PCB mit CNC (Teil 1): Wie Sie Ihre Leiterplattenbahnen fräsen, anstatt sie zu ätzen
über
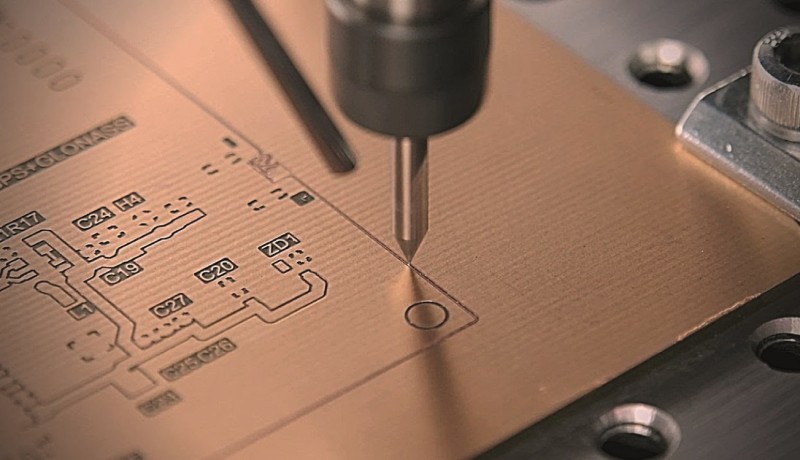
Für das prototyping-production oder die Produktion von Kleinserien kann die Nutzung externer PCB-Dienstleistern teuer oder zumindest zeitraubend sein. Aus verschiedenen Gründen kann auch das chemische Ätzen nicht praktikabel sein. In diesen Fällen könnte das CNC-Fräsen einer gedruckten Schaltung aufgrund der Genauigkeit, der einfachen Umsetzung und vor allem aufgrund der Tatsache, dass Sie Ihre geliebte Platine sehr schnell fertigstellen und zum Löten vorbereiten können, eine gute Alternative sein!
Jeder, der sich mit praktischer Elektronik beschäftigt, sei es als Hobby oder beruflich, wird früher oder später eine Leiterplatte herstellen. Prototypen werden mit Breadboards oder Multi-Loch-Matrix-Leiterplatten erstellt. Dabei handelt es sich aber fast immer um Schaltungen, die man nicht als endgültig betrachten kann, obwohl es einigen Leuten gelingt, mit solchen Medien gut gemachte Designs zu erstellen. Der Königsweg des Prototyps, der auch endgültig werden kann, ist die Leiterplatte (PCB - Printed Circuit Board). Meist wird sie von einem professionellen Dienstleister angefertigt und die Kosten dafür sind heutzutage tragbar, es gibt für jeden Geldbeutel etwas. Ein solcher Service ist eine Option für eine endgültige Schaltung, die alle Tests bestanden hat und vielleicht in die Produktion gehen muss, auch für kleine Auflagen. Befinden Sie sich allerdings in der Design-Phase und benötigen für Ihre Experimente eine stabile Schaltung mit einer Grundplatte und Sie gehen davon aus, dass Sie nach den Tests noch Änderungen vornehmen, dann lohnen sich die Kosten für eine professionelle Leiterplatte möglicherweise nicht.
Bis vor wenigen Jahren gab es nur eine einzige Möglichkeit, eine Leiterplatte selbst herzustellen. Sie mussten den Schaltkreisentwurf durch Fotoätzen erstellen oder Tonertransfer auf einer Kupferplatte fixieren und die Platte anschließend in Eisenchlorid (oder andere geeignete Chemikalien) tauchen, um überschüssiges Kupfer zu entfernen. Während eine Schaltung in SMT (Surface Mount Technology) zu diesem Zeitpunkt fertig war, war bei der THT (Through Hole Technology) der zweite Schritt das Bohren. An dieser Stelle begannen die Probleme. Wie wir alle wissen, sind die Löcher nicht alle gleich groß und erfordern daher Bohrer mit unterschiedlichem Durchmesser. Zudem muss man jedes Loch genau zentrieren. Natürlich war dieser Schritt enorm zeitaufwendig und die Ergebnisse waren selten perfekt. Diese Techniken werden auch heute noch eingesetzt, weil die Schritte bis zum Ätzen in Eisenchlorid schnell sind und gute Ergebnisse liefern. Der Umgang mit Chemikalien in kleinen Umgebungen, wie einem Zimmer zu Hause oder einem kleinen Labor, kann allerdings ziemlich gefährlich sein.
Hier kommen CNC-Maschinen ins Spiel. Sie sind aufgrund ihrer immer erschwinglicheren Kosten inzwischen weit verbreitet. Damit wurde die Welt des Prototypings zweifellos revolutioniert. Sie können nun perfekte Schaltkreise ohne Chemikalien herstellen. Wichtiger ist allerdings, dass sie korrekt dimensionierte und perfekt zentrierte Löcher erhalten. In diesen neuen Artikeln werden wir diese exzellente Kombination zusammen mit einer Vielzahl von Open-Source- oder kostenloser Software nutzen. Damit lernen wir, wie man eine durchschnittliche Leiterplatte mit PTH-Komponenten herstellt. Wir werden alle notwendigen Schritte durchleuchten, um die Datei zu erhalten, die die CNC für die Ätz- und Bohrphase steuert. Ferner werden wir eine einfache mechanische Ergänzung vorschlagen, um die zu bearbeitende Platine mit großer Leichtigkeit und Präzision an der Halteplatte zu befestigen.
Die von uns eingesetzten Programme sind: Eagle 9.6.2 free, um die Gerber-Dateien zu erzeugen, FlatCAM v.8.5 Open Source herunterladen, womit dem die CAM-Dateien in G-Code-Sprache erzeugt werden. Candle v.1.1.7 ist ebenfalls Open Source Downlowad hier. Es sorgt für die Steuerung der CNC und übermittelt die notwendigen Befehle an unseren Controller. Das Programm Eagle von Autodesk ist nicht quelloffen. Sie müssen es also herunterladen und sich dann auf der Website registrieren, um es als kostenlose Version mit eingeschränkten Funktionen nutzen zu dürfen. Wir gehen jedoch davon aus, dass der Schaltplan und die Zeichnung der Leiterplatte bereits erstellt wurden. Daher sehen wir uns direkt an, wie Sie die Gerber-Dateien generieren. Haben Sie also eine andere CAD-Software, müssen Sie nur die Gerber-Dateien generieren und können direkt zum zweiten Schritt springen, den CAM-Dateien.
DRU-Prüfung
Zuvor müssen Sie den Schaltplan und die dazugehörige Leiterplatte zeichnen. Außer in sehr seltenen Fällen ist es immer praktisch, die Leiterplatte mit einer sogenannten "Grundplatte" auszustatten. Sie verbindet nicht nur alle Massepunkte der Schaltung, ohne dass die entsprechenden Leiterbahnen gezeichnet werden müssen, sondern füllt auch alle leeren Stellen der Leiterplatte aus. Das ist beim Ätzen sehr nützlich. Andernfalls würden wir uns das Leben dadurch erschweren, dass wir das gesamte überschüssige Kupfer entfernen müssten. Das würde wiederum die Ätzzeit unverhältnismäßig verlängern oder wir müssten während der CAM-Bearbeitungsphase eine Reihe von isolierten Polygonen erstellen. Als Beispiel verwenden wir die Zeichnung in Abbildung 1.
