Lithium-Akkus reparieren
über
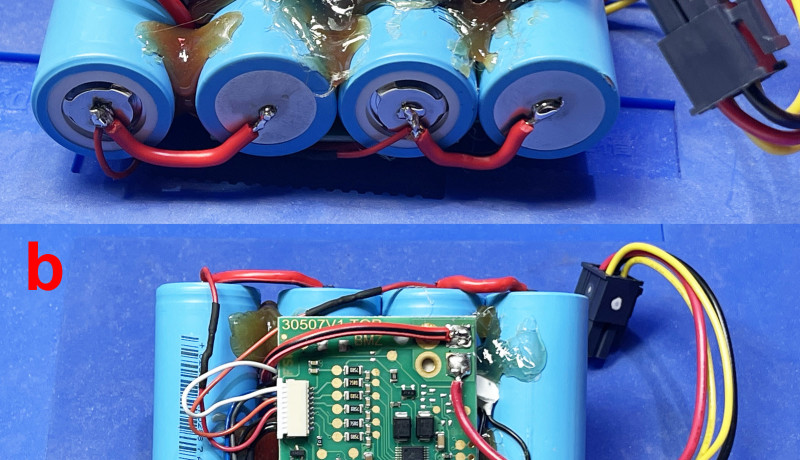
Gegenüber den früheren NiMH-Akkus haben die mit Lithium-Akkus betriebenen Elektrogeräte eindeutig eine längere Lebensdauer, bis die Energiequelle das Zeitliche segnet. Aber irgendwann ist auch der bravste Lithium-Akku erschöpft und hat sich seinen Platz im Recycling-Nirwana verdient. Das habe ich schon ein paar Mal erlebt, auch und gerade bei Bekannten und Verwandten, die den clan-eigenen Elektroniker um Rat baten, wenn ihr akkubetriebenes Gerät nicht mehr oder immer weniger wollte.
Natürlich könnte man dann kurz nach einem passenden Ersatz-Akku googeln und nach kurzer Wartezeit klingelt der Paketbote. Problem gelöst! Was aber, wenn der Drang zum Selbermachen übermächtig wird? Oder wenn weder Hersteller noch Nachbauer nach ein paar Jahren noch einen mechanisch passenden Ersatz-Akku liefern können? Oder aber wenn man die Gelegenheit nutzen will, einen gepimpten Akku mit erhöhter Kapazität zu bauen? Wie Sie sehen, gibt es mehr als einen Grund für die manuelle Reparatur eines Lithium-Akkus. Hat man sich dafür entschieden (oder keine andere Wahl), muss der Lötkolben angeheizt werden.
Auslöser
In meinem Fall fiel mir Anfang der Woche auf, dass mein Rasenrobbi [1] nur noch eine halbe Stunde mähen wollte, bevor er sich zum erneuten Laden für 1,5 h in seine Ladestation zurückzog. Normalerweise dauerte das Mähen und Laden jeweils eine Stunde. „Zufall?“ fragte ich mich, denn mein Misstrauen war geweckt. Der Robbi war nun knapp über vier Jahre im Dauereinsatz – da kann ein Lithium-Akku schon mal schlapp machen.
Am Nachmittag desselben Tages blickte ich neugierig aus dem Fenster, weil es längere Zeit verdächtig still war. Und siehe da: Mein Roboter stand wirklich still, mitten auf dem Rasen. Ich ging hin: Auf Tastendrücke gab es kein Lebenszeichen. Also schob ich ihn in die Ladestation. Hier erwachte er und nach Eingabe des Passworts klickte ich mich durchs Menü zum Punkt Betriebszeit. Da waren 2.938 Stunden abzulesen. Da dies fast 1.500 Ladezyklen entspricht, musste ich mich wohl demnächst um einen neuen Akku kümmern.
Das „demnächst“ trat schneller ein, als ich angenommen hatte. Nachdem der Robbi am gleichen Tag zunächst mehrere kurze Mäh- und längere Ladezyklen problemlos absolvierte, stand er am nächsten Morgen vor einem kleinen Hügel und tat nichts mehr. Auch das Verbringen in die Ladestation half nicht. Da ich den Rasen vor kurzem gedüngt hatte und wir 2021 ein schön feuchtes Frühjahr hatten, musste schnell Abhilfe geschaffen werden, denn das Gras wuchs mit enormem Tempo.
