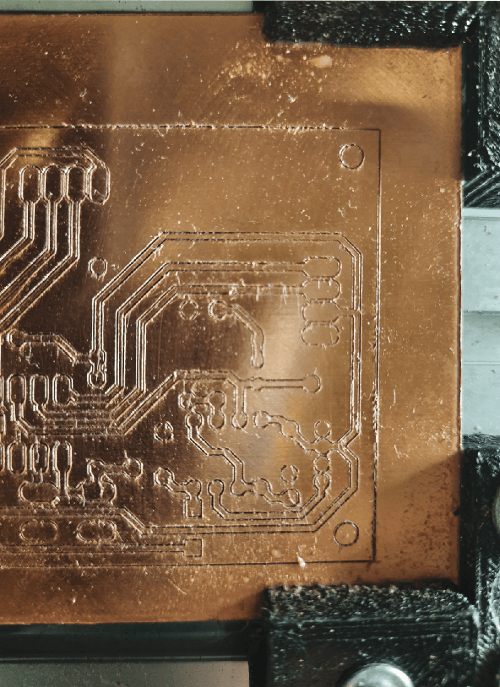
Bohren
Öffnen Sie die Datei Name_FORI.nc, ohne Candle zu schließen, um die Null-XY-Einstellungen zu behalten. Die Maske wird als eine Reihe von gestrichelten Linien angezeigt, die den Weg darstellen, den die CNC während des Bohrvorgangs nehmen wird (Abbildung 18).
Beachten Sie bitte: Es ist wichtig, dass Sie das Kästchen Autoscroll in der linken unteren Ecke aktivieren, da Sie sonst die Softwaremeldungen zum Wechseln der Bohrer nicht sehen.
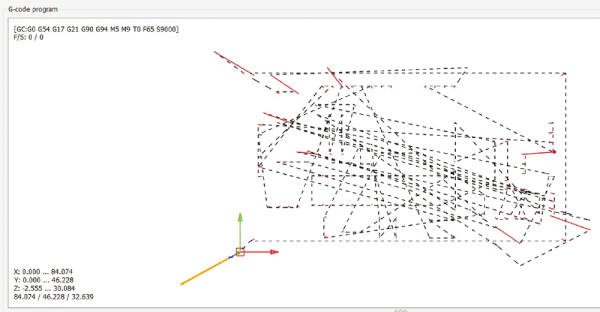
Sie sollten die Z-Achse neu nivellieren, da die Bohrer länger sind als die Gravurwerkzeuge. Allerdings können Sie Probe Z nicht verwenden, da der Bohrer möglicherweise keinen elektrischen Kontakt mit der Kupfer-beschichteten Oberfläche der Leiterplatine gewährleistet und brechen könnte.
Heben Sie die Spindel an und ersetzen Sie den Bohrer durch einen Bohrer. Achten Sie darauf, dass der Bohrer so weit eingeführt wird, dass er den farbigen Referenzring der Spindel berührt und ziehen Sie ihn fest an. CNC-spezifische Bohrer haben normalerweise einen farbigen Ring, der dafür sorgt, dass die Spindel immer gleich weit herausragt. Leider kann es vorkommen, dass sich dieser Ring (der fest ist) bei den verschiedenen Größen in einer anderen Position befindet, sodass ein Teil des Bohrwerkzeugs mehr oder weniger herausragt als andere.
Es kann daher vorkommen, dass wir nach der Z-Null-Kalibrierung mit einem Bohrer, wenn wir ihn durch einen anderen ersetzen, der mehr herausragt, die Leiterplatte bei den Bewegungen zwischen den Bohrungen beschädigen und sogar zerbrechen. Das Problem tritt nicht auf, wenn der Bohrer weniger vorsteht, weil der Wert der Tiefe (Cut Z), den wir in FlatCAM eingegeben haben, die Unterschiede deutlich ausgleichen kann. Daher ist es eine gute Idee, alle für die Leiterplatine vorgesehenen Bohrer zu nehmen und den längsten für die Kalibrierung des Z-Nullpunkts zu verwenden.