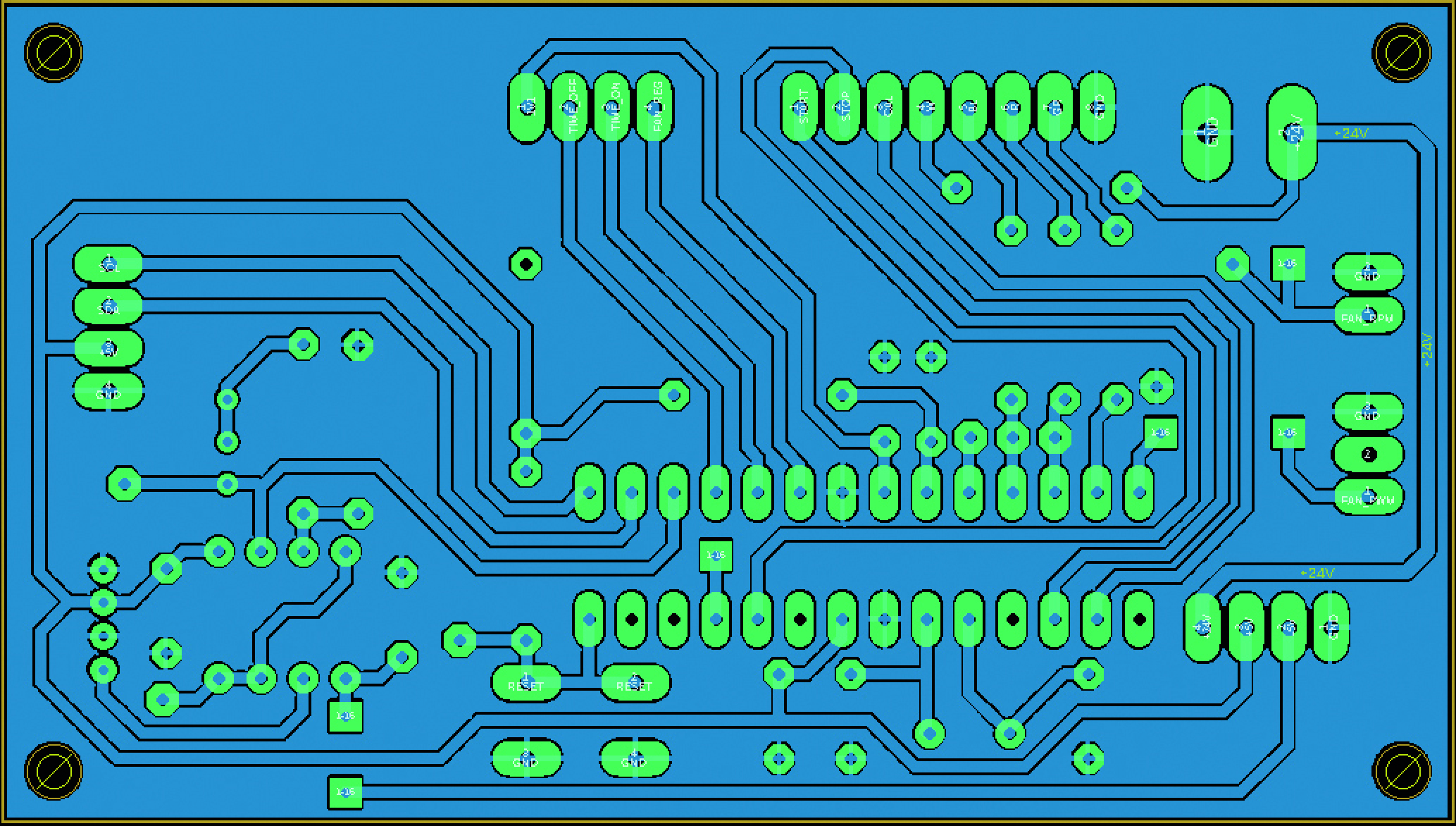
Der erste Arbeitsschritt im CAD-Programm besteht darin, eine spezielle DRU-Datei (so heißt sie bei Eagle) zu erstellen. Sie enthält die Design-Vorgaben, also im Wesentlichen die Abmessungen der Leiterbahnen und Pads sowie ihre Abstände, je nach Art der zu erstellenden Leiterplatte. In der Tat muss man bedenken, dass die typischen Standardeinstellungen von CAD-Programmen für die Leiterplattenherstellung bei einem professionellen Dienstleister in Ordnung sind. Bei einem manuellen Verfahren ist das aber nicht so. Die Parameter, auf die Sie Einfluss nehmen müssen, sind im Wesentlichen die Mindestabmessungen der Anschlussbahnen, Pads (Lötpunkte der Komponenten) und Vias (Verbindungspunkte zwischen der Ober- und Unterseite der Leiterplatte) sowie die Abstände zwischen diesen Komponenten und zwischen ihnen und der Grundplatte. Das ist das gesamte angrenzende Kupfer, das die übrigen Flächen der Leiterplatte bedeckt und geerdet ist. Wählen Sie die richtigen Werte nicht, kann es schwierig werden, die Komponenten auf die Leiterplatte zu löten. Schauen wir uns die relevanten Parameter an und welche Werte wir ihnen zuweisen sollten:
- Clearance (Freiraum): Das ist der Mindestabstand zwischen den verschiedenen Komponenten des Designs: Leiterbahnen, Pads und Vias. In unserem Fall haben wir einen Wert von 8 mils verwendet, was etwa 0,2 mm entspricht. Das ist ein Standardwert, der auch im Servicebereich verwendet wird. Es bedeutet, dass Sie mit dem Lötkolben recht geschickt umgehen müssen, da das Zinn sonst in benachbarte Leiterbahnen oder Pads oder die Grundplatte eindringen und Kurzschlüsse verursachen kann. Der Wert von 0,2 mm entspricht der Größe der Bohrerspitze, die wir mit unserer CNC verwendet haben. Es reicht also ein Durchgang aus, um beim Ätzen überschüssiges Kupfer von der Kupferplatte zu entfernen (Abbildung 2). Sind Sie der Meinung, dass Sie keine ausreichenden Lötkenntnisse haben, empfehlen wir Ihnen, diesen Wert auf 16 mils zu verdoppeln. In diesem Fall können Sie einen 0,4-mm-Bohrer einsetzen oder immer den 0,2-mm-Bohrer, mit dem die CNC zwei benachbarte Durchgänge bohrt. Auf jeden Fall kann beim Löten die Verwendung von Flussmittel eine gute Hilfe sein. Tragen Sie es vor dem Löten mit einem Pinsel auf, erleichtert es das Löten und verhindert, dass das Zinn benachbarte Leiterbahnen oder Pads berührt.
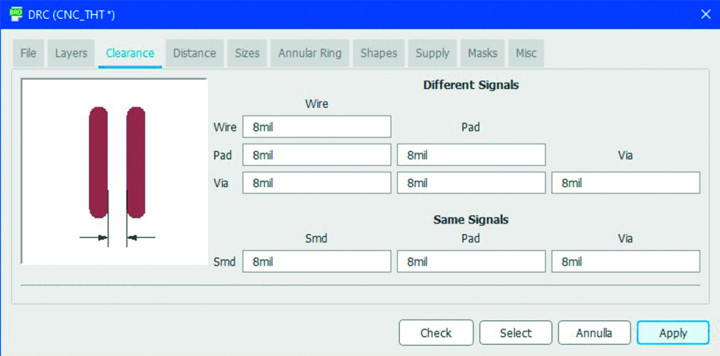
- Größen: Das sind die Mindestgrößen der Spuren und der Mindestdurchmesser der Löcher. Verwenden Sie einen zu kleinen Wert für die Spurbreite, laufen Sie Gefahr, dass ein Grat vom Fräsen extrem dünne oder sogar gebrochene Spuren erzeugt. Wir haben 24 mils verwendet, was etwa 0,6 mm entspricht. Der Durchmesser der Löcher ist für unsere Bedürfnisse irrelevant, aber ein Wert von 16 mils ist in Ordnung (Abbildung 3).
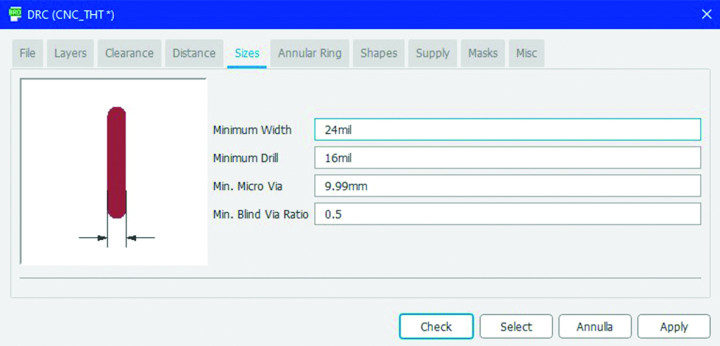
- Kreisring: Das sind die Abmessungen von Pads und Durchkontaktierungen. Die Standardwerte aus den Bibliotheken der verschiedenen Bauteile sind für einen Dienstleister in Ordnung. Arbeiten Sie aber mit CNC, verliert der äußere Rand leicht etwas, während beim Bohren ohne Metallisierung mehr Material im mittleren Teil abgetragen wird. Das führt möglicherweise zu einer übermäßigen Verkleinerung des Lötraums um die Rheophoren führen, mit den daraus folgenden Schwierigkeiten. Die Abmessungen werden als Prozentsatz des Innendurchmessers der Bohrung innerhalb eines Mindest- und eines Höchstwerts definiert. Für Pads lassen sich diese Werte separat für die Ober-, Unter- und Innenseite der Kupferplatte festlegen. Der letzte Wert ist hingegen irrelevant, da er nur für professionelle mehrlagige Leiterplatten verwendet werden kann, die mit handwerklichen Techniken nicht realisierbar sind. Bei Durchkontaktierungen sind die Abmessungen für die beiden Außenflächen eindeutig. Für den inneren Wert gilt das Gleiche gilt wie bei den Pads. Microvias fallen ebenfalls unter die professionellen Typen. In unserem Fall haben wir eine Vergrößerung von 50 % gegenüber den Bauteilbibliotheken festgelegt, mit einem Wertebereich zwischen 10 und 40 mils (Abbildung 4).