Akku wechseln?
Kurzes Googeln machte klar: Ein neuer Original-Akku kostete rund 100 €. „Geht doch noch!“ dachte ich mir. Ein Ersatz-Akku eines Drittherstellers war sogar zwischen 50 € und 65 € zu haben. Auch kein schlechter Deal, denn der gesuchte Akku hatte 18 V und eine Kapazität von 2,1 Ah. Also stecken vermutlich fünf Zellen des Formats 18650 drin. Davon wollte ich mich mit eigenen Augen überzeugen, und daher legte ich den Roboter rücklings auf einen Gartentisch und begann, den Deckel des Akkufachs zu lösen.
Doch erstens ist es nicht so einfach, und zweitens als man denkt: Nachdem sich drei von vier Schrauben problemlos lösen ließen, machte eine richtig Stress. Der Akkuschrauber brauchte mehr Drehmoment und bekam sie schließlich raus – allerdings mitsamt Einschraubmutter dran. Bei der Herstellung hatte ein Arbeiter offensichtlich die Edelstahlschraube etwas schräg und mit viel Gewalt in die Gewindegänge der Messingmutter gequält. Das Resultat zeigt Bild 1a: In der Bohrung des Kunststoffgehäuses fanden sich viele Späne durch das Rausdrehen der Einschraubmutter. Diese Mutter bekam ich dann nur mit viel Kraft von der Schraube runter. Dabei ist unten rechts etwas Messing abgebrochen (Bild 1b).

Da das Gehäuse für den Akku aber wasserdicht sein sollte, konnte ich diese Mutter nicht einfach wieder reindrehen, denn das hätte nicht gehalten. Also habe ich Zweikomponentenkleber angemischt und die Mutter in ihr Loch geklebt. Das Resultat kann man in Bild 2b bewundern. Die Messingmutter links oben sitzt so, als wenn es nie anders gewesen wäre. Nach Überwindung dieser kleinen Hürde nun zum Eigentlichen: Bild 2b zeigt ebenfalls den Akku in seiner natürlichen Behausung. Man erkennt die Silhouette von fünf Zellen. Ein Lineal bestätigte meine Vermutung: 5 x 18650. Daneben ist, wie man in Bild 2c sehen kann, viel Luft. Sofort kam mir die Idee, die Luft mit mehr Kapazität auszufüllen. Damit war meine Entscheidung gegen den Kauf eines „fertigen“ Akkus und für den Austausch der Zellen gefallen.
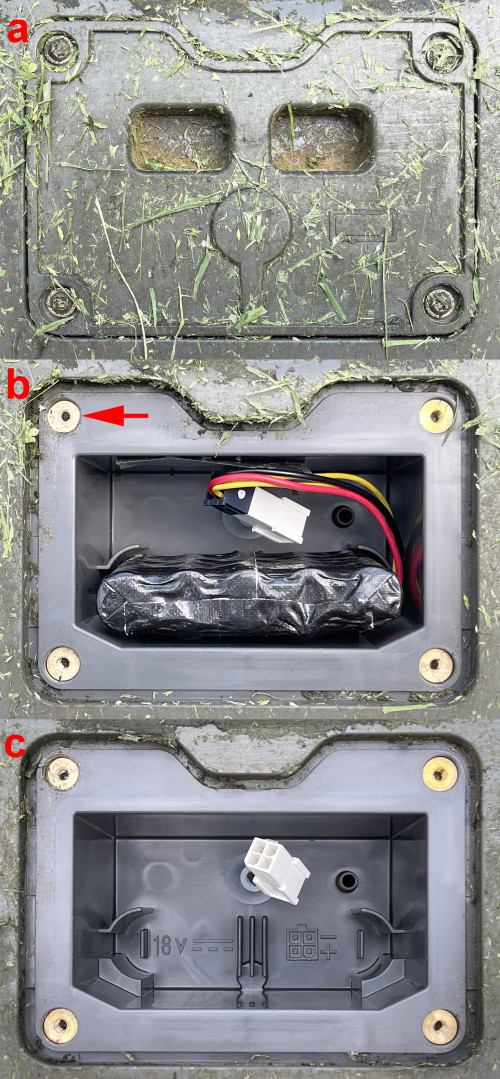
Neue Zellen
Bild 2a ist übrigens nicht redundant, denn es zeigt, dass die beiden Griffmulden im Deckel so tief sind, dass leider keine zweite Reihe Zellen mehr reinpasst. Also nichts mit zehn Zellen in 5s2p-Anordnung (fünf Zellen in Serie, jeweils zwei parallel) zur schlichten Verdoppelung der Kapazität. Aber es gibt ja (teure) Zellen im Format 18650 mit erhöhter Kapazität. Einschlägige Versender haben Zellen bis 3.500 mAh im Programm. Bei eBay, AliExpress und Co. gibt es sogar Zellen mit noch viel größerer Kapazität, doch von diesen Fantasieangaben sollte man sich nicht blenden lassen, denn HTML ist geduldig. Hochkapazitive Markenzellen hingegen kosten gut 10 € pro Stück, und da hätte ich gleich einen Fertig-Akku kaufen können.
