Windkraftanlage mit supraleitender Rotorwicklung
04. Dezember 2018
über
über
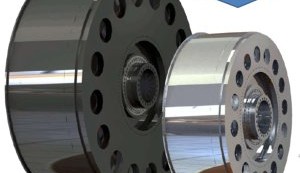
Eine Windturbine an der dänischen Küste bei Thyborøn bietet eine Weltneuheit: Der konventionelle Generatorrotor mit Permanentmagneten wurde durch einen Rotor mit Supraleitern ersetzt. Die neue Turbine ist nur halb so schwer, viel kompakter und liefert dennoch die gleiche Leistung wie eine herkömmliche.
Die Supraleiter ersetzen die Permanentmagnete einer konventionellen Windturbine durch Rotorspulen aus supraleitendem Draht. Diese leistungsstarken Magnete sind noch viel leichter und kompakter als herkömmliche und kommen zudem mit sehr viel weniger Seltene-Erden-Metallen aus. Die leichtere Turbine hat den zusätzlichen Vorteil, dass die Turmkonstruktion leichter ausgeführt werden kann. Dies bietet nicht nur beim (Straßen-) Transport erhebliche Vorteile.
Nach zweijährigen Tests im Labor kam im Spätsommer 2018 alles zusammen: Der Generator mit einem Durchmesser von vier Metern – fast eineinhalb Meter weniger als die konventionelle Version – wurde nach Bodentests am Fraunhofer Institut für Windenergie und Energiesysteme in Bremerhaven nach Thyborøn verschifft. Dort wurde sie in ein GC1-Windrad des Herstellers Envision eingebaut, das 3,6 MW liefert und über zwei Rotorblätter mit einem Gesamtdurchmesser von 128 m verfügt.
Supraleiter
Normalerweise funktionieren die (permanententerregten) Generatoren moderner Windkraftanlagen wie klassische Fahrraddynamos: Ein Rotor mit Permanentmagneten dreht sich in einem Stator mit Spulen, die die magnetische in elektrische Energie umwandeln. Für die Permanentmagneten werden üblicherweise Seltene-Erden-Metalle wie Neodym eingesetzt, damit der Generator möglichst leicht und kompakt gebaut werden kann. Doch diese Seltene Erden sind sehr problematisch in Hinblick auf Verfügbarkeit, Umweltschäden und Gewinnungsbedingungen (Sklaverei) in der dritten Welt.Die Supraleiter ersetzen die Permanentmagnete einer konventionellen Windturbine durch Rotorspulen aus supraleitendem Draht. Diese leistungsstarken Magnete sind noch viel leichter und kompakter als herkömmliche und kommen zudem mit sehr viel weniger Seltene-Erden-Metallen aus. Die leichtere Turbine hat den zusätzlichen Vorteil, dass die Turmkonstruktion leichter ausgeführt werden kann. Dies bietet nicht nur beim (Straßen-) Transport erhebliche Vorteile.
Supraleitendes Band
Supraleiter leiten Strom ohne Widerstand. Dies ermöglicht große Ströme und starke Magnetfelder. Allerdings müssen Supraleiter sehr stark gekühlt werden. Die Magnete im neuen Rotor bestehen aus einem supraleitendem Band: Eine dünne Schicht aus supraleitendem Material wurde auf einen flexiblen Stahlträger aufgebracht, um den Strom zu leiten. Dieses Band, das zunächst nur im Labormaßstab hergestellt werden konnte, lässt sich nun kilometerweise produzieren. Doppelbestückte kompakte Kryokühler rotieren mit dem Rotor und sorgen für eine Temperatur von –240°C.Eiseskälte
In diesem Projekt sorgte die Universität Twente für alles, was kalt war: das Testen der Bänder und Magnetspulen, die Erforschung der optimalen Kühlung und den Zusammenbau des Rotors als Ganzes.Nach zweijährigen Tests im Labor kam im Spätsommer 2018 alles zusammen: Der Generator mit einem Durchmesser von vier Metern – fast eineinhalb Meter weniger als die konventionelle Version – wurde nach Bodentests am Fraunhofer Institut für Windenergie und Energiesysteme in Bremerhaven nach Thyborøn verschifft. Dort wurde sie in ein GC1-Windrad des Herstellers Envision eingebaut, das 3,6 MW liefert und über zwei Rotorblätter mit einem Gesamtdurchmesser von 128 m verfügt.
Mehr anzeigen
Weniger anzeigen
Diskussion (1 Kommentar)