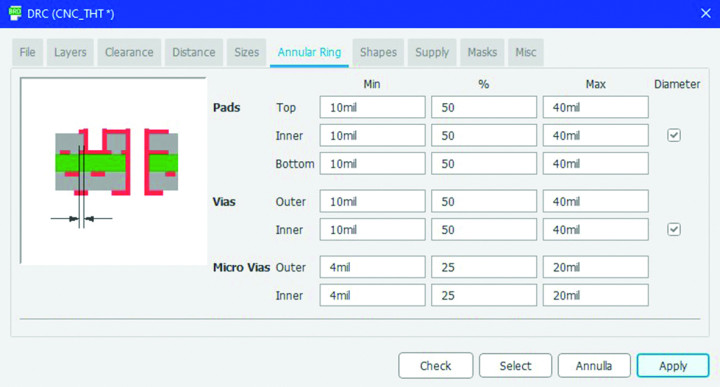
Sie finden die Datei CNC_THT.dru hier: How To Mill Your PCB Tracks Instead Of Etching Them"], die Sie in Eagle in den Ordner dru kopieren sollten. Sobald Sie die PCB-Zeichnungsdatei geöffnet haben, müssen Sie den Menüpunkt Tools-DRC… verwenden, auf die Schaltfläche Load… klicken und die Datei laden. Klicken Sie zuerst auf Apply und anschließend auf Check, wendet Eagle die Einstellungen an und prüft dann, ob die Merkmale der Zeichnung mit denen der DRU übereinstimmen. Wenn nicht, wird eine Maske mit allen gefundenen Fehlern geöffnet. In Abbildung 5 haben wir absichtlich eine DRU für CNC auf ein PCB-Design angewendet, das für den Druck bei einem Dienstleister erstellt wurde. Als Ergebnis bekommen wird nicht weniger als 387 Fehler und 30 Warnungen. Genauer gesagt, wir haben:
- 31 Clearance: bedeutet, dass in 31 Fällen die Mindestabstände zwischen den Spuren nicht eingehalten wurden;
- 1 Drill Size: bedeutet, dass in einem Fall die Größe eines Lochs kleiner als die erwartete Mindestgröße ist;
- 5 Overlap: bedeutet, dass es 5 Probleme mit sich überschneidenden Spuren gibt, die darauf zurückzuführen sind, dass die verwendeten DRU-Einstellungen die PADs vergrößern und sie sich gegenseitig überschneiden. Eigentlich würde dieser Fehler auch mit der korrekten DRU auftreten;
- 350 Width: bedeutet, dass an 350 Punkten die Spuren nicht die von der DRU festgelegte Mindestgröße erreichen;
- 30 Wire Stub: das sind wiederholte Wiederholungen an einigen Stellen der Spuren. Das passiert leicht, wenn wir einen Track löschen, um ihn neu zu erstellen, aber wir merken nicht, dass wir ihn nicht vollständig gelöscht haben, vor allem in PADs.
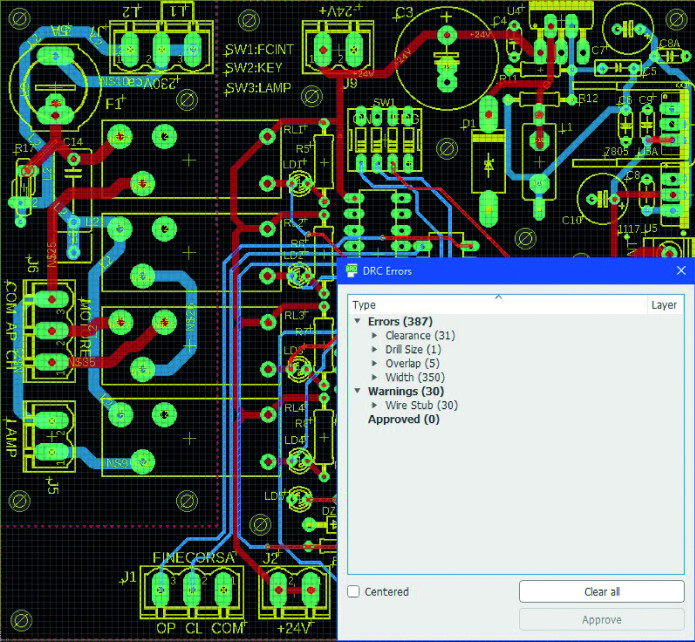
Eagle hilft uns beim Finden und Beseitigen von Fehlern, da wir sie einfach einzeln auswählen und sich ein Markierungsfeld öffnet, das den vom ausgewählten Fehler betroffenen Punkt oder Abschnitt anzeigt. Abbildung 6 zeigt genau den Hinweis auf einen Abstandsfehler – die zwischen den beiden PADs verlaufend Spur ist zu nah und entspricht nicht den Parametern der DRU. Daher muss man an dieser Stelle verkleinern oder verschieben, bis der Fehler behoben ist. In einigen Fällen können Sie beschließen, dass der von der DRU-Prüfung angezeigte Fehler für die Herstellung Ihres Prototyps irrelevant ist. In diesem Fall können Sie diesen Fehler auswählen und auf die Schaltfläche Approve klicken, damit er aus der Liste entfernt wird. Sie sollten diese Option aber nur verwenden, wenn Sie genau wissen, was Sie tun.
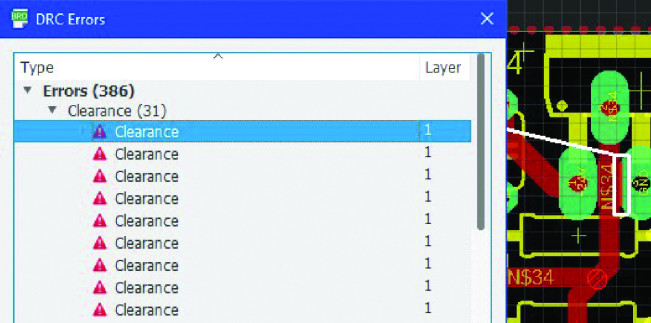
Generierung von Gerber-Dateien
Sobald Sie alle von der DRU angezeigten Fehler beseitigt (oder genehmigt) haben, können Sie mit der Erstellung der Gerber-Datei fortfahren. Mit Eagle ist das ziemlich einfach.
Im Folgenden finden Sie eine Liste mit den entsprechenden Schritten:
- Klicken Sie auf CAM Processor (Abbildung 7).
- Wählen Sie TOP COPPER, um die Vorschau der Oberseite der Leiterplatte zu prüfen (nützlich für doppelseitige SMT- oder THT-Schaltungen);
- Wählen Sie BOTTOM COPPER, um die Vorschau der Oberseite der Leiterplatte zu prüfen (nützlich für einseitige THT);
- Aktivieren Sie Board shape um einen Rand um die Leiterplatte zu erhalten (nützlich beim endgültigen Zuschneiden der Leiterplatte);
- Aktivieren Sie Cutouts, um die inneren Kreise der großen Löcher zu erhalten. Nehmen Sie KEINE ÄNDERUNG in der Sektion Advanced vor, die im Grunde zum Spiegeln von THT-Platinen dient. Wir werden das mit FlatCAM bearbeiten;
- Klicken Sie auf Process Job: Eagle erstellt sofort am ausgewählten Ort den Ordner CAMOutputs mit allen Dateien, die für die Verarbeitung der Leiterplatte durch einen Dienstleister benötigt werden.
Sie können den Ordner dort lassen, wo er erstellt wurde oder ihn für die nächsten Schritte an einen geeigneteren Ort verschieben.

Erzeugung von CAM-Dateien verfolgen
Nach der Installation von FlatCAM müssen Sie das Programm starten und bei der ersten Verwendung diese einfachen Schritte ausführen:
- Navigieren Sie zur leeren Zeile am unteren Rand der Programmoberfläche (Abbildung 8);
- Ist die Shell nicht sichtbar, führen Sie den Befehl aus: Tool ⇒ Command line;
- Tippen SIe get_sys excellon_zeros und betätigen Sie die EINGABETASTE auf der Tastatur.;
- Schreiben Sie set_sys excellon_zeros T und betätigen Sie die EINGABETASTE auf der Tastatur;
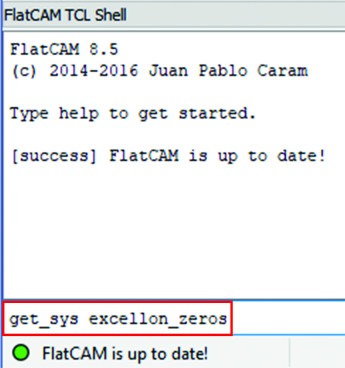
Die beiden Code-Zeilen sind notwendig, damit Sie die Löcher deutlich sehen können, wenn Sie eine Datei vom Typ Bohrer laden. Wir sehen uns das später noch genauer an. Der Vorgang ändert die Programmoptionen dauerhaft, sodass er in Zukunft nicht mehr ausgeführt werden sollte. An dieser Stelle können Sie die Shell auch schließen, um so viel Platz wie möglich für das Hauptfenster zu lassen. Führen Sie dazu einfach erneut den Befehl Tool ⇒ Command line command aus.