Glücklicherweise entdeckte ich Zellen im etwas ungewöhnlicheren Format 21700. Diese waren nur wenig größer und boten doch deutlich mehr Kapazität fürs Geld. Sie müssten auch irgendwie reinpassen (mir schwebte eine Anordnung vor, die von oben wie ein W ausgesehen hätte). Außerdem kosteten sie mit „Mengenrabatt“ und Porto zusammen nur 26 € und das für Exemplare mit 4.000 mA. Also ab in den Warenkorb damit und auf „Kaufen“ geklickt. Zwei Tage später waren sie da – der Rasen hatte mittlerweile bedrohliche Halmlängen erreicht. Es war also höchste Zeit!
Überlegungen
Wer einzelne Zellen zu einem Akkupaket kombinieren will, der braucht neben etwas Fingerfertigkeit und elektrischer Expertise eigentlich etwas zum Punktschweißen. Wie man an der Auswickelzeremonie von Bild 3 sehen kann, sind die fünf grünen Zellen des alten Akkupacks schön oben und unten mit dünnem Nickelband verbunden, das punktgeschweißt ist. Diese Art der elektrischen Verbindung schont den Akku, da der Wärmeübertrag bei dieser Methode recht gering ist. Löten wird bei Akkuzellen allgemein nicht für gut befunden, da hier mehr Wärme appliziert wird. Doch für die paar Mal Gebrauch im Elektronikerleben ein Punktschweißgerät kaufen? Das wäre für meine Zwecke (und auch die vieler anderer Elektroniker) übertrieben, selbst wenn man Tools bekanntlich nie genug haben kann.
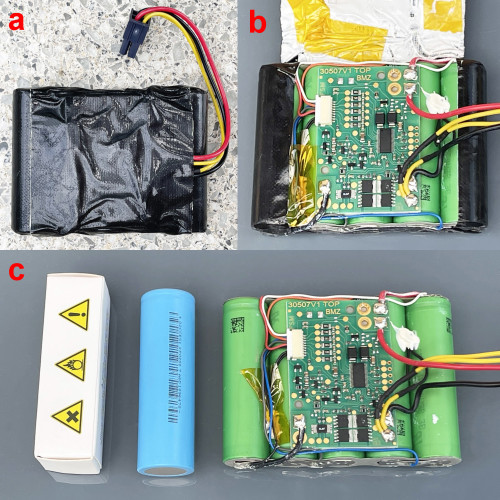
Doch zuerst zum Aufbau des Akkupacks: Das Exemplar von Bild 3 ist typisch auch für viele andere Geräte. Es besteht aus in Serie geschalteten Akkuzellen plus einem „Battery Management System“, kurz BMS. Das ist die Platine in den Bildern 3b und 3c. In letzterem Bild sieht man auch einen Größenvergleich von alten und neuen Akkuzellen. Die Aufgaben eines BMS sind dreifach:
1. Es muss die Zellen „balancieren“, das heißt, auf gleicher Spannung beziehungsweise gleichem Ladezustand halten.
2. Es soll verhindern, dass die Zellen mit zu viel Spannung überladen werden können.
3. Es soll die Last bei Unterspannung abschalten, um eine Tiefentladung zu vermeiden.
Hierfür dient der Chip mit den vielen Beinchen; ein spezialisierter Mikrocontroller, der die Zellenspannungen überwacht (links) und die Zellen bei Überspannung und Unterspannung mit Hilfe von 2 x 2 MOSFETs abschaltet (unten). Mehr zum Thema Balancing von Lithium-Akkus findet sich unter [2] und [3].