Der Teil, der Sie interessiert, ist natürlich der spiralförmige Teil unterhalb des Rings und nicht der Teil oberhalb. Wenn Sie hingegen Bohrer ohne Ring haben, dann bestimmen Sie am besten, wie weit sie aus der Spindel herausragen sollten und markieren Sie den Punkt auf allen Bohrern mit einem Permanentmarker.
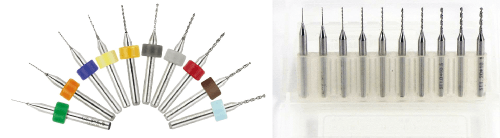
In Abbildung 19 sehen Sie die beiden Arten von Bohrer-Sets. Bewegen Sie sich außerhalb des Bereichs der Leiterplatine und starten Sie die Drehung des Spindelmotors mit der Taste Z. Senken Sie den Bohrer bis auf etwa 1 mm an die Leiterplatine, setzen Sie den Schrittwert auf "0,1" und fahren Sie dann fort, bis Sie einen Kontakt mit der Kupferschicht spüren. Klicken Sie nun auf die Schaltfläche Zero Z.
Heben Sie die Spitze ein paar Zentimeter an und klicken Sie dann auf Send. Das Programm hält sofort mit einer Fehlermeldung an und im Befehlsbereich erscheint eine hervorgehobene Zeile mit der erforderlichen Bitgröße für den ersten Satz von Bohrungen (Abbildung 20).
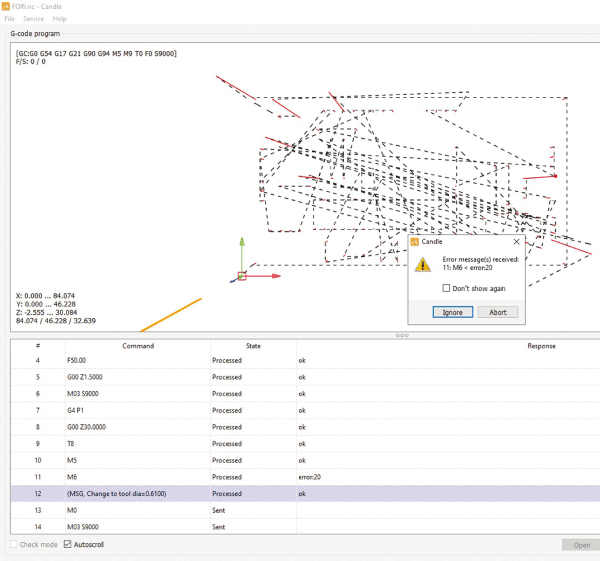
Haben Sie mit diesem speziellen Bohrer kalibriert, brauchen Sie ihn nicht zu ersetzen. Entspricht der angeforderte Wert jedoch keiner Standardgröße, sollten Sie die nächstmögliche Größe verwenden. In dem Beispiel aus Abbildung 20 wird ein 0,61 mm Bohrer benötigt. Sie können auch den 0,6 mm Bohrer verwenden. Ist die Änderung abgeschlossen, klicken Sie auf die Schaltfläche Pause und beginnen mit dem Bohren. Die CNC treibt die drei Motoren an, bringt den Bohrer in die XYZ-Nullposition und fährt mit dem ersten Loch fort, wobei sie dem durch die gestrichelten Linien angezeigten Pfad folgt. Ähnlich wie beim Gravieren ändern die gestrichelten Linien ihre Farbe, wenn das Bohren fortschreitet (Abbildung 21).