Führen Sie den Befehl File ⇒ Open Gerber… aus und suchen Sie die zu öffnende Datei im Ordner CAMOutputs/GerberFiles. Da wir mit einer einseitigen THT-Schaltung arbeiten, interessiert uns nur die untere (Datei copper_bottom.gbr). Bei SMT-Schaltungen würden wir die Datei copper_top.gbr benötigen. Abbildung 9 zeigt die Art von Bild, die Sie im mittleren Fenster sehen, nachdem die Datei geladen wurde.
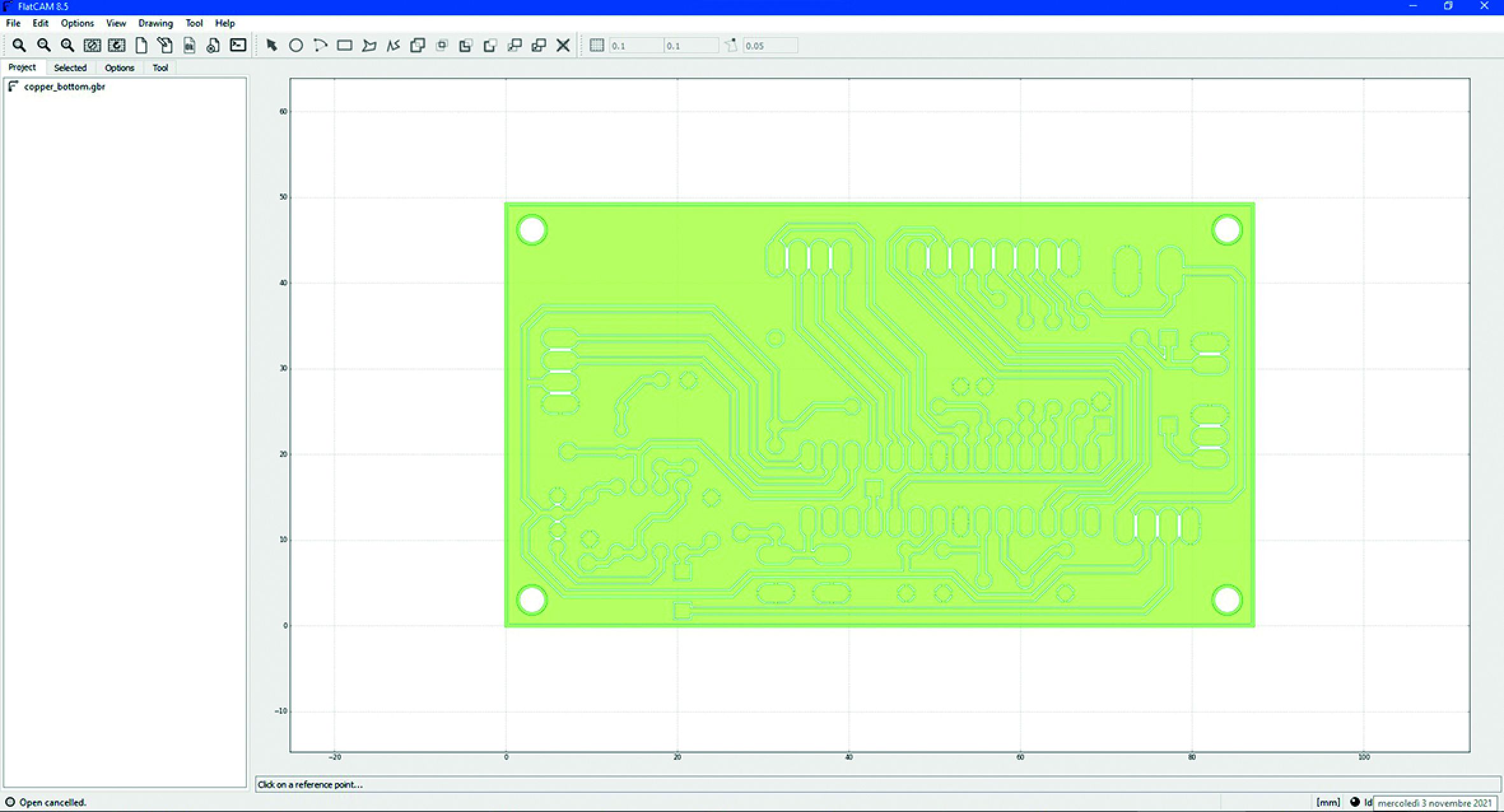
Öffnen Sie die Registerkarte Options und setzen Sie das Feld Untis auf mm. Da die PCB-Zeichnung immer von der Bauteilseite aus erstellt wird, würde die Gravur seitenverkehrt erfolgen, sodass eine Spiegelung notwendig ist. Wir müssen den Befehl Tool ⇒ Double-Sided PCB Tool ausführen und diese Parameter einstellen (Abbildung 10):
- Bottom layer = copper_bottom.gbr;
- Mirror axis = Y;
- Axis location = Box;
- Point/Box = copper_bottom.gbr;
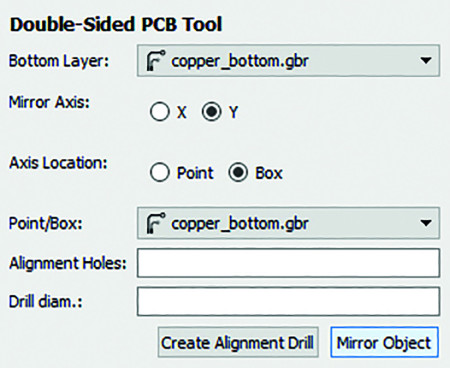
Klicken Sie auf Mirror Object, ist die Leiterplatte nun direkt von der Lötseite (Unterseite) sichtbar.
Beachten Sie bitte: Natürlich müssen Sie die Registerkarte Tool nicht ändern, wenn wir mit der Oberseite arbeiten müssen (SMT-Schaltungen). Öffnen Sie die Registerkarte Project und klicken Sie doppelt auf das Projekt copper_bottom.gbr. Es öffnet sich die Registerkarte Selected, in der wir alle folgenden Optionen einstellen müssen:
Plot-Optionen:
- Aktivieren Sie die Optionen Plot und Solid.
Isolations-Routing:
- Tool dia: Hier müssen wir den Durchmesser der Bohrerspitze eingeben, die wir für die Gravur verwenden. Die von uns verwendete DRU sieht einen Abstand zwischen den Spuren bzw. zwischen den Spuren und der Grundplatte von 8 mils (ca. 0,2 mm) vor. Wir müssen also einen Fräser mit einem Durchmesser wählen, der diesem Wert entspricht oder ein Vielfaches davon ist. Es gibt Fräser mit 0,1 mm und 0,2 mm. Setzen wir den 0,2-mm-Bohrer ein, graviert die CNC in einem einzigen Durchgang genau den von der DRU vorgegebenen Bereich. Benutzen wir hingegen den 0,1-mm-Bohrer verwenden, macht die CNC automatisch zwei Durchgänge nebeneinander, um die gleiche Dicke zu realisieren. Wir stellen 0,2 ein.
- Width: Die Breite wird verwendet, um die Isolierung der Leiterbahnen zu erhöhen. Es ist sinnvoll, dieses Feld zu verwenden, wenn keine vorausgehende Aktion an der DRU auf die Leiterplatte angewendet wird. In unserem Fall setzen wir es auf 1 (einzelner Durchgang). Wird eine größere Anzahl von Durchläufen eingestellt, erstellt FlatCAM für jeden Durchlauf eine grbl-Datei, sodass die Leiterplatte mehrfach geätzt werden muss. Bei jedem neuen Durchlauf wird der Fräser um einen Bruchteil des Wertes verschoben, der im nächsten Feld Pass overlap angegeben ist. Beträgt die von der DRU gelieferte Isolierung beispielsweise 0,2 mm und wir wollen sie aber auf 0,3 mm erhöhen, haben aber nur den Fräser mit 0,2 mm, setzen wir dieses Feld auf 2 und das nächste Feld (Pass overlap) auf 0,5 (50 %). Dann hat der zweite Durchgang 50 % Überlappung mit dem ersten Durchgang hat und die zweite Gravur beträgt folglich 0,1 mm.
- Pass overlap: dieses Feld wird nur verwendet, wenn die Breite größer als 1 ist – andernfalls wird es ignoriert.
- Combine passes: es kann sinnvoll sein, diese Option zu aktivieren, wenn Width>1 ist, wenn FlatCAM eine einzige Datei anstelle einer Anzahl von Dateien erzeugt, die dem Wert der Breite entspricht.