Kauft man einen neuen Akku, kommt die noch prima funktionierende BMS-Platine in den Müll. Tauscht man hingegen lediglich die Zellen, muss die Platine transplantiert werden, um die neuen Akkuzellen adäquat zu schützen. Im Kasten Ein BMS als Flipflop? ist eine zweite Hürde beschrieben, die es zuvor noch zu überwinden galt.
Ein BMS als Flipflop
Als ich den ausgepackten Akku wie in Bild 3c vor mir liegen hatte, staunte ich nicht schlecht: An den Zellen direkt gemessen lagen 19,2 V an. Das hatte ich nicht erwartet: Ein voller Akku? War doch etwas anderes defekt und ich hatte voreilig neue Akkuzellen bestellt? Am Stecker des Akkus und an den entsprechenden Anschlüssen rechts der BMS-Platine waren hingegen nur etwa 18,5 V zu messen – allerdings sehr hochohmig. Zwei Finger reichten schon, um die Spannung am Ausgang auf wenige Volt zusammenbrechen zu lassen. Also war das BMS kaputt?
Mit Stirnrunzeln versuchte ich zunächst, den Akku direkt an seinen Polen zu belasten. An 24 Ω waren bei rund 0,75 A immer noch gut 18,2 V zu messen. Ein Ladeversuch über den Stecker klärte das merkwürdige Verhalten auf. Nach nur wenigen Sekunden des Ladens mit 0,5 A blieb auch am Stecker des Akkus die Spannung niederohmig erhalten. Ergo war die Spannung bei einem weichen Akku am Ende seines Lebens wohl zu tief gesunken - das BMS hatte dann abgeschaltet und sich den Zustand einfach gemerkt. Ich konnte das reproduzieren, indem ich den Akku mit 12 Ω belastete. Nach fünf Minuten schaltete das BMS bei knapp über 13 V ab. Einmal Laden und es schaltete den Akku wieder ein.
Das BMS war also nicht defekt (seufz!) und ich konnte den Umbau des Akkus bedenkenlos starten...
Löten?
In Ermangelung eines passenden kleinen Punktschweißgeräts entschloss ich mich, die Verbindungen in Form von Litze direkt an die Akkupole zu löten. Wenn man weiß, was man tut, klappt das, ohne die Akkus zu schädigen. Da ein potentieller Schaden durch unerwünschte chemische Vorgänge in den Zellen in etwa proportional zum Integral aus Zeit und Temperatur ist, empfiehlt es sich, schnell und zügig zu löten, damit der Lötvorgang schon beendet ist, bevor sich die innere Chemie nennenswert aufzuheizen beginnt. Dabei sind drei Dinge wichtig: Der Lötkolben muss genug Leistung haben, die Temperatur der Lötspitze muss hoch genug sein (um die darin gespeicherte Wärmeenergie in kurzer Zeit zu übertragen) und das Lötzinn muss gut und bei nicht zu hoher Temperatur schmelzen. Mein Lötkolben wird mit 90 W geheizt und lässt sich auf über 400 °C einstellen – das passt. Außerdem sollte man so ein Manöver nicht mit modernem, bleifreiem Lot versuchen, denn das braucht eine höhere Temperatur und benetzt Oberflächen nicht so schön wie das von mir präferierte, gute alte SnPb 60/40. Die Metalloberflächen der Pole von Lithiumzellen lassen sich meiner Erfahrung nach gut löten. Ich brauchte bei einer Lötspitzentemperatur von 385 °C und 1 mm starkem, bleihaltigem Lötzinn mit Flussmittelseele etwa 1 s pro Lötstelle. Das ist schnell genug.