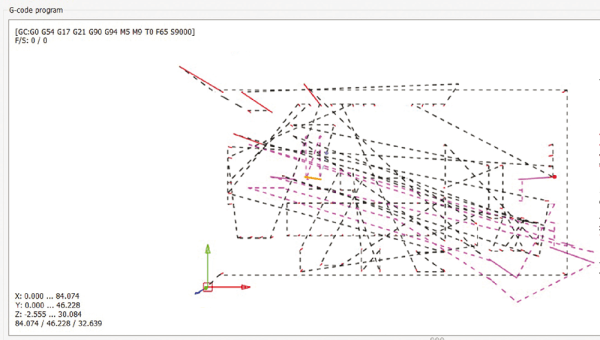
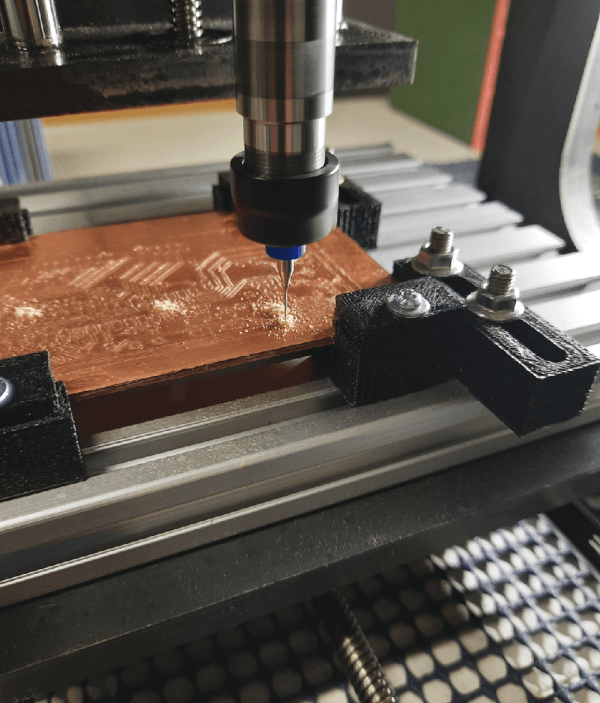
Sie sollten sich keine Gedanken über die Reinigung der Leiterplatine beim Bohren machen. Wir empfehlen Ihnen sogar, jede Art von Tätigkeit zu vermeiden, da es sehr gefährlich ist, mit den Händen oder einem Werkzeug in die Nähe eines Bohrers zu kommen, der, egal wie klein er ist, schwere Schäden anrichten kann! Tritt ein Problem auf (z.B. wenn Sie einen Bohrer abbrechen), können Sie jederzeit auf die Schaltfläche ABORT klicken, um den Vorgang sofort abzubrechen.
Jetzt können Sie das Problem beheben und die Bohrung mit der Schaltfläche Send erneut starten. Sie dürfen Candle jedoch nicht schließen und wieder öffnen oder das Kabel abziehen, da Sie sonst die XY-Nullreferenzen verlieren könnten. Nur unter diesen Bedingungen können Sie erneut mit dem Bohren beginnen und darauf vertrauen, dass die Bohrer genau über die vorherigen Löcher geführt werden.
Beachten Sie bitte: Müssen Sie die Bohrung von Anfang an wiederholen, können Sie es vermeiden, die Werkzeuge einzusetzen, die ihren Zyklus bereits abgeschlossen haben. Die CNC wird die Bewegungen auch ohne das Schneidewerkzeug ausführen. Erreichen Sie die Anforderung für den abgebrochenen Bohrer erreichen, können Sie ihn einsetzen.
Ende
Sind die Bohrarbeiten beendet, heben Sie die Spindel an, entfernen den Bohrer und nehmen die Leiterplatine von der Platte. Reinigen Sie die Leiterplatine zunächst mit einer Bürste mit harten Borsten, dann können Sie sie unter fließendes Wasser halten. Trocknen Sie sie anschließend, am besten mit einem Luftstrahl. Wenn, wie in unserem Fall, die Oberfläche nicht vollkommen glatt ist, muss sie mit sehr feinem Schleifpapier behandelt werden. Auch das geschieht unter fließendem Wasser, bis alle Unebenheiten verschwunden sind.
In Abbildung 23 sehen Sie die Qualität des fertigen Produkts auf beiden Seiten, die im Vergleich zur Arbeit bei einem Dienstleister wirklich nicht viel schlechter sind, abgesehen natürlich von der fehlenden Metallisierung und Lötmaske. Aber schließlich handelt es sich ja immer noch um einen Prototyp!
A final note concerns the offline controller we discussed in the article on the CNC controller. Keep in mind that it is fine for the engraving procedure, but not for the drilling procedure. This is because, excluding PC control, it wouldn’t allow for changing drill bits, and the tool change message would result in an error.

Editorische Anmerkungen: Interessieren Sie sich für CNC und Leiterplatten (PCBs)? Dieses Projekt (PCB per CNC) erschien ursprünglich in Elettronica IN.
Diskussion (1 Kommentar)