- Klicken Sie auf Generate Geometry, erscheint eine rote Linie innerhalb der Isolationsspuren. Sie zeigt an, dass ein Durchgang ausreicht, um das überschüssige Kupfer zu entfernen. In Abbildung 11 haben wir das Bild vergrößert und sowohl die Verwendung des 0,2-mm-Fräsers (oben) als auch des 0,1-mm-Fräsers (unten) simuliert. Damit wollen wir zeigen, dass die CNC im zweiten Fall zwei Durchgänge durchführen muss, um die von der DRU erwartete Isolierung zu gewährleisten.
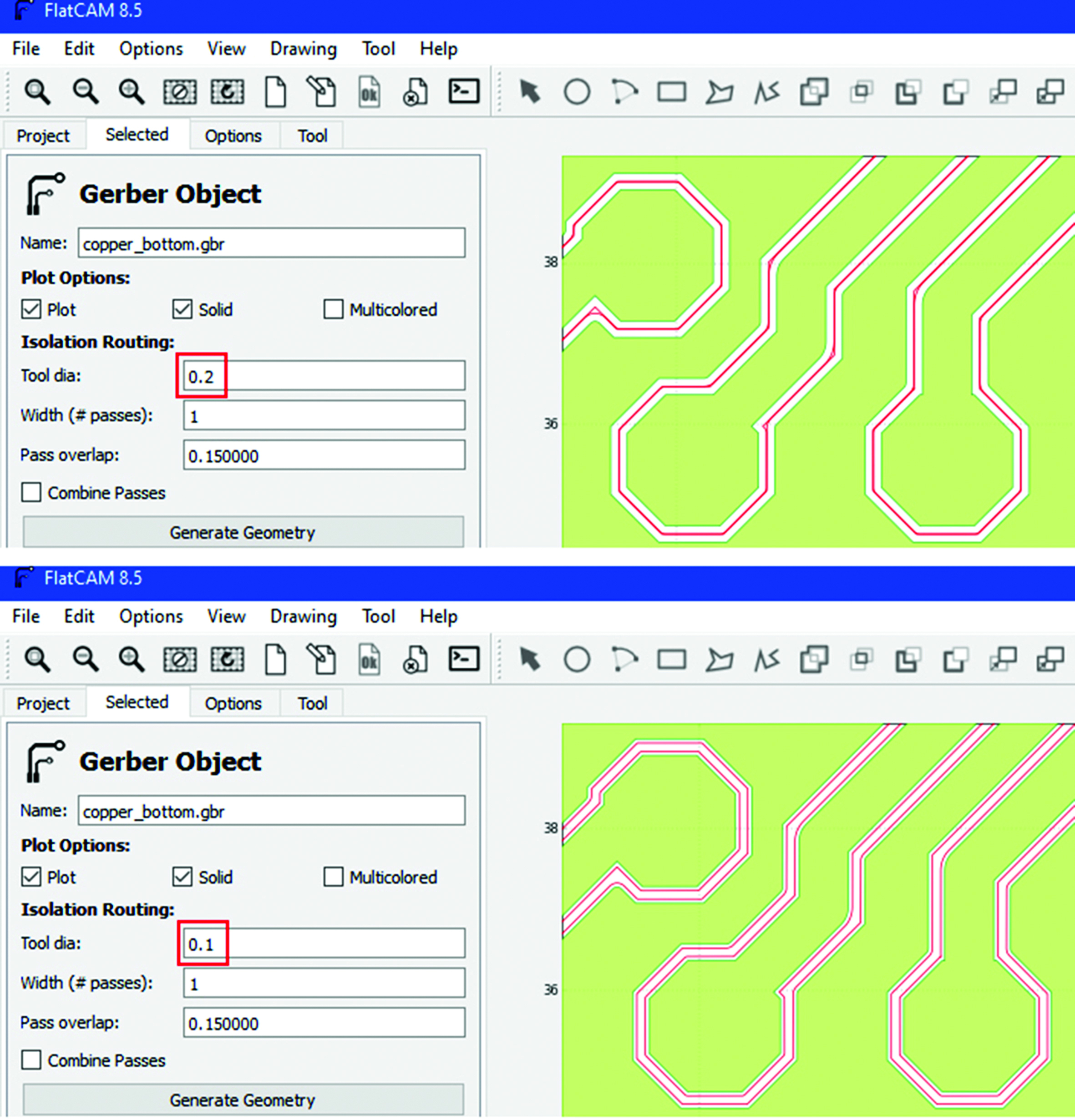
Falls Sie nach dem Vorgang der Generierung einen Fehler feststellen, müssen Sie diese Schritte ausführen:
- Öffnen Sie den Reiter Project;
- Wählen Sie das Projekt copper_bottom.gbr_iso, das gerade vom Programm erstellt wurde;
- Drücken Sie auf der Tastatur Delete (entf), um es zu löschen;
- Klicken Sie doppelt auf das Projekt copper_bottom.gbr;
- Wiederholen Sie die vorher beschriebene Reihenfolge der Vorgänge.
Ist jedoch alles in Ordnung, öffnen Sie die Registerkarte Project und klicken Sie doppelt auf das Projekt copper_bottom.gbr_iso. Die Registerkarte Selected wird erneut geöffnet und Sie müssen die folgenden Werte einstellen:
- Plot: aktivieren Sie die Schaltfläche;
- Cut z: Gravurtiefe in Millimetern. Normalerweise beträgt die Kupferdicke 0,035 mm, sodass Sie einen größeren Wert eingeben müssen. Berücksichtigen Sie auch die Toleranzen der Spindelbewegung, normalerweise sind -0,06 bis -0,08 in Ordnung;
- Travel z: ist der Hub des Fräsers während der Bewegung, wenn nicht graviert wird. Sie können 1,5 mm einstellen;
- Feed rate: Graviergeschwindigkeit in mm/min, ein niedriger Wert benötigt viel Zeit, bietet aber große Zuverlässigkeit. Ein hoher Wert erzeugt eine schnelle Gravur, birgt aber ein gewisses Risiko für den Fräser oder es kommt zu übersprungenen Schritten. Wir haben einen guten Kompromiss mit einem Wert zwischen 50 und 80 gefunden;
- Tool dia: 0.2 (entspricht dem oben eingegebenen Wert);
- Spindle speed: maximale Drehzahl der Spindel. Der Wert dient zur Verarbeitung des vom CNC-Controller erzeugten PWM-Signals. Unser Modell sieht diese Möglichkeit vor, und aus dem Datenblatt der Spindel erfahren wir, dass sie bei 36 V 9000 U/min erreichen kann. Daher geben wir diesen Wert ein. Hat der von Ihnen verwendete Controller stattdessen eine einfache Relaisschaltung, können Sie das Feld ignorieren. Sie können es leer lassen (Abbildung 12).
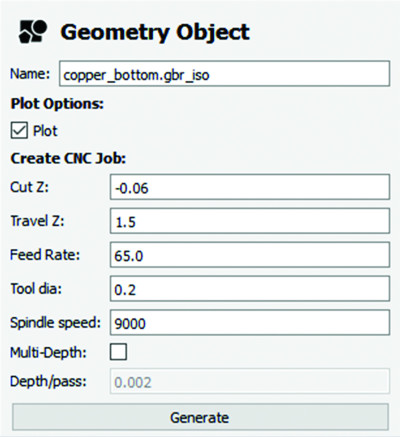
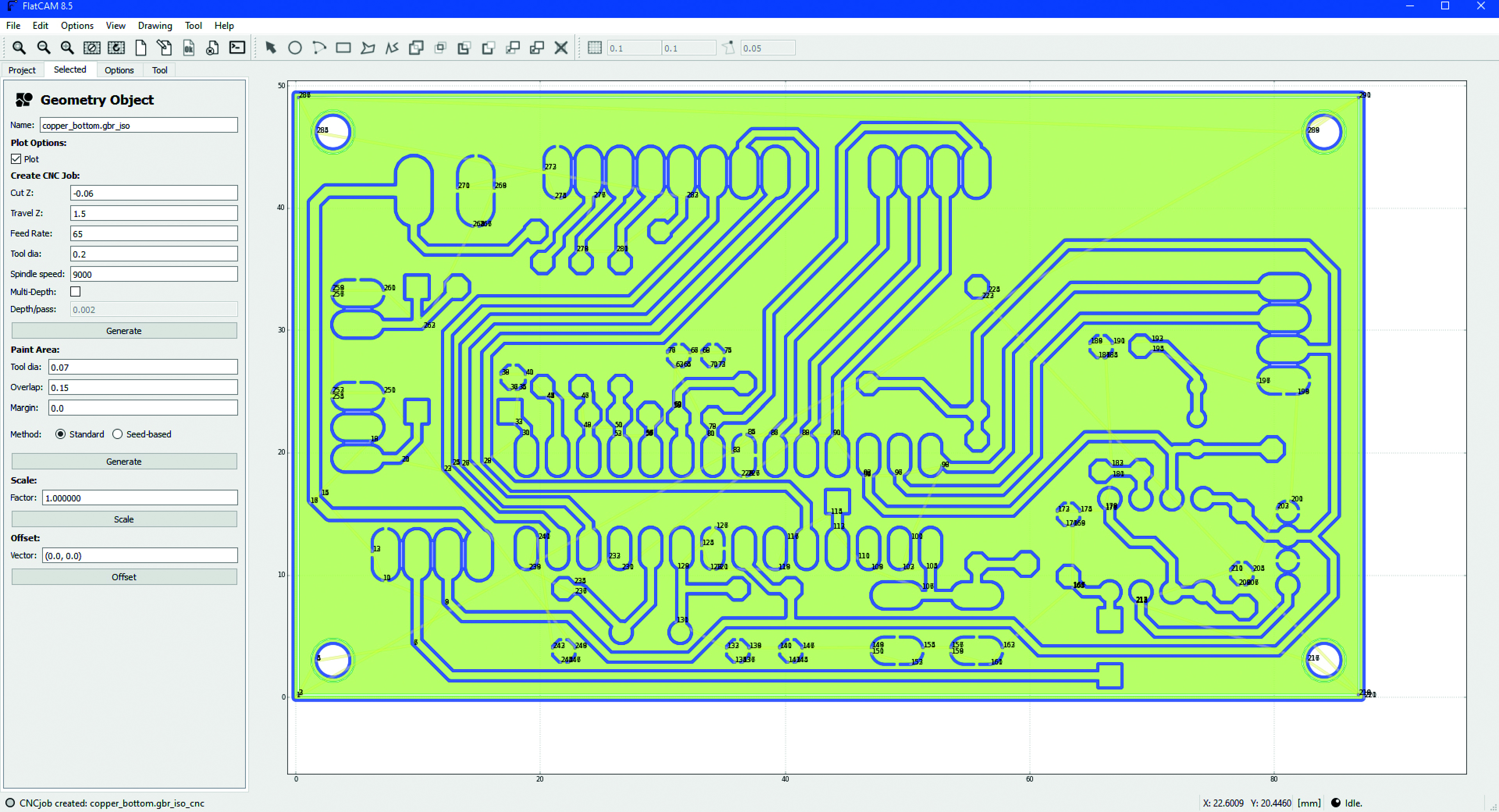
Falls Sie nach dem Generierungsvorgang Fehler feststellen, müssen Sie folgende Schritte durchführen:
- Öffnen Sie den Reiter Project.