Wenn man diese Regeln beherzigt, ist das Löten an Lithium-Zellen ungefährlich. Wenn man aber zu lange (wegen zu schwachem Lötkolben, zu niedriger Temperatur oder bleifreiem Lot) auf dem Metallgehäuse einer Lithium-Zelle herumfuhrwerkt, wird deren Kapazität oder mögliche Zyklenzahl leiden. Im Sekundenbereich wird einem die Zelle nicht gleich um die Ohren fliegen. Alternativ könnte man auch leicht teurere Zellen mit angeschweißten Fahnen ordern und nur an den Enden dieser Metallstreifen löten. Das ist im Prinzip sicherer, aber man muss die überstehenden Fahnen dann sehr gut isolieren. Kurzschlüsse sind deutlich gefährlicher als kurzes direktes Löten.
Bild 4 zeigt meine Löttechnik. Der Pluspol hat eine erhabene, schlecht wärmeleitende Kappe, die nur an drei Stellen mit dem eigentlichen Pol verbunden ist. Hier ist die Wärmeempfindlichkeit nicht so hoch. Man bringt also zunächst an allen Pluspolen kleine Lötzinntropfen auf (Bild 4a), die man dann später nach Abkühlung zum Blitzlöten benutzt. Auf die Minuspole lötet man direkt kleine Litzenstücke passender Länge (Bild 4b). Letzteres kann man in zwei Durchgängen erledigen: Erst alle Minuspole mit einem Lötzinntropfen versehen und nach Abkühlung im zweiten Durchgang die vorher verzinnten Litzenstücke anlöten. Damit man etwas Spielraum hat, können diese etwas länger sein als nötig. Ich habe Litzenstücke von etwa 3 cm Länge mit einem Querschnitt von 1,5 mm2 verlötet. Hier sollte man zügig arbeiten. In Bild 4c ist zu sehen, dass jeweils ein Pluspol eines anderen Akkus ans andere Litzenende gelötet wurde, um die Zellen in Serie zu schalten. Das dünnere rote Litzenstück führt zu den Messstrippen für die einzelnen Zellenspannungen des BMS.
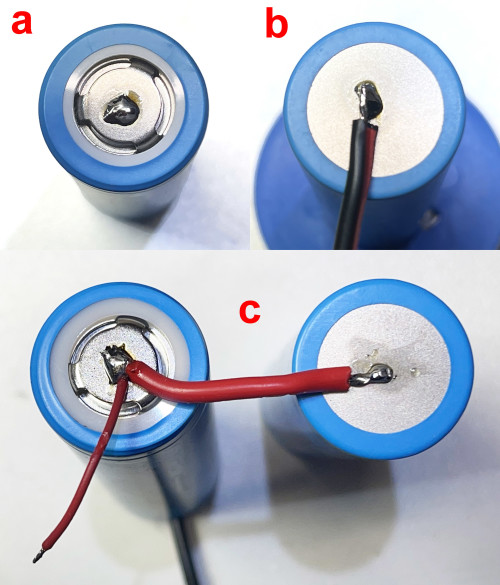
Zusammenbau und Test
Wie schon angedeutet, hatte ein Zellenpaket in W-Anordnung einfach keinen Platz. Aber man muss nur einmal um die Ecke denken, dann klappt das schon: Wie Bild 5 zeigt, habe ich einfach vier Zellen nebeneinander gelegt sowie vorsichtig und Stück für Stück mit Heißkleber fixiert. Die fünfte Zelle kam einfach quer auf den Rücken. Dank Heißkleber wird diese Struktur sehr stabil. Wer schonender vorgehen will, nimmt Silikon statt Heißkleber.
Die BMS-Platine hatte auf der Rückseite doppelseitiges Klebeband, was auch auf dem neuen Akkupack gut hielt. Nun mussten nur noch die sechs Leitungen des weißen Steckers (Bild 5b) an die jeweiligen Zellenpole, sowie Plus- und Minuspol des Gesamtpacks an die BMS-Platine - dann konnte der neue Akku getestet werden. Beim Zusammenbau sollte man sorgfältig arbeiten und keine Fehler machen – ein paar Fotos vom alten Akku helfen bei Unsicherheiten. Bei mir funktionierte alles direkt und der Akku ließ sich problemlos laden und entladen. Etwas anderes hätte ich auch nicht erwartet ;-).