- Wählen Sie das Projekt copper_bottom.gbr_iso_cnc, das gerade vom Programm erstellt wurde.
- Drücken Sie Delete (entf) auf der Tastatur, um es zu löschen.
- Klicken Sie doppelt auf das Projekt copper_bottom.gbr_iso.
- Wiederholen Sie die vorher beschriebene Reihenfolge der Vorgänge.
Ist hingegen alles in Ordnung, öffnen Sie die Registerkarte Project und klicken Sie doppelt auf Projekt copper_bottom.gbr_iso_cnc. Der Reiter Selected öffnet sich erneut. Nun müssen wir die Option Plot aktivieren und in das Feld Tool dia denselben Wert eingeben, der in den vorherigen Masken verwendet wurde (in unserem Fall 0. 2). Klicken Sie anschließend auf Update Plot. Warten Sie einige Sekunden, auch wenn scheinbar nichts passiert. Klicken Sie dann auf Export G-Code und speichern Sie die Datei als Name_PCB.nc, wobei Name der Name Ihres Projekts ist. Es ist nicht zwingend erforderlich, einen bestimmten Namen zu vergeben. Tun Sie das aber, können Sie einen Ordner erstellen, der alle Ihre Dateien enthält, um sie später zu verwenden. Es ist lediglich die Endung .nc wichtig, sonst wird die Datei von der Software Candle nicht erkannt.
Sind Sie an diesem Punkt angelangt und Ihr Entwurf enthält SMD-Bauteile und somit keine Löcher vorhanden sind, können Sie FlatCAM schließen und direkt zur Gravur übergehen. Andernfalls müssen Sie mit dem nächsten Schritt dieses Programms fortfahren.
CAM-Löcher Datei erzeugen
Führen Sie den Befel File ⇒ Open Excellon… aus und öffnen Sie die Date drill_1_16.xln, Sie finden Sie im Ordner CAMOutputs/DrillFiles. Haben Sie die Leiterplatte zuvor gespiegelt, werden Sie feststellen, dass die Löcher (dargestellt durch rote Kreise) nicht mit den darunter liegenden Pads oder Durchkontaktierungen übereinstimmen (Abbildung 14). Sie müssen die Funktion Tool ⇒ Double-Sided PCB Tool ausführen und nachfolgende Parameter festlegen:
- Bottom layer = drill_1_16.xln;
- Mirror axis = Y;
- Axis location = Box;
- Point/Box = copper_bottom.gbr.
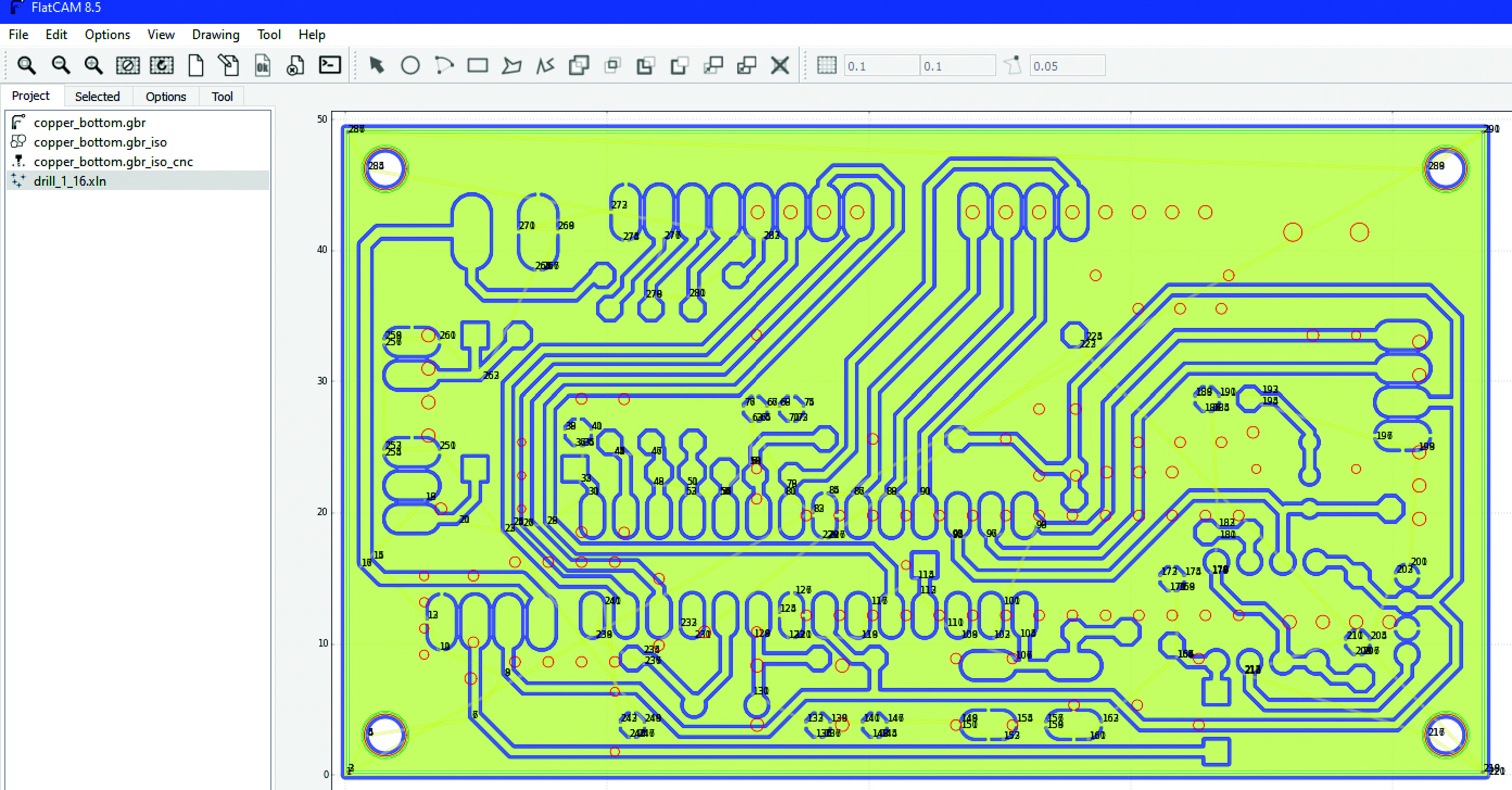
Klicken Sie auf Mirror Object, werden die Löcher sofort perfekt auf die darunter liegenden Pads und Durchkontaktierungen zentriert (Abbildung 15). Sollten Sie nach der Spiegelung Fehler feststellen, müssen Sie diese Schritte durchführen:
- Öffnen Sie den Reiter Project;
- Löschen Sie das Projekt drill_1_16.xln indem Sie Delete (entf) auf Ihrer Tastatur drücken.;
- Führen Sie den Befeh File ⇒ Open Excellon… aus und öffnen Sie die Dat drill_1_16.xln
- Wiederholen Sie die vorher beschriebene Reihenfolge der Vorgänge.