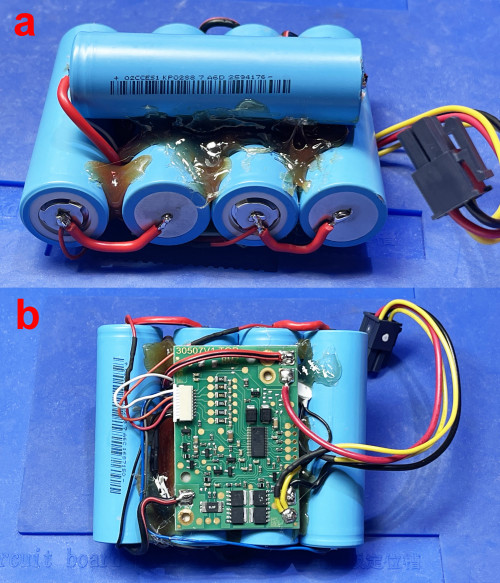
Zur besseren mechanischen Stabilität, Isolierung und Feuchteresistenz wurde das fertige Akkupaket dann noch mit kräftigem Gaffer-Tape beklebt (Bild 6) und das Resultat in den Roboter gesteckt – alles passte. Nach Zuschrauben des Batteriefachs und Einschalten wollte der Rasenroboter sich zuerst mit den Signalen des Leitkabels kalibrieren und dann direkt loslegen. Ich habe Letzteres aber abgebrochen und ihn zunächst in die Ladestation gesteckt. Dort lud er volle drei Stunden – ein Indiz dafür, dass der Akku jetzt fast die doppelte Kapazität des Originals hat.
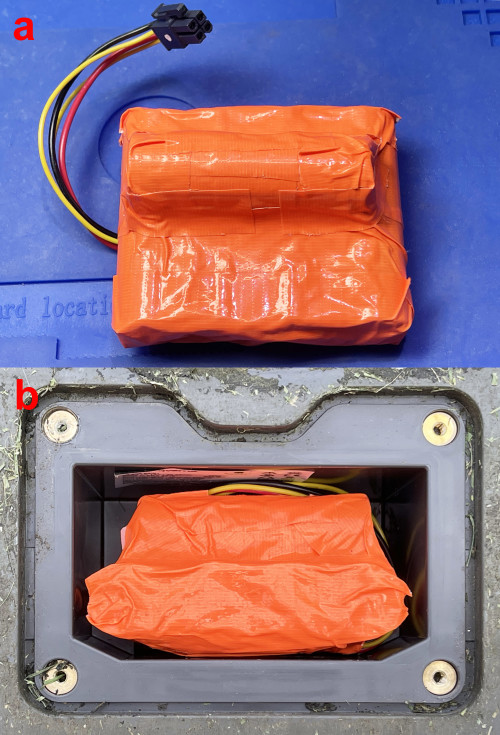
Der Roboter mäht mittlerweile genauso schön wie die Jahre zuvor: Eine Stunde Mähen gefolgt von einer Stunde Laden. Der Akku wird also nur teilentladen. Dadurch kann ich begründet davon ausgehen, dass die größere Kapazität zu deutlich mehr Ladezyklen führen wird, bis der Akku das nächste Mal schlapp macht. Durch die relativ zur Kapazität kleineren Zyklen sollte er sogar überproportional lange halten. Ich rechne mit gut der doppelten Lebensdauer des Originals. Trifft das zu, hat sich der Aufwand von etwa drei Stunden Basteln gelohnt. Der Stundenlohn ist zwar nicht besonders gut, aber dafür habe ich einen Akku, den man so nicht kaufen kann!
Diese Art des Akkureparierens ist übrigens nicht auf Rasenmäher beschränkt. Sie eignet sich auf ähnliche Weise auch zur Verlängerung der Laufzeit von Akku-Staubsaugern und anderen Geräten, selbst wenn da die Platzverhältnisse nicht ganz so großzügig sind. Der letzte Staubsauger, den ich mit der Methode (aber hochkapazitiven 18650er Zellen) repariert habe, läuft schon drei Jahre ohne Beanstandung.
Sie haben Fragen oder Kommentare?
Bei technischen Fragen können Sie sich gern an die Elektor-Redaktion wenden unter der E-Mail-Adresse redaktion@elektor.de.
Diskussion (13 Kommentare)