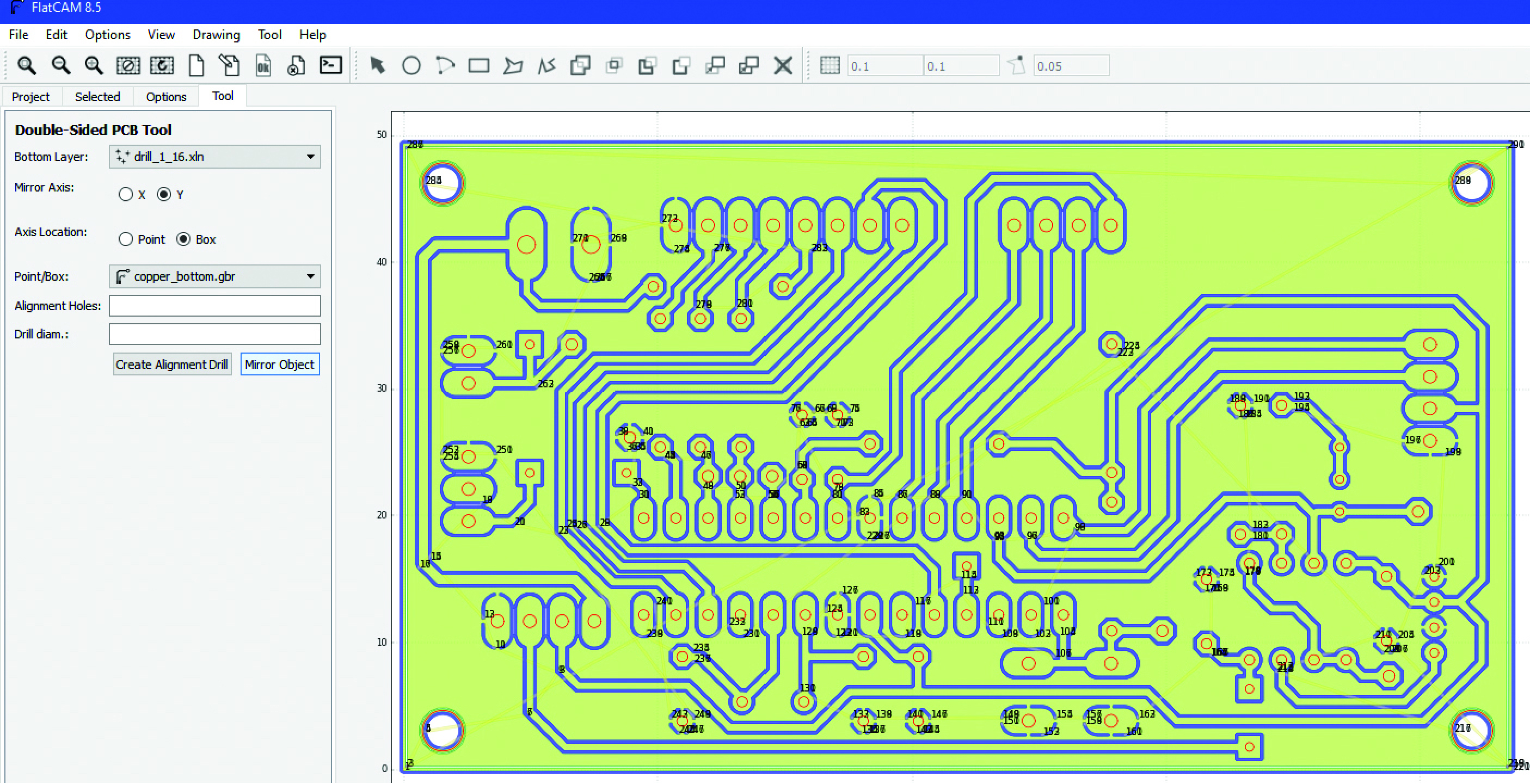
Ist hingegen alles in Ordnung, öffnen Sie den Reiter Project und klicken Sie doppelt auf das Projekt drill_1_16.xln. Der Reiter Selected öffnet sich wieder und Sie müssen die folgenden Einstellungen vornehmen:
Plot options
- Plot:aktivieren Sie die Box;
Tools
- Tools: überprüfen Sie die Reihenfolge der Durchmesser. Sie muss aufsteigend sein, sonst klicken Sie auf #. Die Werte sind die Durchmesser der Bohrer, die für das Bohren der Leiterplatte notwendig sind. Sie werden feststellen, dass einige Werte von der Norm abweichen. Es handelt sich dabei aber um Zehntel- oder Hundertstel-Millimeter. Sie müssen genau genommen nur sie praktisch abrunden und dann den Bohrer mit dem nächstliegenden Wert zu dem Zeitpunkt zu verwenden, zu dem er benötigt wird.
Beispiel: für 0,61 verwenden Sie einen 0,6 mm Bohrer, für 0,686 und 0,7 verwenden Sie immer den 0,7 mm Bohrer;
CNC-Job erstellen
- Cut z: Tiefe des Bohrlochs. PCB ist typischerweise 1,6 mm, der einzugebende Wert ist typischerweise -2,5, wenn die PCB auf Stützen befestigt wird, die wie bei uns über der Platte liegen. Wählen Sie alle Werkzeug-IDs mit der Maus aus, was für die Erstellung der grbl-Datei wichtig ist.
- Travel z: mm des Bohrer-Hubs, um zum nächsten Loch zu gelangen. Stellen Sie 1,5 ein.
- Feed rate: Geschwindigkeit der Z-Achse beim Bohren, in Einheiten pro Minute. Das Programm schlägt einen Wert von 3,0 vor, aber für unsere Zwecke können Sie durchaus einen Wert zwischen 30 und 50 einstellen.
- Tool change: aktivieren Sie die Box, damit die CNC bei jedem Werkzeugwechsel anhält.
- Tool change z: 30 (mm Spindelhub für den Bohrerwechsel).
- Spindle speed: Für die Spindeldrehzahl gilt dasselbe wie oben beschrieben. Für unsere CNC haben wir 9000 eingestellt. Haben Sie aber ein anderes Spindelmodell, müssen Sie sich auf das entsprechende Datenblatt beziehen.
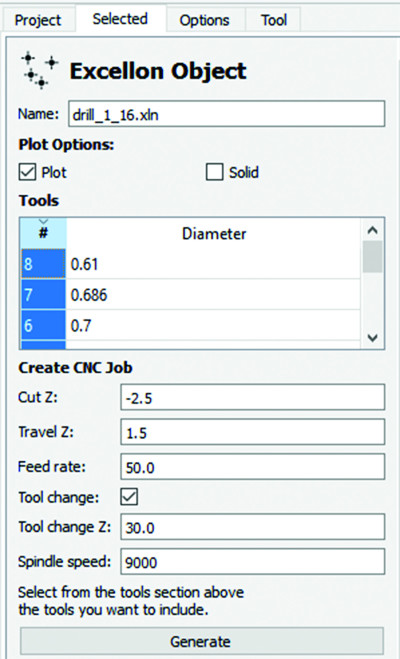
In Abbildung 16 haben wir den gerade beschriebenen Abschnitt mit den eingestellten Werten gezeigt.
Klicken Sie auf Generate werden alle Löcher entsprechend der Bohrreihenfolge nummeriert (Abbildung 17). Ist das nicht der Fall, komplett oder nur für einige Löcher, bedeutet es, dass die Werkzeug-IDs nicht korrekt ausgewählt wurden. Falls Sie nach diesem letzten Vorgang einen Fehler feststellen, müssen Sie diese Schritte ausführen:
- Öffnen Sie den Reiter Project.
- Wählen Sie das Projekt drill_1_16.xln_cnc, das vom Programm gerade erstellt wurde.
- Drücken Sie Delete (entf) auf der Tastatur, um es zu löschen;
- Wiederholen Sie die vorherige Schrittfolge.
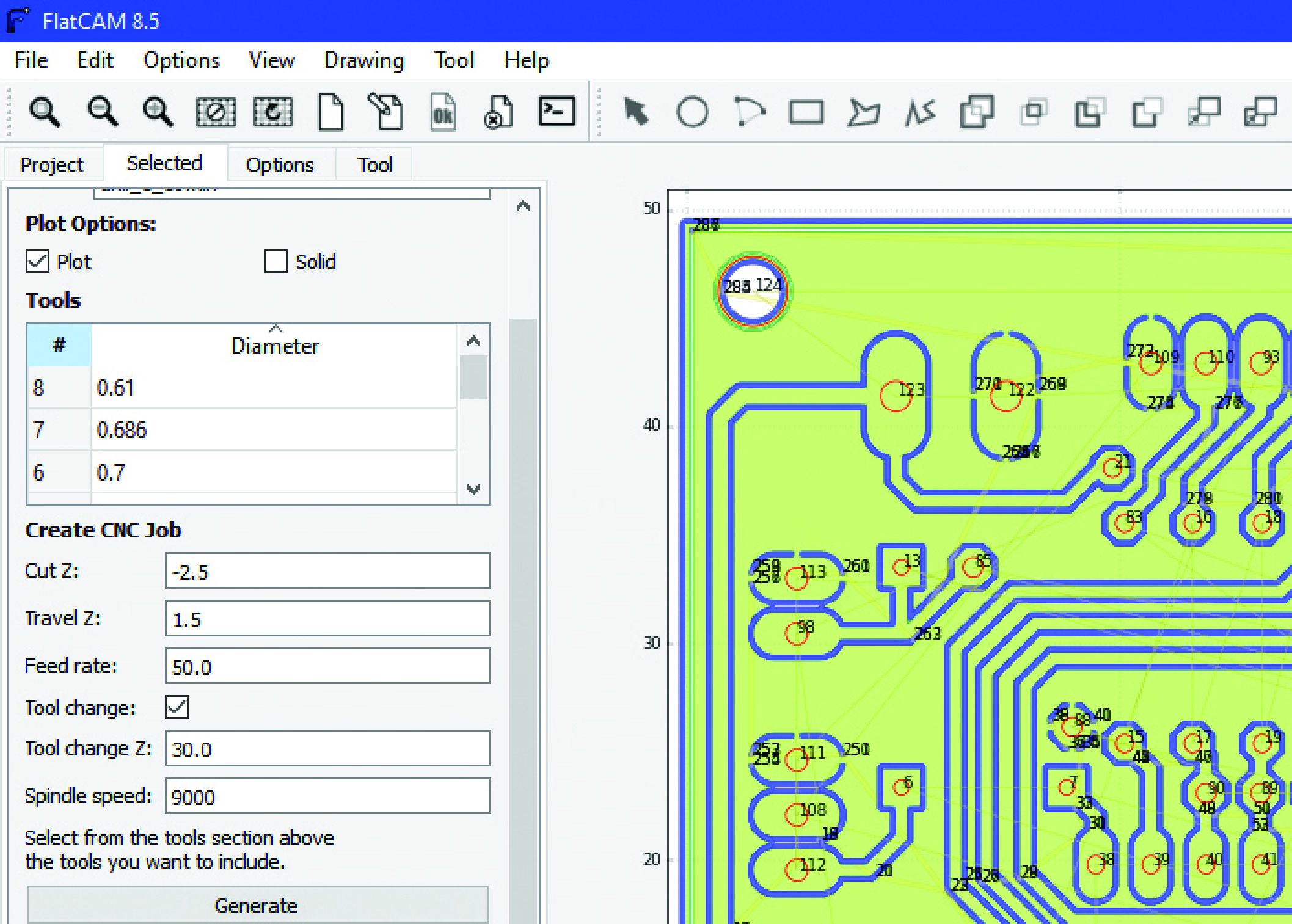
Ist jedoch alles in Ordnung ist, öffnen Sie die Registerkarte Project und klicken Sie doppelt auf das Projekt drill_1_16.xln_cnc. Die Registerkarte Selected öffnet sich erneut und Sie müssen die folgenden Werte einstellen:
- Tool dia: 0.6 (Standardwert für den anfänglichen Bohrdurchmesser).
- Klicken Sie auf Update Plot. Das Bild zeigt nun auch den Bohrpfad an (Abbildung 18).
- Klicken Sie auf Export G-Code.
- Speichern Sie unter Name_FORI.nc, wobei Name der Name Ihres Projekts ist, wie bereits für die Track-Datei erklärt. Auch hier ist es wichtig, die Endung .nc zu verwenden, da die Datei sonst von der Candle-Software nicht erkannt wird.
Mit diesem letzten Schritt haben wir die CAM-Operationen abgeschlossen und verfügen nun über zwei Dateien im grbl-Format. Damit können wir unsere Kupferplatte bearbeiten, indem wir zunächst das überschüssige Kupfer entfernen und dann die erforderlichen Löcher für die Komponenten bohren.
Beachten Sie bitte: Es ist wichtig, das FlatCAM-Projekt zu speichern, vielleicht im gleichen Ordner wie die grbl-Dateien, sodass Sie es wieder öffnen können, um schnell Änderungen an einigen Parametern vorzunehmen, ohne alle bisher gesehenen Schritte wiederholen zu müssen. Verwenden Sie dazu den Befehl File ⇒ Save Project As… und geben Sie den Pfad sowie den Namen an (in der Regel derselbe, der für die beiden grbl-Dateien verwendet wurde), etwa Name_prj ohne Suffix, wobei Name immer der zuvor verwendete Name ist. In der nächsten Folge gehen wir zum praktischen Teil über und beschäftigen uns eingehend mit dem Programm Candle und der Herstellung unserer ersten Leiterplatte
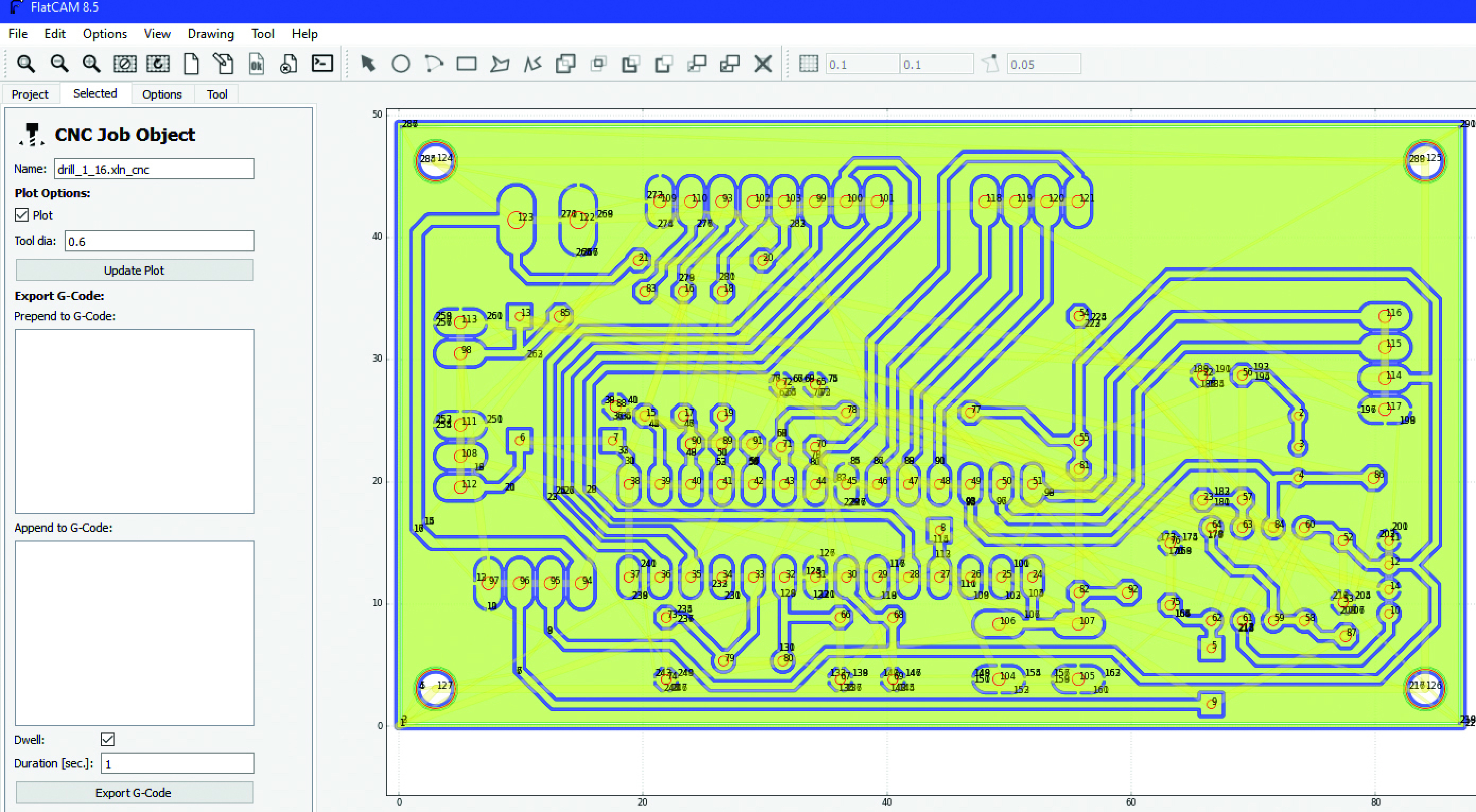
Diskussion (6 Kommentare)